Annealing is a heat treatment process primarily used to alter the microstructure of a material to improve its properties, such as ductility, machinability, and workability. However, it does not strengthen a material in the traditional sense of increasing hardness or tensile strength. Instead, annealing reduces hardness, relieves internal stresses, and increases ductility, making the material easier to work with and less prone to cracking or failure during manufacturing or service. The process involves heating the material to a specific temperature, holding it at that temperature, and then cooling it in a controlled manner. While annealing may not directly strengthen a material, it can indirectly enhance its performance by improving its uniformity and reducing defects.
Key Points Explained:
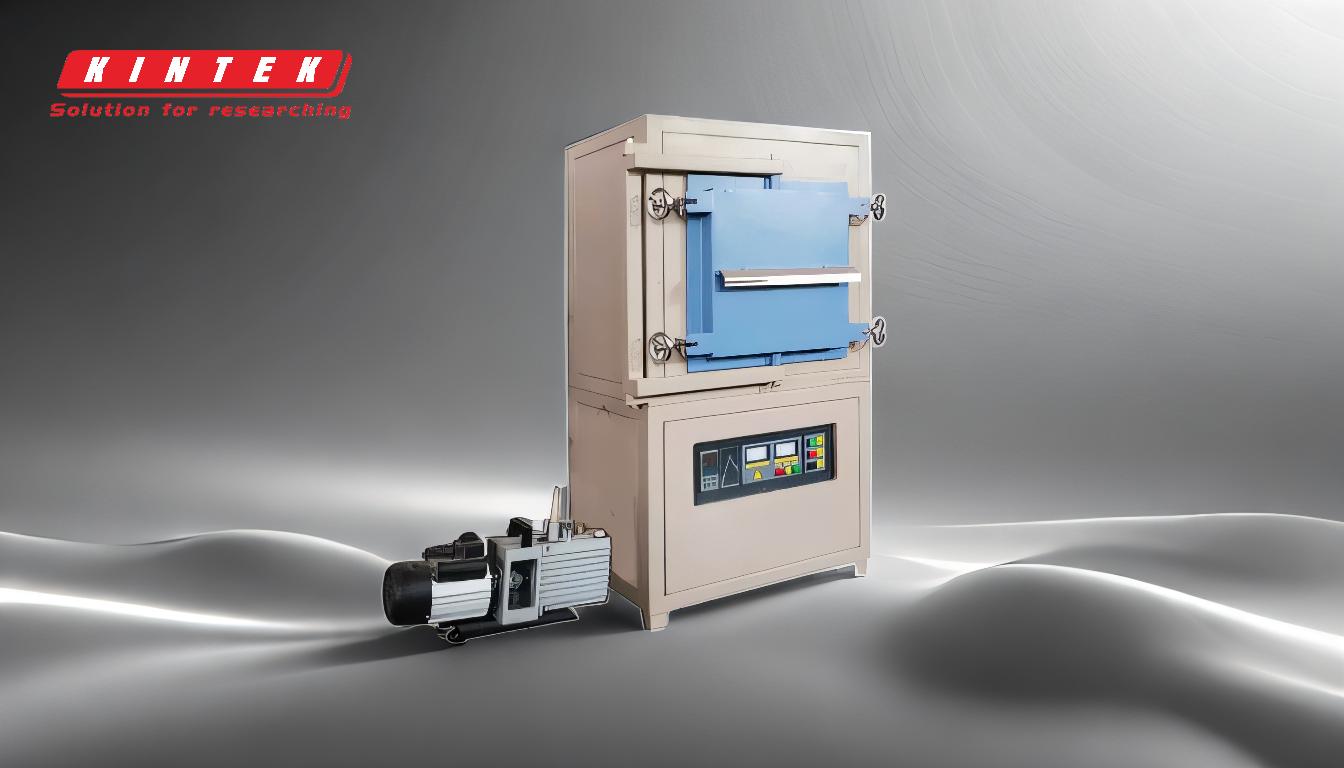
-
Purpose of Annealing:
- Annealing is primarily used to improve the ductility, machinability, and workability of a material.
- It is not designed to increase hardness or tensile strength but rather to make the material more uniform and less brittle.
-
Effect on Hardness and Strength:
- Annealing reduces the hardness of a material by allowing the microstructure to reorganize into a more stable and less stressed state.
- This reduction in hardness is accompanied by an increase in ductility, which makes the material easier to shape or machine.
-
Relief of Internal Stresses:
- One of the key benefits of annealing is the elimination of internal stresses that can lead to failure during manufacturing or service.
- By relieving these stresses, annealing helps prevent cracking, warping, or other forms of material failure.
-
Improvement in Workability:
- Annealing makes materials more workable by increasing their ductility and reducing their brittleness.
- This is particularly important for materials that undergo extensive machining, forming, or shaping processes.
-
Controlled Heating and Cooling:
- The annealing process involves heating the material to a specific temperature, holding it at that temperature for a set period, and then cooling it in a controlled manner.
- This controlled cooling is crucial to achieving the desired microstructure and properties.
-
Indirect Strengthening:
- While annealing does not directly increase a material's strength, it can indirectly enhance its performance by improving its uniformity and reducing defects.
- A more uniform and defect-free material is less likely to fail under stress, which can be seen as a form of strengthening in certain applications.
-
Applications of Annealing:
- Annealing is commonly used in the manufacturing of steels, where it helps improve machinability and reduce internal stresses.
- It is also used in the production of electrical components, where it can enhance electrical properties and reduce brittleness.
-
Trade-offs:
- The primary trade-off with annealing is the reduction in hardness and strength in exchange for increased ductility and workability.
- This makes annealing unsuitable for applications where high hardness or strength is required, but it is ideal for processes that involve extensive shaping or machining.
In summary, annealing does not strengthen a material in the conventional sense but rather improves its ductility, workability, and uniformity. This makes it an essential process in many manufacturing and material processing applications, where the goal is to create a material that is easier to work with and less prone to failure.
Summary Table:
Aspect | Effect of Annealing |
---|---|
Purpose | Improves ductility, machinability, and workability; reduces brittleness. |
Hardness & Strength | Reduces hardness and strength; increases ductility. |
Internal Stresses | Relieves internal stresses, preventing cracking or failure. |
Workability | Enhances workability for machining, forming, and shaping processes. |
Heating & Cooling | Controlled heating and cooling to achieve desired microstructure and properties. |
Indirect Strengthening | Improves uniformity and reduces defects, indirectly enhancing performance. |
Applications | Used in steel manufacturing and electrical component production. |
Trade-offs | Reduced hardness and strength for increased ductility and workability. |
Learn more about how annealing can optimize your material processing—contact our experts today!