Crucible size is a critical factor in determining the efficiency, safety, and success of various processes, whether in metal melting, chemical reactions, or other high-temperature applications. The size of a crucible directly impacts its compatibility with the furnace, the sample dimensions, and the overall process requirements. A crucible that is too small may not accommodate the sample or allow for proper heat distribution, while one that is too large may lead to inefficiencies or safety hazards. Additionally, the size must align with the furnace's capacity and the specific operational needs, such as temperature control, alloy compatibility, and process requirements. Therefore, selecting the right crucible size is essential for optimizing performance and ensuring the desired outcomes in any application.
Key Points Explained:
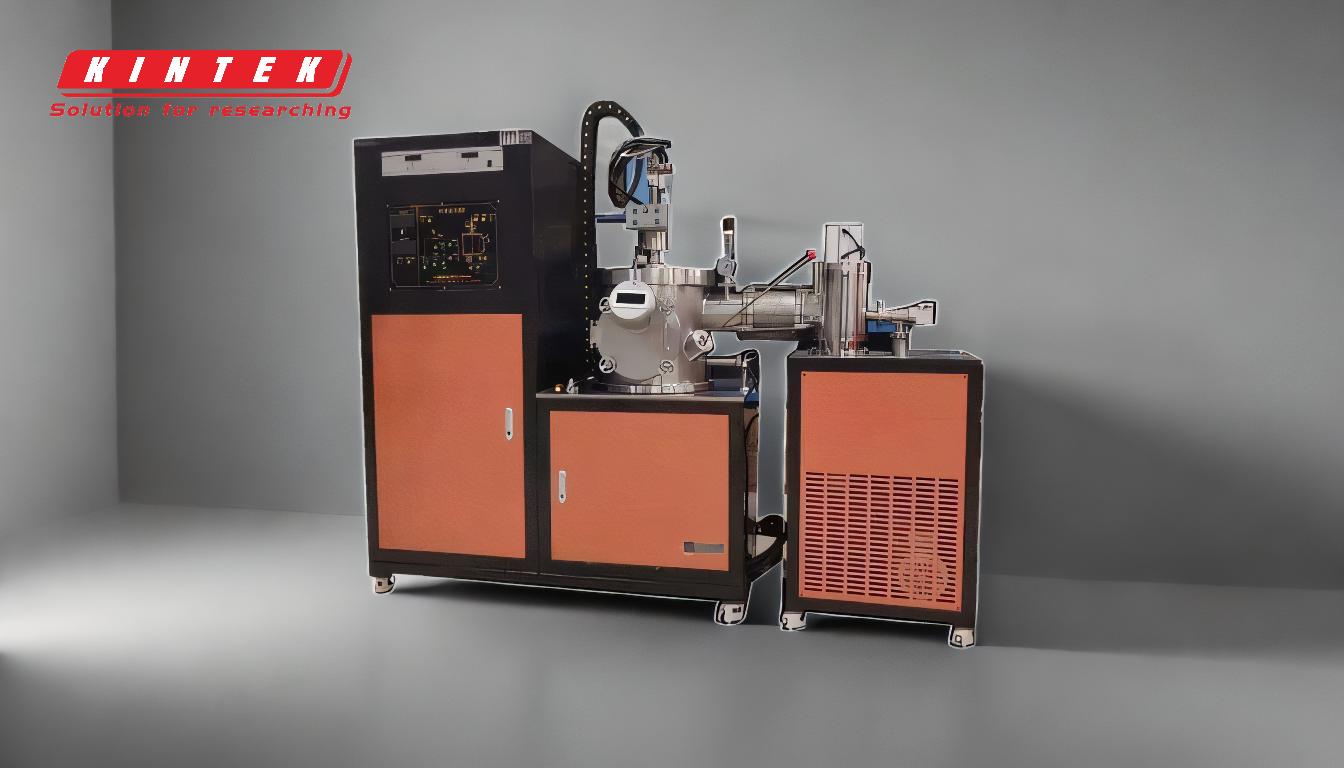
-
Crucible Size and Sample Dimensions:
- The crucible must be large enough to accommodate the sample being processed. If the sample is too large for the crucible, it may not fit properly, leading to uneven heating or incomplete reactions.
- For example, in metal melting, a crucible that is too small may not hold enough material, while in chemical reactions, a sample that overflows the crucible could lead to contamination or safety issues.
-
Compatibility with Furnace Dimensions:
- The crucible size must match the furnace's internal dimensions. A crucible that is too large for the furnace may not fit, while one that is too small may not utilize the furnace's heating capacity efficiently.
- Ensuring the crucible fits properly within the furnace is crucial for even heat distribution and optimal performance.
-
Impact on Heat Distribution and Process Control:
- The size of the crucible affects how heat is distributed across the sample. A low and wide crucible is ideal for melting metals because it provides an even heating surface.
- In contrast, a tall and narrow crucible is better suited for chemical reactions, as it reduces the surface area exposed to heat, making it easier to control the reaction and minimize evaporation.
-
Temperature Considerations:
- The crucible size can influence the rate at which the sample reaches the desired temperature. A larger crucible may require more time to heat up, while a smaller one may heat too quickly, potentially causing thermal shock.
- The material of the crucible also plays a role, as it must withstand the furnace's maximum temperature. For example, a Zirconia crucible is suitable for temperatures above 2100°C.
-
Operational Efficiency and Safety:
- Choosing the right crucible size ensures that the process runs efficiently, minimizing energy waste and reducing the risk of accidents.
- A crucible that is too large may lead to unnecessary energy consumption, while one that is too small could result in spillage or overheating.
-
Process-Specific Requirements:
- Different processes have unique requirements that influence the choice of crucible size. For example, in metal melting, factors such as the type of alloy, melting temperature, and pouring arrangements must be considered.
- In chemical reactions, the crucible size must allow for proper mixing, degassing, and slag removal, depending on the specific reaction being carried out.
-
Avoiding Cross-Contamination:
- In applications where multiple alloys or chemicals are processed, the crucible size must be chosen to prevent cross-contamination. Using a crucible that is too large for a small sample may leave residues that could affect subsequent processes.
-
Economic Considerations:
- Selecting the appropriate crucible size can also have economic implications. A crucible that is too large may be more expensive and less cost-effective, while one that is too small may require frequent replacements, increasing operational costs.
In conclusion, crucible size is a critical factor that must be carefully considered to ensure compatibility with the furnace, sample dimensions, and specific process requirements. By selecting the right size, you can optimize performance, enhance safety, and achieve the desired outcomes in your application.
Summary Table:
Key Factor | Impact |
---|---|
Sample Dimensions | Ensures proper fit and avoids overflow or contamination. |
Furnace Compatibility | Matches furnace dimensions for even heat distribution. |
Heat Distribution | Low and wide for metals; tall and narrow for chemical reactions. |
Temperature Control | Influences heating rate and thermal shock risks. |
Operational Efficiency | Minimizes energy waste and reduces safety hazards. |
Process-Specific Requirements | Tailored to alloy type, melting temperature, and reaction needs. |
Cross-Contamination Prevention | Prevents residue buildup for multi-sample processes. |
Economic Considerations | Balances cost-effectiveness with operational needs. |
Need help selecting the right crucible size for your application? Contact our experts today for tailored solutions!