Deposition processes can vary significantly depending on the method used, but heat often plays a critical role in influencing the quality, rate, and characteristics of the deposited film. While not all deposition techniques strictly require heat, many benefit from controlled temperatures to optimize film properties such as density, composition, and adhesion. Heat can enhance surface reactions, improve film quality, and increase deposition rates in methods like thermal evaporation. However, the necessity of heat depends on the specific deposition technique and the desired film properties. For instance, higher temperatures generally lead to denser films but may also impose limitations based on the substrate or application requirements.
Key Points Explained:
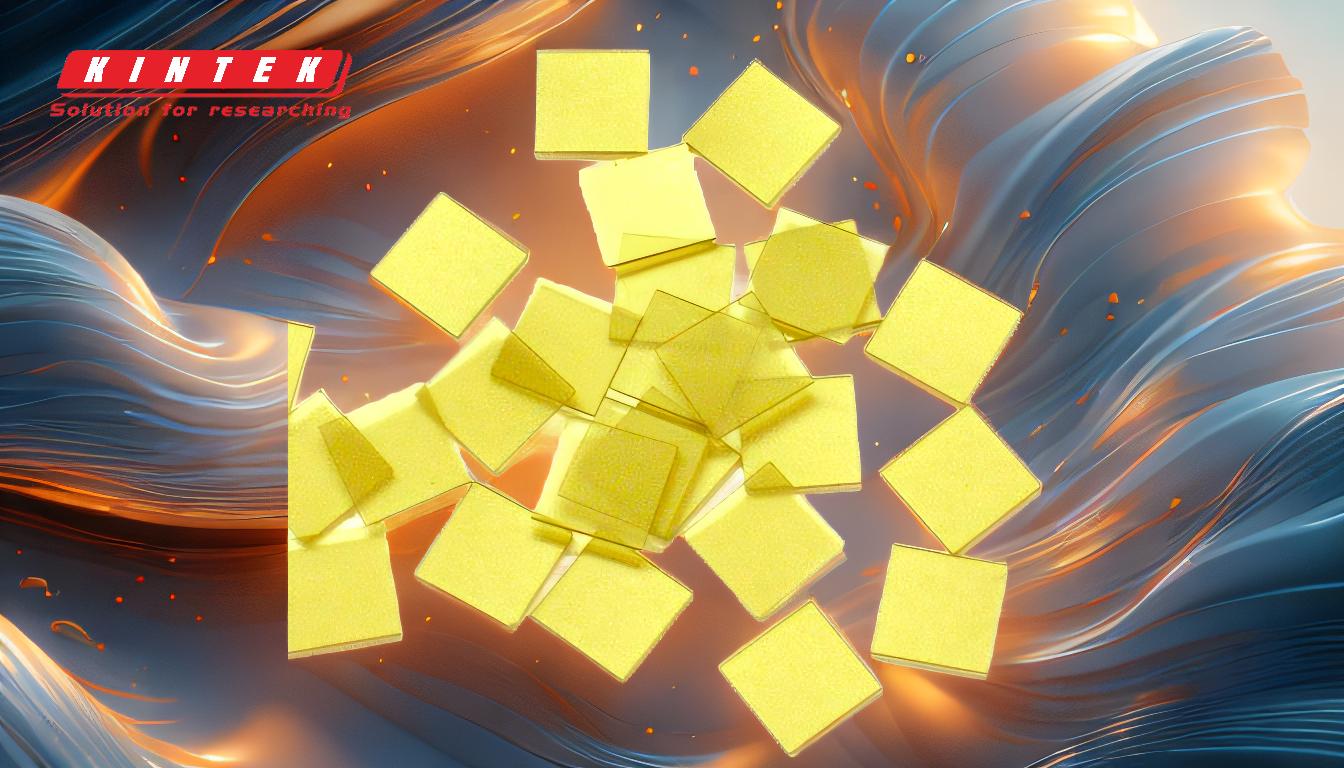
-
Role of Heat in Deposition Processes:
- Heat is often used to improve the quality and characteristics of deposited films. For example, higher substrate temperatures can enhance surface reactions, leading to denser and more uniform films.
- In thermal evaporation, increased temperature raises the vapor pressure of the material, resulting in higher deposition rates as more material is vaporized and deposited on the substrate.
-
Impact of Temperature on Film Properties:
- Higher temperatures generally improve film quality by promoting better adhesion, denser structures, and improved composition. This is because heat facilitates atomic mobility and surface diffusion, leading to more stable and uniform films.
- However, excessive heat can alter film properties or damage temperature-sensitive substrates, so temperature control is critical to balance quality and application constraints.
-
Deposition Rate and Temperature:
- In many deposition methods, such as thermal evaporation, higher temperatures correlate with higher deposition rates due to increased vapor pressure and material vaporization.
- For other techniques like chemical vapor deposition (CVD), temperature influences the rate of chemical reactions, which in turn affects deposition rates and film properties.
-
Heat as a Variable in Different Deposition Techniques:
- Thermal Evaporation: Heat is essential to vaporize the material, making it a key factor in this method.
- Sputtering: While sputtering can be performed at lower temperatures, heating the substrate can improve film quality and adhesion.
- Chemical Vapor Deposition (CVD): Heat is often required to drive the chemical reactions necessary for film formation.
- Physical Vapor Deposition (PVD): Some PVD techniques, like electron beam evaporation, rely on heat to vaporize materials, while others, like magnetron sputtering, may not require significant heating.
-
Substrate Temperature and Film Quality:
- Substrate temperature has a significant impact on film quality, even if it does not always affect the deposition rate. Higher temperatures can lead to denser films with fewer defects, as they promote better atomic arrangement and surface reactions.
- For temperature-sensitive substrates, lower temperatures or alternative deposition methods may be necessary to avoid damage.
-
Balancing Heat with Application Requirements:
- The application often dictates the temperature limits for deposition. For example, in semiconductor manufacturing, excessive heat can damage delicate components, so deposition processes must be carefully controlled.
- In contrast, applications requiring high-performance coatings, such as aerospace components, may benefit from higher temperatures to achieve superior film properties.
-
Alternative Approaches for Low-Temperature Deposition:
- Some deposition techniques, such as plasma-enhanced chemical vapor deposition (PECVD), allow for film formation at lower temperatures by using plasma to drive chemical reactions instead of relying solely on heat.
- These methods are particularly useful for depositing films on temperature-sensitive substrates, such as polymers or biological materials.
In summary, while heat is not always strictly required for deposition, it is a critical factor in many processes to achieve desired film properties. The necessity of heat depends on the specific deposition technique, the material being deposited, and the application's temperature constraints. By carefully controlling temperature, manufacturers can optimize deposition rates, film quality, and overall performance.
Summary Table:
Aspect | Details |
---|---|
Role of Heat | Enhances surface reactions, improves film quality, and increases deposition rates. |
Impact on Film Properties | Higher temperatures lead to denser films, better adhesion, and fewer defects. |
Deposition Rate | Increased temperature often results in higher deposition rates. |
Techniques Requiring Heat | Thermal Evaporation, Chemical Vapor Deposition (CVD), some PVD methods. |
Low-Temperature Alternatives | Plasma-enhanced CVD (PECVD) for temperature-sensitive substrates. |
Application Considerations | Temperature limits depend on substrate and application requirements. |
Ready to optimize your deposition process? Contact our experts today for tailored solutions!