Heat treatment is a process used to alter the physical and mechanical properties of metals, but it does not change their chemical composition. Instead, it modifies the microstructure of the metal, which in turn affects properties like hardness, strength, toughness, ductility, and elasticity. The process involves heating the metal to a specific temperature, holding it at that temperature for a certain period, and then cooling it at a controlled rate. These steps influence the arrangement of atoms within the metal, leading to changes in its mechanical behavior without altering its chemical makeup.
Key Points Explained:
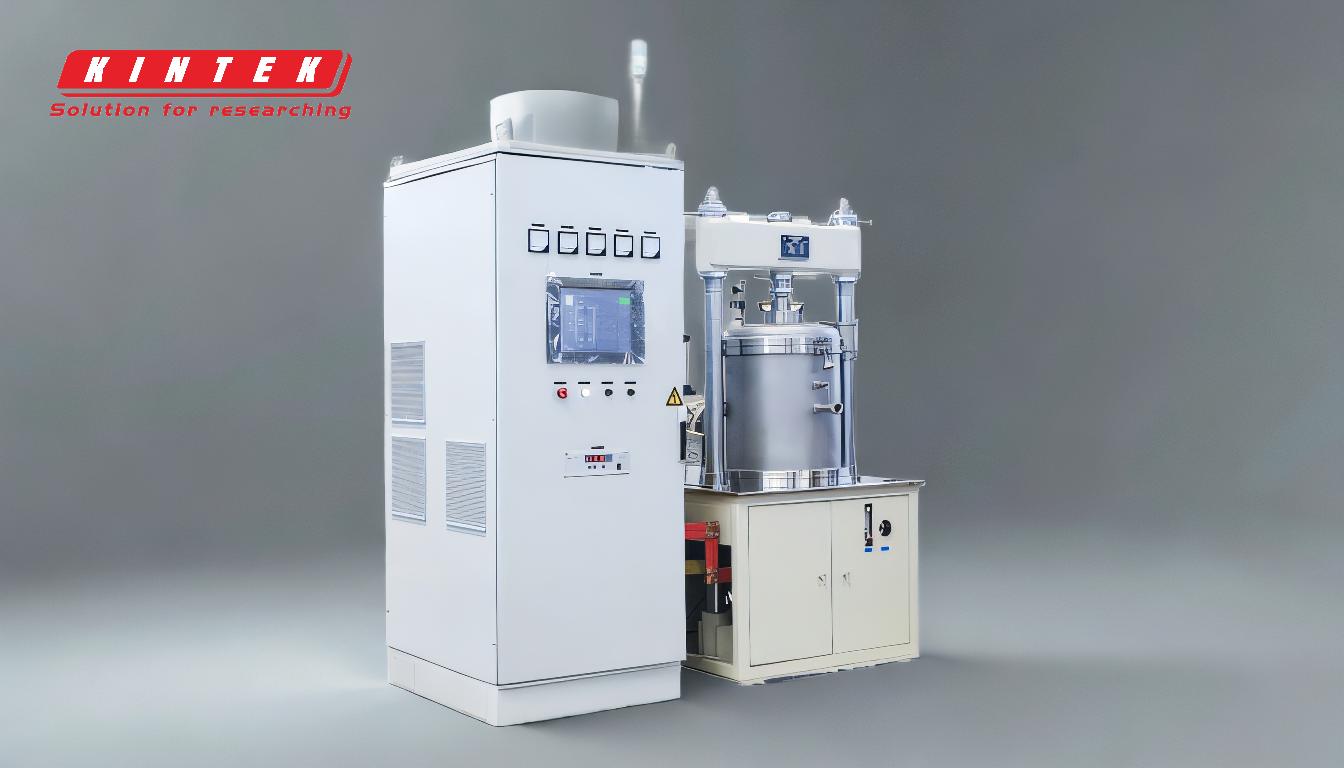
-
Definition of Heat Treatment:
- Heat treatment involves heating a metal to a specific temperature, holding it there for a set duration, and then cooling it in a controlled manner.
- The primary goal is to alter the metal's microstructure to achieve desired mechanical properties.
-
Chemical Composition Remains Unchanged:
- Heat treatment does not change the chemical composition of the metal. The elements and their proportions remain the same before and after the process.
- The process only affects the physical arrangement of atoms within the metal, not the chemical bonds or the elements themselves.
-
Microstructural Changes:
- The microstructure of the metal, which includes grain size, phase distribution, and defect density, is altered during heat treatment.
- These changes influence the metal's mechanical properties, such as hardness, strength, and ductility.
-
Mechanical Properties Affected:
- Hardness: Increased by processes like quenching, which rapidly cools the metal to form a harder microstructure.
- Strength: Enhanced by processes like tempering, which reduces brittleness while maintaining strength.
- Toughness and Ductility: Improved by annealing, which involves slow cooling to make the metal more ductile and less brittle.
-
Types of Heat Treatment:
- Annealing: Heats the metal to a high temperature and then slowly cools it to increase ductility and reduce hardness.
- Quenching: Rapidly cools the metal to increase hardness and strength.
- Tempering: Reheats the quenched metal to a lower temperature to reduce brittleness while maintaining strength.
-
Applications of Heat Treatment:
- Used in industries like automotive, aerospace, and manufacturing to enhance the performance of metal components.
- Common applications include hardening gears, increasing the durability of tools, and improving the fatigue resistance of structural components.
In summary, heat treatment is a powerful method for modifying the mechanical properties of metals without altering their chemical composition. By controlling the heating and cooling processes, manufacturers can tailor the microstructure of metals to meet specific performance requirements, making heat treatment an essential process in various industrial applications.
Summary Table:
Aspect | Details |
---|---|
Definition | Heating, holding, and cooling metal to alter microstructure and properties. |
Chemical Composition | Remains unchanged; only microstructure is modified. |
Properties Affected | Hardness, strength, toughness, ductility, and elasticity. |
Types | Annealing, quenching, tempering. |
Applications | Automotive, aerospace, manufacturing (e.g., gears, tools, structural parts). |
Learn how heat treatment can optimize your metal components—contact our experts today!