Yes, induction heating works with copper. Induction heating is a process that uses electromagnetic induction to generate heat within a conductive material, such as metals. Copper, being a highly conductive metal, is well-suited for induction heating. This method is widely used for melting, heating, and processing copper and its alloys due to its efficiency, precision, and ability to generate localized heat.
Key Points Explained:
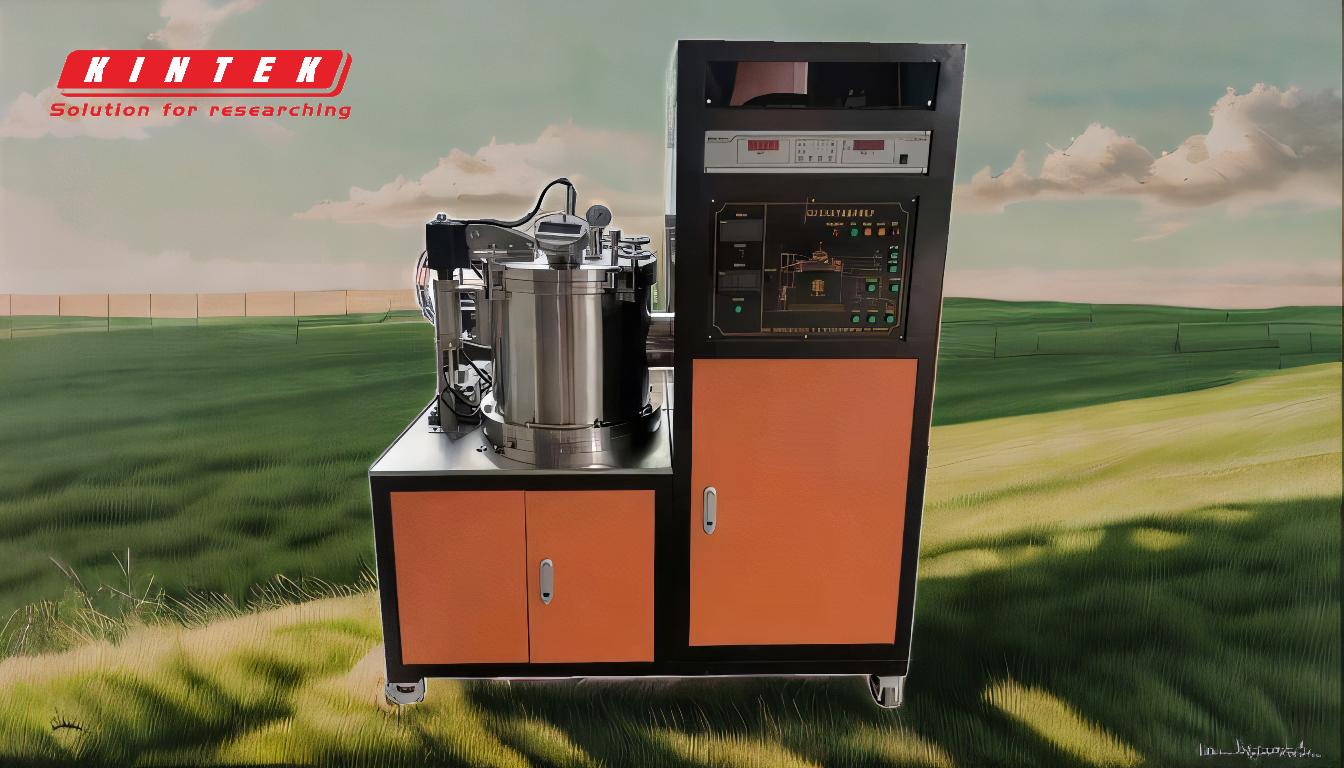
-
How Induction Heating Works:
- Induction heating relies on electromagnetic induction to generate heat in conductive materials.
- An alternating magnetic field is created by passing an alternating current through a coil (inductor).
- When a conductive material like copper is placed within this magnetic field, eddy currents are induced within the material.
- The resistance of the material to these eddy currents generates heat, which is localized and controllable.
-
Why Copper is Suitable for Induction Heating:
- Copper is an excellent conductor of electricity, making it highly responsive to induction heating.
- Its high electrical conductivity allows for efficient heat generation when exposed to an alternating magnetic field.
- Copper's thermal conductivity ensures even heat distribution, which is beneficial for processes like melting or annealing.
-
Applications of Induction Heating for Copper:
- Melting: Induction heating is widely used to melt copper and its alloys (e.g., brass, bronze) in industrial and jewelry-making applications.
- Annealing: Copper wires and sheets are often annealed using induction heating to improve ductility and reduce hardness.
- Brazing and Soldering: Induction heating is used to join copper components with precision and minimal heat exposure to surrounding areas.
- Surface Heating: Induction heating can be used for localized heating of copper parts for specific manufacturing processes.
-
Advantages of Induction Heating for Copper:
- Efficiency: Induction heating directly heats the copper, minimizing energy loss and reducing heating times.
- Precision: The heat is localized, allowing for precise control over the heating process.
- Cleanliness: Induction heating does not require combustion, making it a cleaner process compared to traditional heating methods.
- Safety: Since the heat is generated within the material, there is no open flame or external heat source, reducing safety risks.
-
Considerations for Induction Heating with Copper:
- Frequency Selection: The frequency of the alternating current affects the depth of heat penetration. Higher frequencies are typically used for surface heating, while lower frequencies are better for deeper heating or melting.
- Power Requirements: Copper's high conductivity means it requires sufficient power to generate the necessary heat, especially for melting.
- Cooling: Proper cooling systems are essential to prevent overheating of the induction coil and ensure consistent performance.
-
Comparison with Other Heating Methods:
- Furnace Heating: Induction heating is faster and more energy-efficient than traditional furnace heating, especially for small-scale or precision applications.
- Flame Heating: Induction heating eliminates the need for open flames, reducing contamination and improving safety.
- Resistance Heating: While resistance heating also uses electric currents, induction heating is more efficient and provides better control over the heating process.
In summary, induction heating is highly effective for working with copper due to its conductive properties. It offers numerous advantages, including efficiency, precision, and cleanliness, making it a preferred method for melting, annealing, and other thermal processing applications involving copper and its alloys.
Summary Table:
Aspect | Details |
---|---|
How It Works | Uses electromagnetic induction to generate localized heat in conductive materials like copper. |
Why Copper is Ideal | High electrical and thermal conductivity ensures efficient, even heat distribution. |
Applications | Melting, annealing, brazing, soldering, and surface heating of copper and its alloys. |
Advantages | Efficiency, precision, cleanliness, and safety compared to traditional methods. |
Key Considerations | Frequency selection, power requirements, and proper cooling systems. |
Comparison | Faster and more energy-efficient than furnace, flame, or resistance heating. |
Ready to optimize your copper processing with induction heating? Contact our experts today to learn more!