PVD (Physical Vapor Deposition) plating is known for its exceptional durability and resistance to fading, making it a popular choice for applications requiring long-lasting finishes. Unlike traditional plating methods, PVD coatings are highly resistant to wear, corrosion, and oxidation, which helps maintain their appearance over time. With proper care and maintenance, PVD-plated items can retain their elegance and attractiveness for many years. The durability of PVD coatings is influenced by factors such as the substrate material, coating hardness, and environmental conditions, but overall, PVD plating is designed to withstand everyday wear and harsh conditions without significant fading.
Key Points Explained:
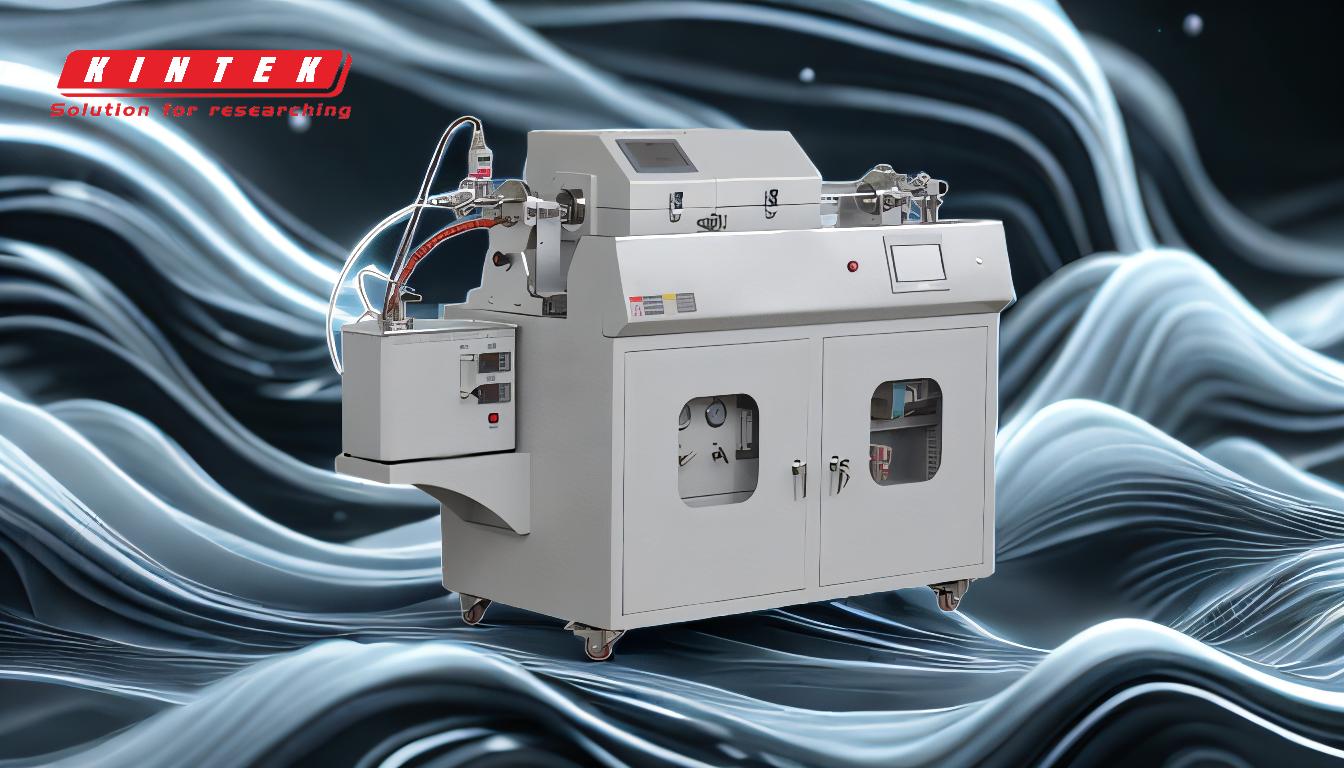
-
Durability of PVD Coatings:
- PVD coatings are highly durable, with robust temperature tolerance, impact strength, and excellent abrasion and corrosion resistance. These properties make PVD coatings suitable for demanding applications where durability is critical.
- PVD-coated jewelry, for example, can last 3 years or more with everyday wear, whereas electroplated jewelry typically lasts only about 1 year.
-
Resistance to Fading:
- PVD coatings are highly resistant to corrosion and oxidation, which are common causes of fading in traditional plating methods.
- The extreme thinness of PVD coatings (ranging from 0.5 microns to five microns) makes them difficult to remove, contributing to their long-lasting appearance.
-
Substrate Material Influence:
- The properties of PVD coatings are influenced by the underlying substrate material. For example, a coating made from TiN (Titanium Nitride) can increase the fatigue limit by 22% and endurance by 7% when applied to Ti-6Al-4V alloy.
- The hardness of the coating is a critical factor in determining its durability and resistance to fading.
-
Superior Quality Compared to Traditional Finishes:
- PVD is considered a super-hard coating, offering superior quality that outlasts any traditional finish. This makes it an ideal choice for applications where maintaining the appearance and functionality of the coated item is essential.
-
Longevity with Proper Care:
- PVD-plated items can maintain their elegance and attractiveness for many years with correct care and maintenance. This includes avoiding harsh chemicals, abrasive materials, and extreme environmental conditions that could potentially damage the coating.
-
Applications and Benefits:
- PVD coatings are widely used in various industries, including jewelry, automotive, aerospace, and medical devices, due to their durability and resistance to fading.
- The ability of PVD coatings to replicate the original finish of materials with minimal effort further enhances their appeal for aesthetic applications.
In summary, PVD plating is designed to be highly resistant to fading, thanks to its exceptional durability, resistance to corrosion and oxidation, and the influence of the substrate material. With proper care and maintenance, PVD-plated items can retain their appearance and functionality for many years, making PVD plating a superior choice for long-lasting finishes.
Summary Table:
Key Aspect | Details |
---|---|
Durability | High temperature tolerance, impact strength, abrasion, and corrosion resistance. |
Fading Resistance | Resistant to corrosion and oxidation, with coatings as thin as 0.5–5 microns. |
Substrate Influence | Coating properties depend on substrate material; TiN enhances fatigue limit. |
Superior Quality | Outlasts traditional finishes, ideal for maintaining appearance and function. |
Longevity with Care | Proper maintenance ensures elegance and attractiveness for years. |
Applications | Jewelry, automotive, aerospace, and medical devices. |
Upgrade to PVD plating for unmatched durability and fade resistance—contact us today to learn more!