PVD (Physical Vapor Deposition) coatings are renowned for their durability, wear resistance, and scratch resistance. Contrary to the misconception that PVD coatings scratch easily, they are highly resistant to scratches, corrosion, and wear due to their super-hard nature and excellent adhesion properties. PVD coatings have a hardness range of 1500–4500 HV (Vickers), making them significantly harder than many traditional materials like carbon steel or nickel/chrome-plated steels. Their low coefficient of friction, uniform application, and ability to withstand high temperatures and impacts further enhance their durability. PVD coatings are widely used in demanding applications where long-lasting performance and minimal maintenance are critical.
Key Points Explained:
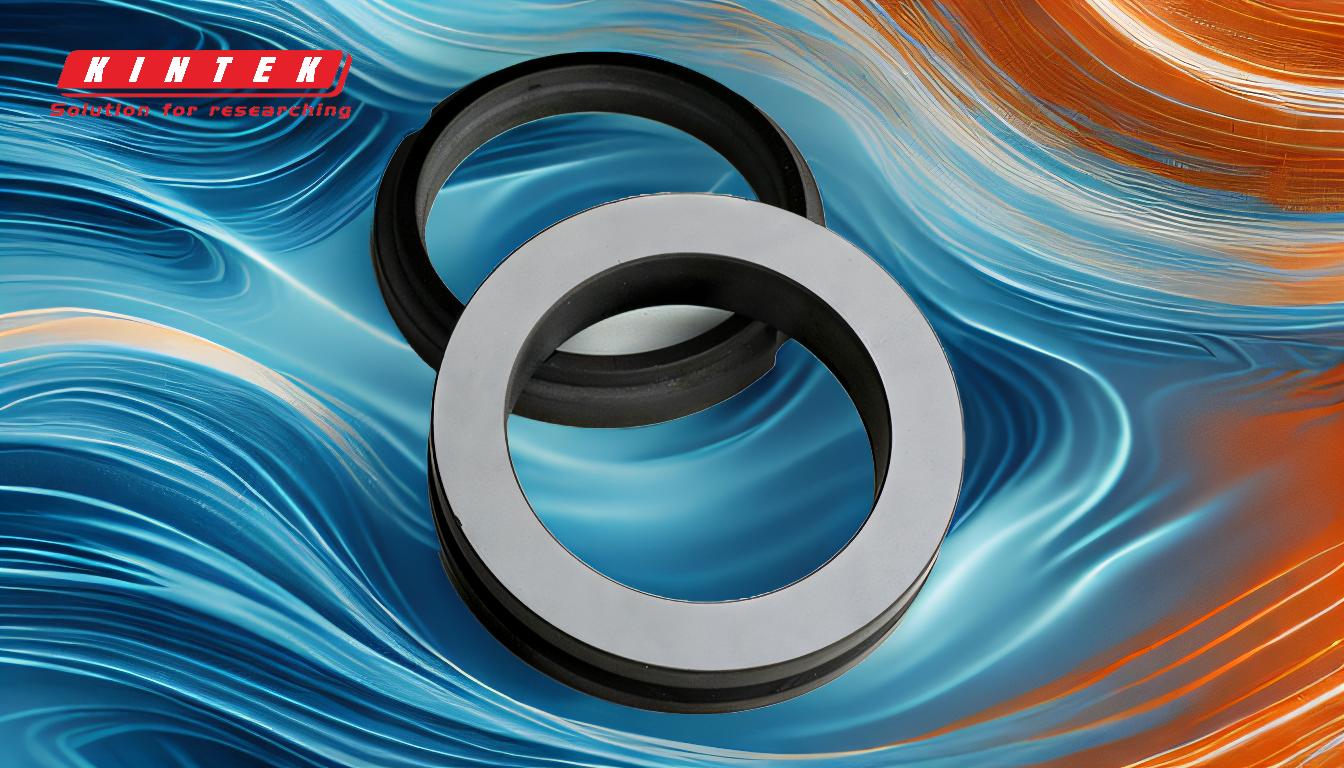
-
Misconception About PVD Scratch Resistance
- The idea that PVD coatings scratch easily is incorrect. PVD coatings are designed to be highly durable and resistant to abrasion, making them suitable for demanding environments.
-
Super-Hard Nature of PVD Coatings
- PVD coatings have a hardness range of 1500–4500 HV (Vickers), which is significantly higher than traditional materials like carbon steel (250 HV) or nickel/chrome-plated steels (600–1000 HV). This extreme hardness contributes to their scratch resistance.
-
Wear and Corrosion Resistance
- PVD coatings are highly resistant to wear, corrosion, and chemical damage. Their uniform application and excellent adhesion ensure they do not chip, tarnish, or fade over time.
-
Comparison with Other Coatings
- PVD coatings are more wear-resistant than CVD (Chemical Vapor Deposition) coatings and can be deposited at lower temperatures. They also exhibit higher compressive stress, which enhances their durability.
-
Low Maintenance and Environmental Benefits
- PVD coatings require minimal maintenance and are environmentally friendly, making them a sustainable choice for long-term applications.
-
Applications in Demanding Environments
- Due to their robustness, PVD coatings are used in industries where durability is critical, such as aerospace, automotive, and medical devices. Their ability to withstand high temperatures and impacts makes them ideal for these applications.
-
Optimum Hardness and Wear Resistance
- While high hardness often correlates with wear resistance, PVD coatings achieve an optimal balance. Excessive hardness can lead to decarburization, but PVD coatings avoid this issue, ensuring consistent performance.
-
Decorative and Functional Benefits
- Beyond their functional advantages, PVD coatings provide a brilliant decorative finish, making them suitable for both industrial and aesthetic applications.
In summary, PVD coatings are highly resistant to scratches and wear, making them one of the most durable and reliable coating options available today. Their superior hardness, corrosion resistance, and low maintenance requirements ensure they outperform traditional finishes in both functional and decorative applications.
Summary Table:
Property | PVD Coatings | Traditional Materials |
---|---|---|
Hardness (HV) | 1500–4500 | 250 (Carbon Steel) |
Scratch Resistance | Extremely High | Moderate |
Wear Resistance | Excellent | Limited |
Corrosion Resistance | High | Moderate |
Maintenance Requirements | Minimal | Frequent |
Applications | Aerospace, Automotive, Medical | General Industrial |
Upgrade your materials with the durability of PVD coatings—contact us today to learn more!