Carbon nanotubes (CNTs) are grown through various methods, each involving the controlled deposition of carbon atoms to form cylindrical nanostructures. The most common techniques include Chemical Vapor Deposition (CVD), Arc Discharge, and Laser Ablation. CVD is the most widely used method due to its scalability and ability to produce high-quality CNTs. The process typically involves the decomposition of a carbon-containing gas on a catalyst substrate at high temperatures, leading to the formation of CNTs. The choice of catalyst, temperature, and gas flow rate significantly influences the growth and properties of the nanotubes. Understanding these methods is crucial for tailoring CNTs for specific applications, such as electronics, composites, and energy storage.
Key Points Explained:
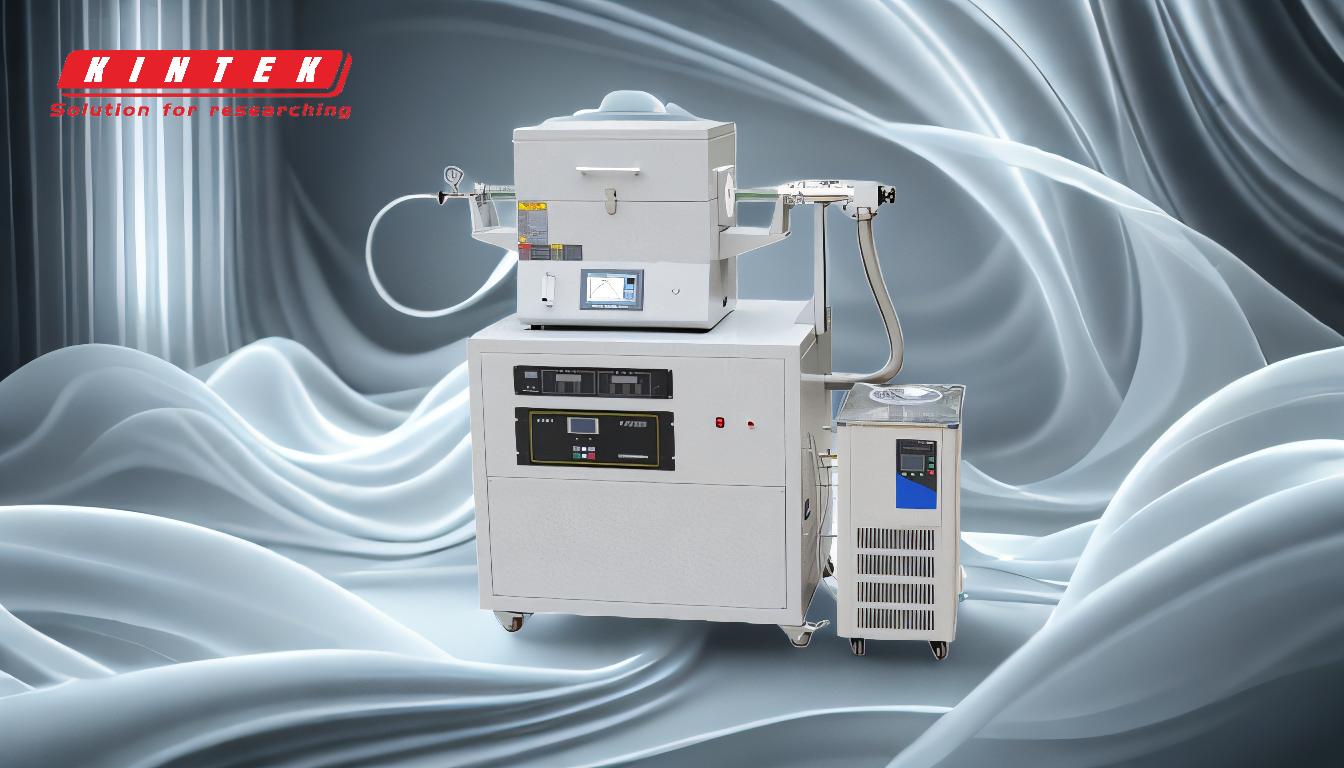
-
Chemical Vapor Deposition (CVD):
- Process Overview: CVD is the most common method for growing carbon nanotubes. It involves the decomposition of a carbon-containing gas (like methane or ethylene) on a catalyst (such as iron, cobalt, or nickel) at high temperatures (typically 600-1000°C). The carbon atoms are deposited on the catalyst particles, forming nanotubes.
- Key Factors: The quality and yield of CNTs depend on the catalyst type, substrate material, temperature, and gas flow rate. For example, a higher temperature generally leads to faster growth but may also increase defects.
- Advantages: CVD is scalable and can produce high-quality, aligned CNTs, making it suitable for industrial applications.
-
Arc Discharge:
- Process Overview: In this method, a high current is passed through two graphite electrodes in an inert gas atmosphere (like helium or argon). The arc vaporizes the carbon from the anode, which then condenses on the cathode, forming CNTs.
- Key Factors: The quality of CNTs depends on the arc current, gas pressure, and electrode material. This method often produces multi-walled carbon nanotubes (MWCNTs) with fewer defects.
- Advantages: Arc discharge can produce high-quality CNTs, but it is less scalable and more energy-intensive compared to CVD.
-
Laser Ablation:
- Process Overview: In laser ablation, a high-power laser is used to vaporize a graphite target in the presence of a catalyst and an inert gas. The vaporized carbon condenses to form CNTs.
- Key Factors: The laser power, target composition, and gas pressure are critical for controlling the growth process. This method can produce single-walled carbon nanotubes (SWCNTs) with high purity.
- Advantages: Laser ablation can produce high-quality SWCNTs, but it is expensive and not easily scalable for large-scale production.
-
Catalyst Role:
- Function: The catalyst plays a crucial role in CNT growth by providing nucleation sites for carbon atoms. Common catalysts include transition metals like iron, cobalt, and nickel.
- Influence on Growth: The size, distribution, and type of catalyst particles affect the diameter, length, and structure of the CNTs. For example, smaller catalyst particles tend to produce smaller-diameter nanotubes.
-
Temperature and Gas Flow:
- Temperature: Higher temperatures generally increase the growth rate of CNTs but may also lead to more defects. Optimal temperatures vary depending on the method and materials used.
- Gas Flow: The flow rate of the carbon-containing gas influences the concentration of carbon atoms available for growth. Proper control of gas flow is essential for consistent CNT production.
-
Applications and Tailoring:
- Electronics: CNTs are used in transistors, sensors, and interconnects due to their excellent electrical properties.
- Composites: CNTs enhance the mechanical properties of materials, making them stronger and lighter.
- Energy Storage: CNTs are used in batteries and supercapacitors for their high surface area and conductivity.
- Tailoring: By controlling growth parameters, CNTs can be tailored for specific applications, such as adjusting their electrical conductivity or mechanical strength.
Understanding these methods and factors is essential for optimizing the growth of carbon nanotubes for various high-tech applications.
Summary Table:
Method | Process Overview | Key Factors | Advantages |
---|---|---|---|
Chemical Vapor Deposition (CVD) | Decomposition of carbon-containing gas on a catalyst at high temperatures. | Catalyst type, temperature, gas flow rate. | Scalable, produces high-quality, aligned CNTs. |
Arc Discharge | High current passed through graphite electrodes in an inert gas atmosphere. | Arc current, gas pressure, electrode material. | Produces high-quality MWCNTs, fewer defects. |
Laser Ablation | High-power laser vaporizes graphite target in the presence of a catalyst and gas. | Laser power, target composition, gas pressure. | Produces high-purity SWCNTs, but expensive and less scalable. |
Catalyst Role | Provides nucleation sites for carbon atoms. Common catalysts: iron, cobalt, nickel. | Size, distribution, and type of catalyst particles. | Influences CNT diameter, length, and structure. |
Temperature and Gas Flow | Higher temperatures increase growth rate but may cause defects. | Optimal temperature and gas flow rate vary by method. | Critical for consistent CNT production. |
Applications | Electronics, composites, energy storage. | Tailoring CNTs for specific applications (e.g., conductivity, mechanical strength). | Enables use in transistors, sensors, batteries, and supercapacitors. |
Ready to explore how carbon nanotubes can revolutionize your industry? Contact us today to learn more!