Improving pellet quality involves optimizing various factors in the pellet production process, including raw material selection, moisture content, particle size, binding agents, and processing conditions. High-quality pellets are characterized by their durability, density, and consistency, which are essential for efficient combustion, storage, and transportation. By focusing on these aspects, you can enhance the physical and chemical properties of your pellets, ensuring they meet industry standards and customer expectations.
Key Points Explained:
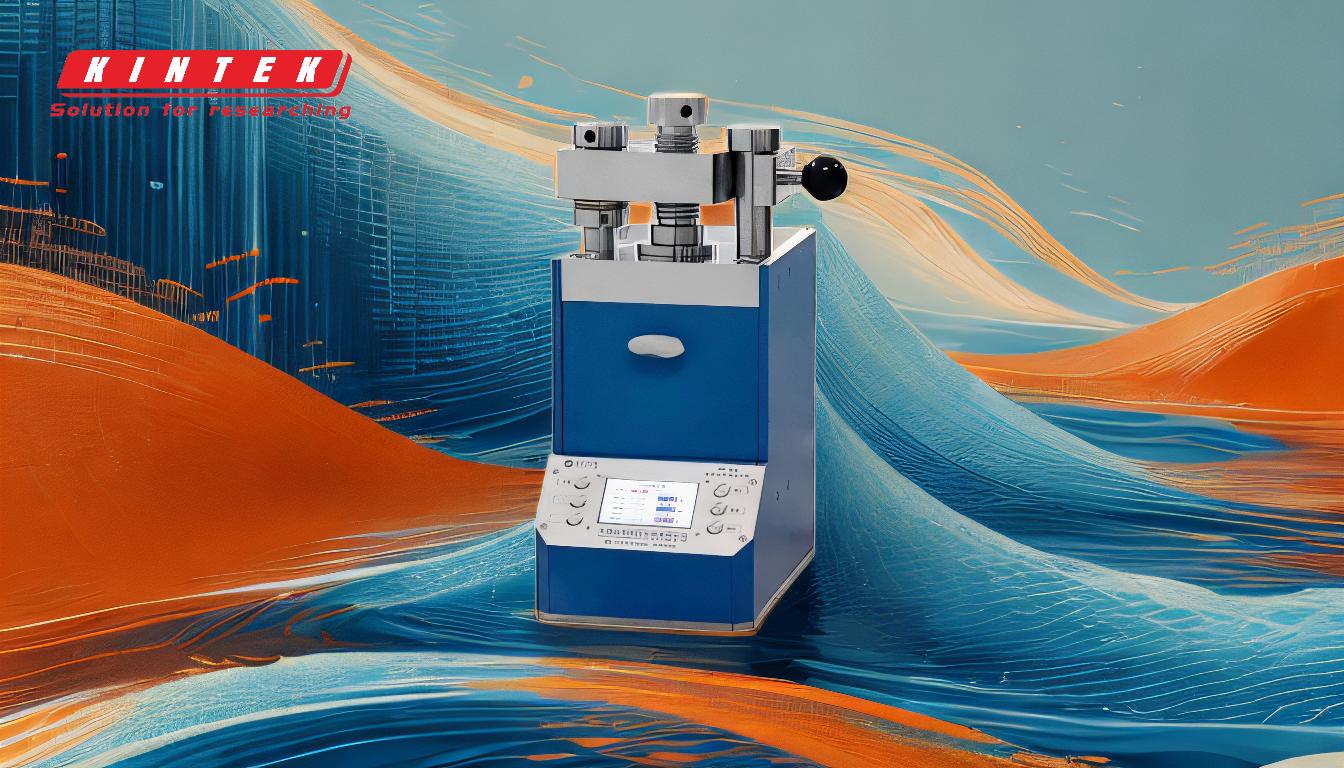
-
Raw Material Selection
- The quality of raw materials directly impacts pellet quality. Use clean, dry, and consistent feedstock with minimal impurities.
- For biomass pellets, use materials like wood, agricultural residues, or energy crops with high lignin content, as lignin acts as a natural binder.
- For feed pellets, ensure the ingredients are nutritionally balanced and free from contaminants.
-
Moisture Content Optimization
- Moisture content is critical for pellet formation. Ideal moisture levels typically range between 10-15% for biomass pellets and 12-18% for feed pellets.
- Too much moisture can lead to soft, low-density pellets, while insufficient moisture can cause cracking and poor binding.
- Use drying equipment to achieve the optimal moisture level before pelleting.
-
Particle Size Reduction
- Grinding raw materials to a uniform particle size improves pellet quality. Smaller particles create a larger surface area, enhancing binding during compression.
- Use a hammer mill or grinder to achieve a consistent particle size, typically between 1-3 mm for most pellet types.
-
Binding Agents and Additives
- Binding agents like lignin, starch, or commercial binders can improve pellet durability and reduce fines.
- For feed pellets, additives such as vitamins, minerals, or growth promoters can enhance nutritional value.
- For biomass pellets, additives like starch or vegetable oil can improve combustion efficiency.
-
Compression and Die Selection
- The compression ratio of the die and the pressure applied during pelleting affect pellet density and durability.
- Choose a die with the appropriate compression ratio for your material type. For example, harder materials may require a higher compression ratio.
- Ensure the die is properly maintained to avoid wear and tear, which can reduce pellet quality.
-
Cooling and Drying
- After pelleting, cool the pellets to room temperature using a pellet cooler. This stabilizes the pellets and reduces moisture content.
- Proper cooling prevents cracking and ensures long-term durability.
-
Quality Control and Testing
- Regularly test pellet quality using parameters such as durability, density, moisture content, and ash content.
- Use a pellet durability tester to measure the percentage of fines produced during handling and transportation.
- Adjust the production process based on test results to maintain consistent quality.
-
Storage and Handling
- Store pellets in a dry, cool environment to prevent moisture absorption and degradation.
- Use appropriate handling equipment to minimize breakage and fines during transportation.
By addressing these factors systematically, you can significantly improve the quality of your pellets, ensuring they meet the desired standards for strength, density, and performance.
Summary Table:
Key Factor | Details |
---|---|
Raw Material Selection | Use clean, dry feedstock with minimal impurities. High lignin content for biomass. |
Moisture Content | Ideal range: 10-15% (biomass) or 12-18% (feed). Use drying equipment. |
Particle Size | Grind to 1-3 mm for uniform binding. Use hammer mills or grinders. |
Binding Agents | Use lignin, starch, or commercial binders to improve durability. |
Compression & Die | Choose the right compression ratio and maintain dies for consistent quality. |
Cooling & Drying | Cool pellets to room temperature to stabilize and reduce moisture. |
Quality Control | Test durability, density, moisture, and ash content regularly. |
Storage & Handling | Store in dry, cool environments and use proper handling equipment. |
Ready to improve your pellet quality? Contact our experts today for tailored solutions!