Vacuum furnaces heat materials in a controlled, oxygen-free environment, ensuring minimal contamination and precise temperature management. They use various heating methods, including resistance heating, induction heating, and radiation heating, with heating elements like graphite, molybdenum, tungsten, and silicon carbide. These elements can withstand extreme temperatures, ranging from 750°C to 2200°C, depending on the material and application. The vacuum environment eliminates oxidation and decarburization, making it ideal for processes like heat treatment, brazing, and sintering. Cooling is often achieved using inert gases, which are pressurized and circulated to absorb heat efficiently. Advanced systems, such as the EV-7, allow for seamless transitions between vacuum and controlled atmospheres, enhancing versatility.
Key Points Explained:
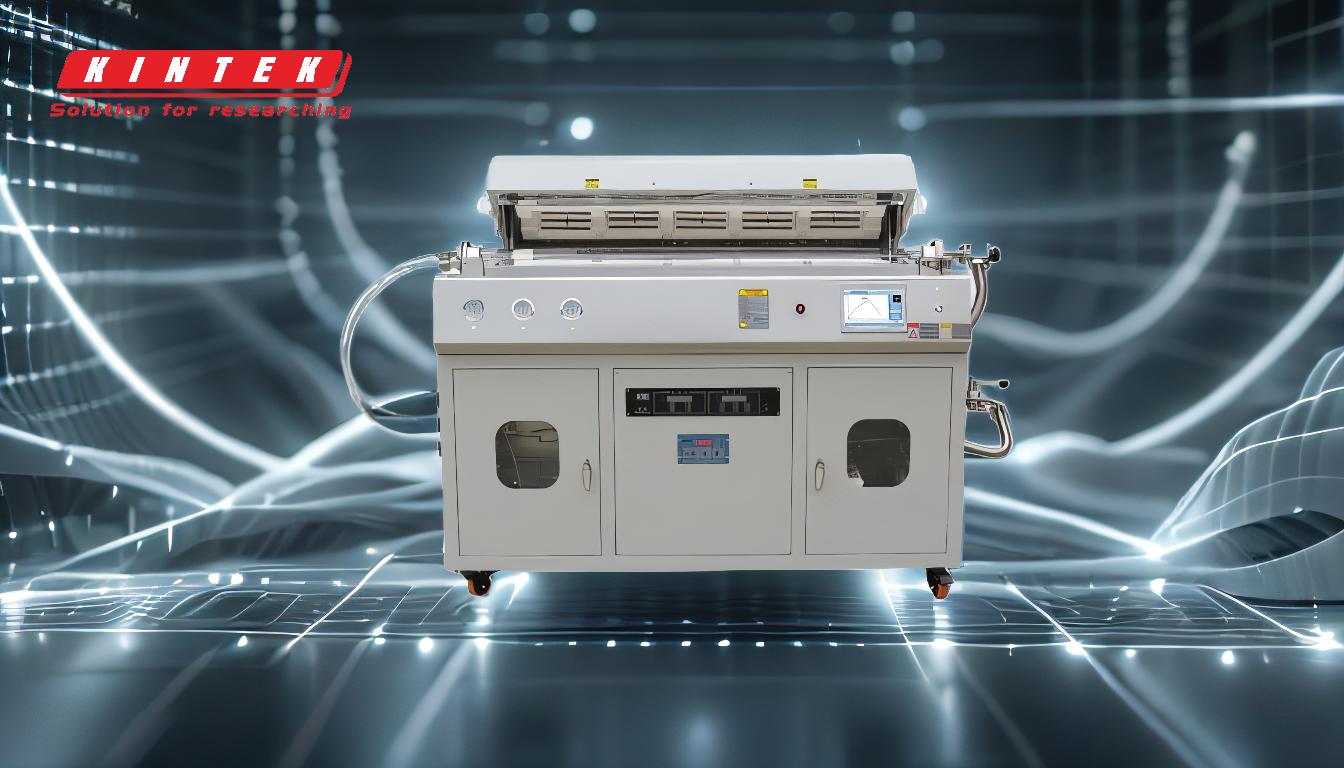
-
Heating Methods in Vacuum Furnaces:
- Resistance Heating: Uses materials like graphite, molybdenum, or tungsten as heating elements. These elements generate heat when an electric current passes through them, making them suitable for high-temperature applications.
- Induction Heating: Heat is generated within the material itself through electromagnetic induction, eliminating the need for external heating elements and reducing contamination risks.
- Radiation Heating: Heat is transferred through thermal radiation, often used in conjunction with resistance heating elements for uniform temperature distribution.
-
Heating Elements and Their Properties:
- Graphite: Can withstand temperatures up to 2200°C and is commonly used in cold-wall vacuum furnaces.
- Molybdenum: Suitable for temperatures up to 1600°C, often used in high-temperature vacuum furnaces.
- Tungsten: Capable of reaching 2200°C, ideal for extreme high-temperature processes.
- Silicon Carbide: Used for moderate temperatures, typically up to 1400°C, and is resistant to thermal shock.
-
Vacuum Environment Benefits:
- Oxidation Prevention: The absence of oxygen and reactive gases prevents oxidation and decarburization, ensuring high-quality results.
- Contamination-Free: The vacuum environment eliminates impurities, making it ideal for sensitive processes like semiconductor manufacturing.
- Precise Temperature Control: The vacuum allows for accurate control of heating and cooling rates, critical for processes like annealing and brazing.
-
Cooling Mechanisms:
- Inert Gas Cooling: After heating, inert gases like argon or nitrogen are circulated to absorb heat. The gases are then removed through a heat exchanger, enabling rapid and controlled cooling.
- Phase Change Cooling: Some systems use water as a heat transfer medium, where water evaporates and condenses to facilitate heat exchange.
-
Advanced Systems (EV-7):
- Dual-Functionality: The EV-7 system allows operation in both vacuum and controlled atmospheres, enhancing flexibility for complex processes.
- Automated Control: Solenoid valves and specialized programs enable precise management of vacuum levels, gas introduction, and aeration.
-
Applications:
- Heat Treatment: Used for processes like annealing, tempering, and hardening, where precise temperature control is essential.
- Brazing and Sintering: Ideal for joining metals or consolidating powders without contamination.
- Semiconductor Manufacturing: Ensures high purity and precision in material processing.
For more details on vacuum furnaces, visit vacuum furnace.
Summary Table:
Aspect | Details |
---|---|
Heating Methods | Resistance, Induction, Radiation |
Heating Elements | Graphite (up to 2200°C), Molybdenum (up to 1600°C), Tungsten (up to 2200°C), Silicon Carbide (up to 1400°C) |
Vacuum Benefits | Prevents oxidation, eliminates contamination, ensures precise temperature control |
Cooling Mechanisms | Inert gas cooling, phase change cooling |
Advanced Systems | EV-7: Dual-functionality (vacuum & controlled atmospheres), automated control |
Applications | Heat treatment, brazing, sintering, semiconductor manufacturing |
Ready to optimize your heating processes with vacuum furnaces? Contact us today to learn more!