Brazing a furnace involves joining metal components using a filler metal with a lower melting point than the base materials. This process requires precise temperature control to ensure the filler metal melts while the base materials remain solid. A brazing furnace provides an oxygen-free environment, which is crucial for achieving strong, uniform bonds. By using a brazing furnace, components like heat exchangers can be joined more compactly and efficiently, leading to improved performance and durability. The process is particularly beneficial for applications requiring high heat-exchanging efficiency and long service life.
Key Points Explained:
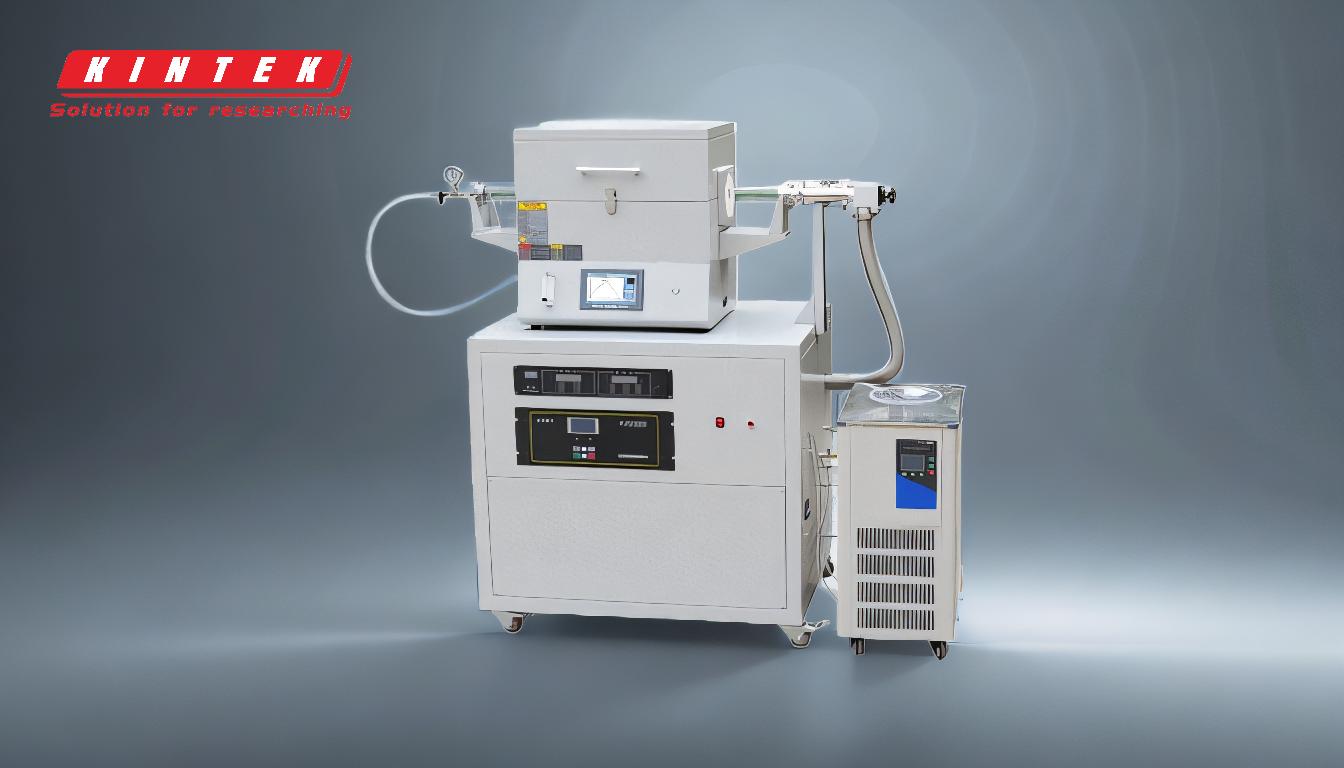
-
Understanding Brazing and Its Purpose:
- Brazing is a metal-joining process where a filler metal is heated above its melting point and distributed between two or more close-fitting parts by capillary action.
- The filler metal has a lower melting point than the base materials, ensuring that only the filler melts during the process.
- This technique is widely used in industries like automotive, aerospace, and HVAC for creating strong, leak-proof joints.
-
Role of a Brazing Furnace:
- A brazing furnace is specifically designed to control temperature precisely, ensuring the filler metal melts while the base materials remain intact.
- It provides an oxygen-free environment, which prevents oxidation and ensures clean, strong joints.
- The furnace is ideal for processing complex components like heat exchangers, where uniformity and compactness are critical.
-
Steps to Braze a Furnace:
-
Preparation:
- Clean the metal surfaces thoroughly to remove any contaminants like oil, grease, or oxides.
- Ensure proper fit-up of the components to allow capillary action to draw the filler metal into the joint.
-
Application of Filler Metal:
- Place the filler metal (often in the form of wire, foil, or paste) at the joint or in proximity to it.
-
Heating in the Brazing Furnace:
- Load the components into the furnace and set the temperature to the filler metal's melting point.
- Maintain the temperature until the filler metal flows and fills the joint completely.
-
Cooling:
- Allow the furnace to cool gradually to room temperature to ensure the filler metal solidifies uniformly and forms a strong bond.
-
Preparation:
-
Advantages of Using a Brazing Furnace:
- Uniform Heating: The furnace ensures even heat distribution, which is crucial for consistent brazing results.
- Oxygen-Free Environment: This prevents oxidation, which can weaken the joint.
- Improved Efficiency: Components like heat exchangers can be joined more compactly, enhancing heat transfer efficiency.
- Longer Service Life: The uniform and strong joints created in a brazing furnace contribute to the durability of the assembled components.
-
Applications of Brazing Furnaces:
- Heat Exchangers: Brazing furnaces are extensively used to join water pipes, cylinders, and heat-absorbing pieces in heat exchangers.
- Automotive and Aerospace: These industries rely on brazing furnaces for creating lightweight, high-strength joints in critical components.
- HVAC Systems: Brazing furnaces are used to assemble components in heating, ventilation, and air conditioning systems, ensuring leak-proof and efficient performance.
By following these steps and understanding the principles of brazing, you can achieve high-quality, durable joints using a brazing furnace. This process is essential for industries where precision, efficiency, and longevity are paramount.
Summary Table:
Key Aspect | Details |
---|---|
Brazing Process | Joins metal components using a filler metal with a lower melting point. |
Role of Brazing Furnace | Provides precise temperature control and an oxygen-free environment. |
Steps to Braze | 1. Preparation 2. Filler Metal Application 3. Heating 4. Cooling |
Advantages | Uniform heating, oxidation prevention, improved efficiency, longer service life. |
Applications | Heat exchangers, automotive, aerospace, HVAC systems. |
Ready to achieve high-quality brazing results? Contact our experts today for tailored solutions!