Ensuring the safe operation of equipment and machinery is a critical aspect of maintaining a productive and hazard-free workplace. It involves a combination of proper training, regular maintenance, adherence to safety protocols, and the use of appropriate safety equipment. By understanding the risks associated with machinery and implementing preventive measures, organizations can significantly reduce the likelihood of accidents and equipment failures. This approach not only protects workers but also enhances the longevity and efficiency of the equipment.
Key Points Explained:
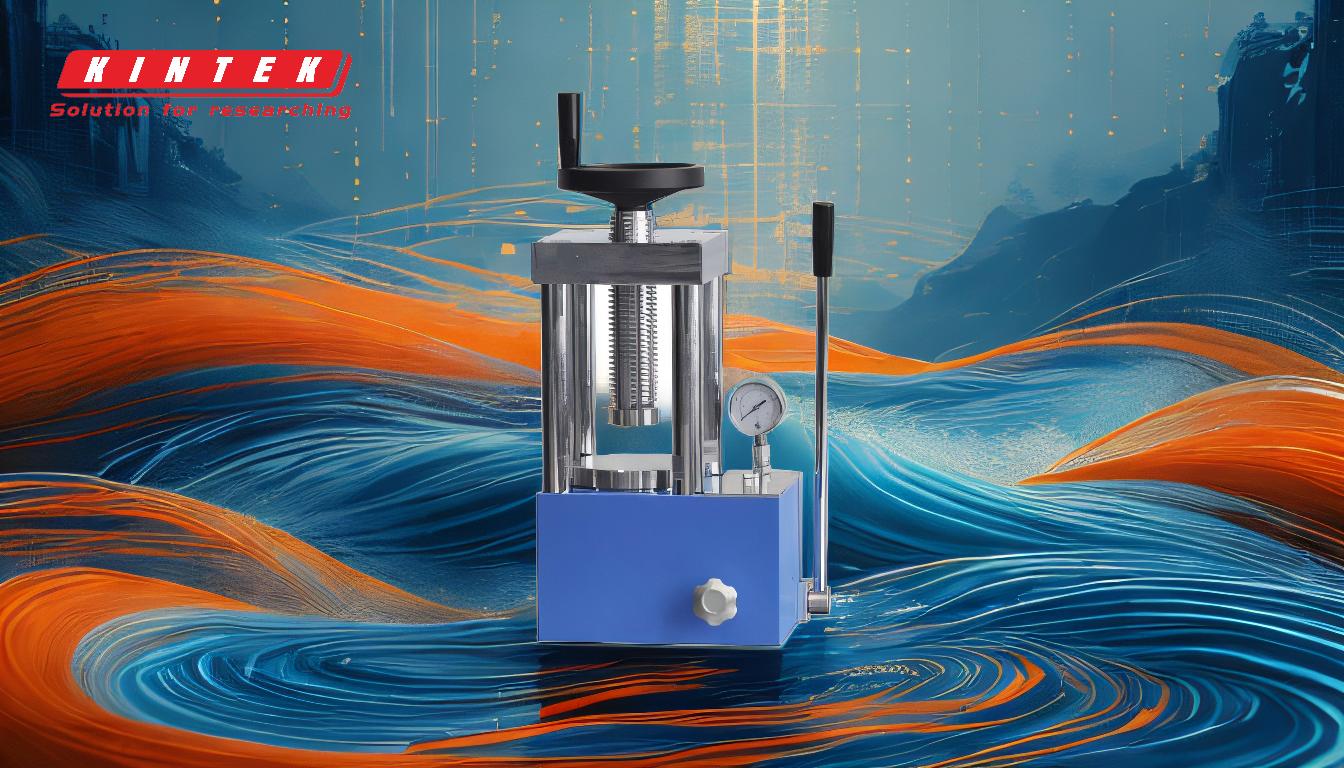
-
Comprehensive Training for Operators
- Why it matters: Operators must be thoroughly trained to understand the machinery they are working with, including its functions, potential hazards, and emergency procedures.
- Implementation: Provide hands-on training sessions, safety manuals, and periodic refresher courses to ensure operators remain up-to-date with best practices.
- Outcome: Well-trained operators are less likely to make errors that could lead to accidents or equipment damage.
-
Regular Maintenance and Inspections
- Why it matters: Machinery that is not properly maintained can malfunction, leading to safety risks and costly downtime.
- Implementation: Establish a routine maintenance schedule, including daily checks, lubrication, and part replacements as needed. Use diagnostic tools to identify potential issues early.
- Outcome: Regular maintenance ensures equipment operates efficiently and reduces the risk of unexpected breakdowns.
-
Adherence to Safety Protocols and Standards
- Why it matters: Safety protocols are designed to minimize risks and ensure compliance with industry regulations.
- Implementation: Develop and enforce safety guidelines, such as lockout/tagout procedures, proper use of personal protective equipment (PPE), and safe operating limits.
- Outcome: Following safety protocols reduces the likelihood of accidents and ensures compliance with legal and regulatory requirements.
-
Use of Safety Equipment and Guards
- Why it matters: Safety equipment, such as guards, emergency stop buttons, and sensors, can prevent injuries by creating physical barriers or stopping machinery in hazardous situations.
- Implementation: Install and maintain safety guards on all moving parts, ensure emergency stop buttons are accessible, and use sensors to detect unsafe conditions.
- Outcome: Proper use of safety equipment significantly reduces the risk of operator injury and equipment damage.
-
Risk Assessment and Hazard Identification
- Why it matters: Identifying potential hazards before they cause harm is essential for creating a safe working environment.
- Implementation: Conduct regular risk assessments to evaluate machinery, work processes, and environmental factors. Address identified risks through engineering controls, administrative changes, or PPE.
- Outcome: Proactive hazard identification and mitigation prevent accidents and improve overall workplace safety.
-
Emergency Preparedness and Response Plans
- Why it matters: Accidents can still occur despite preventive measures, so having a clear response plan is crucial.
- Implementation: Develop and communicate emergency procedures, including evacuation routes, first aid protocols, and contact information for emergency services. Conduct regular drills to ensure readiness.
- Outcome: A well-prepared team can respond effectively to emergencies, minimizing harm and downtime.
-
Monitoring and Continuous Improvement
- Why it matters: Safety is an ongoing process that requires regular evaluation and improvement.
- Implementation: Collect data on incidents, near-misses, and maintenance issues to identify trends and areas for improvement. Encourage feedback from workers to refine safety practices.
- Outcome: Continuous improvement ensures that safety measures evolve to address new challenges and maintain a high standard of safety.
By implementing these key strategies, organizations can create a safe and efficient working environment that protects both workers and equipment. Prioritizing safety not only reduces the risk of accidents but also enhances productivity and fosters a culture of responsibility and care.
Summary Table:
Key Strategy | Why It Matters | Implementation | Outcome |
---|---|---|---|
Comprehensive Training | Reduces operator errors and accidents | Hands-on training, safety manuals, refresher courses | Well-trained operators minimize accidents and equipment damage |
Regular Maintenance | Prevents malfunctions and costly downtime | Routine checks, lubrication, part replacements, diagnostic tools | Efficient operation and reduced risk of breakdowns |
Adherence to Safety Protocols | Ensures compliance and minimizes risks | Lockout/tagout procedures, PPE, safe operating limits | Reduced accidents and regulatory compliance |
Use of Safety Equipment | Prevents injuries and equipment damage | Safety guards, emergency stop buttons, sensors | Lower risk of operator injury and equipment failure |
Risk Assessment | Identifies hazards before they cause harm | Regular risk assessments, engineering controls, PPE | Proactive hazard mitigation improves workplace safety |
Emergency Preparedness | Ensures effective response to accidents | Emergency procedures, drills, first aid protocols | Minimized harm and downtime during emergencies |
Continuous Improvement | Keeps safety measures up-to-date and effective | Data collection, feedback, refining safety practices | Evolving safety measures address new challenges and maintain high standards |
Ready to enhance workplace safety and equipment efficiency? Contact us today to learn more!