Graphene, a single layer of carbon atoms arranged in a hexagonal lattice, can be grown using various methods, broadly categorized into "top-down" and "bottom-up" approaches. The top-down methods involve breaking down graphite into graphene layers, while bottom-up methods build graphene from carbon atoms or molecules. Key techniques include mechanical exfoliation, liquid-phase exfoliation, reduction of graphene oxide, and chemical vapor deposition (CVD). Each method has unique advantages and limitations, with CVD being particularly promising for producing large-area, high-quality graphene. This answer explores these methods in detail, focusing on their processes, applications, and suitability for different needs.
Key Points Explained:
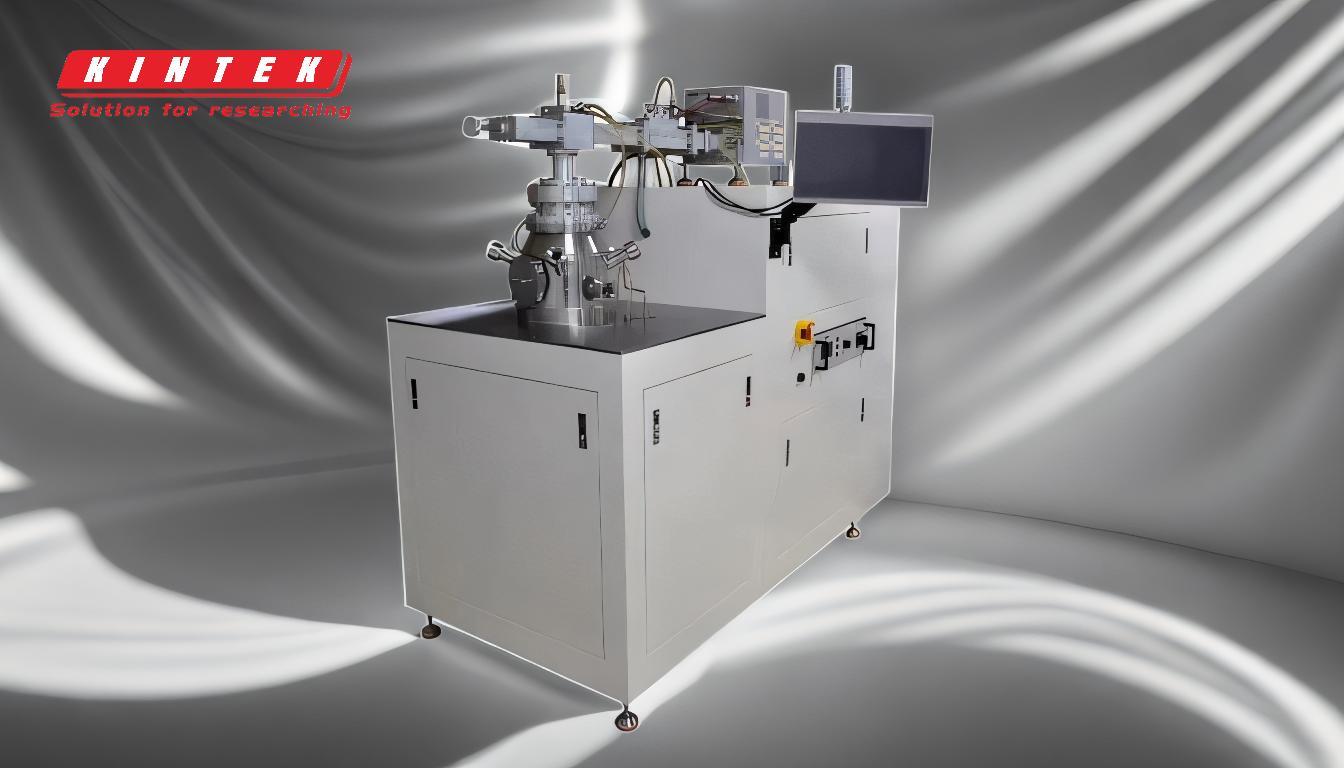
-
Top-Down Methods:
- These methods involve deriving graphene from graphite or other carbon-rich materials. They are generally simpler but may not produce graphene with the highest quality or uniformity.
-
Mechanical Exfoliation:
- Process: Graphite is peeled using adhesive tape to isolate single or few-layer graphene.
- Advantages: Produces high-quality graphene suitable for fundamental research.
- Limitations: Low yield and not scalable for industrial applications.
-
Liquid-Phase Exfoliation:
- Process: Graphite is dispersed in a solvent and exfoliated using ultrasonic energy.
- Advantages: Suitable for mass production and scalable.
- Limitations: Graphene produced often has low electrical quality and may contain defects.
-
Reduction of Graphene Oxide (GO):
- Process: Graphene oxide is chemically reduced to produce graphene.
- Advantages: Cost-effective and scalable.
- Limitations: Reduced graphene often contains residual oxygen and defects, affecting its electrical properties.
-
Bottom-Up Methods:
- These methods build graphene from carbon atoms or molecules, offering better control over quality and structure.
-
Chemical Vapor Deposition (CVD):
- Process: A carbon-containing gas (e.g., methane) is decomposed on a metal substrate (e.g., copper or nickel) at high temperatures, forming graphene layers.
- Advantages: Produces large-area, high-quality graphene with excellent electrical properties. Scalable for industrial applications.
- Limitations: Requires expensive equipment and precise control of process parameters.
-
Epitaxial Growth on Silicon Carbide (SiC):
- Process: Silicon atoms are sublimated from a SiC substrate at high temperatures, leaving behind a graphene layer.
- Advantages: Produces high-quality graphene with good electrical properties.
- Limitations: High cost and limited scalability due to expensive SiC substrates.
-
Arc Discharging:
- Process: An electric arc is used to vaporize carbon electrodes, forming graphene flakes.
- Advantages: Simple and cost-effective.
- Limitations: Produces graphene with variable quality and is not suitable for large-scale production.
-
Comparison of Methods:
-
Quality vs. Scalability:
- Top-down methods (e.g., mechanical exfoliation) are ideal for research but lack scalability.
- Bottom-up methods (e.g., CVD) offer a balance between quality and scalability, making them suitable for industrial applications.
-
Cost Considerations:
- Methods like CVD and epitaxial growth on SiC are expensive but produce high-quality graphene.
- Liquid-phase exfoliation and reduction of graphene oxide are more cost-effective but may compromise on quality.
-
Applications:
- High-quality graphene (e.g., from CVD) is used in electronics, sensors, and advanced materials.
- Lower-quality graphene (e.g., from liquid-phase exfoliation) is suitable for composites, coatings, and energy storage applications.
-
Quality vs. Scalability:
-
Choosing the Right Method:
- For fundamental research: Mechanical exfoliation is preferred due to its ability to produce pristine graphene.
- For industrial applications: CVD is the most promising method due to its scalability and ability to produce high-quality graphene.
- For cost-sensitive applications: Liquid-phase exfoliation or reduction of graphene oxide may be more appropriate.
-
Future Directions:
- Research is ongoing to improve the scalability and cost-effectiveness of bottom-up methods like CVD.
- Efforts are also being made to enhance the quality of graphene produced by top-down methods, such as optimizing liquid-phase exfoliation techniques.
By understanding the strengths and limitations of each method, purchasers and researchers can select the most appropriate technique for their specific needs, whether for high-quality research or scalable industrial production.
Summary Table:
Method | Process Overview | Advantages | Limitations |
---|---|---|---|
Mechanical Exfoliation | Peeling graphite with adhesive tape to isolate graphene layers. | High-quality graphene for research. | Low yield, not scalable for industrial use. |
Liquid-Phase Exfoliation | Dispersing graphite in a solvent and exfoliating with ultrasonic energy. | Scalable for mass production. | Low electrical quality, may contain defects. |
Reduction of Graphene Oxide | Chemically reducing graphene oxide to produce graphene. | Cost-effective and scalable. | Residual oxygen and defects affect electrical properties. |
Chemical Vapor Deposition (CVD) | Decomposing carbon gas on a metal substrate to form graphene layers. | Produces large-area, high-quality graphene; scalable for industrial use. | Expensive equipment, requires precise control. |
Epitaxial Growth on SiC | Sublimating silicon atoms from SiC to leave behind graphene. | High-quality graphene with good electrical properties. | High cost, limited scalability due to expensive SiC substrates. |
Arc Discharging | Vaporizing carbon electrodes with an electric arc to form graphene flakes. | Simple and cost-effective. | Variable quality, not suitable for large-scale production. |
Need help choosing the right graphene growth method? Contact our experts today for tailored advice!