A continuous furnace is designed to process materials or components in a steady, uninterrupted flow, ensuring consistent heating and efficient energy use. Unlike batch furnaces, continuous furnaces operate at a constant temperature, with items moving through the furnace at a controlled speed. This movement is facilitated by mechanisms such as rotating hearths or straight-chamber designs. The furnace typically includes multiple heated zones and may feature a cooling section to reduce cooling times. Continuous furnaces are highly efficient, as they eliminate the need for racks or baskets, reduce thermal mass, and ensure even heating for each item. These characteristics make them ideal for industrial applications requiring high throughput and uniform heat treatment.
Key Points Explained:
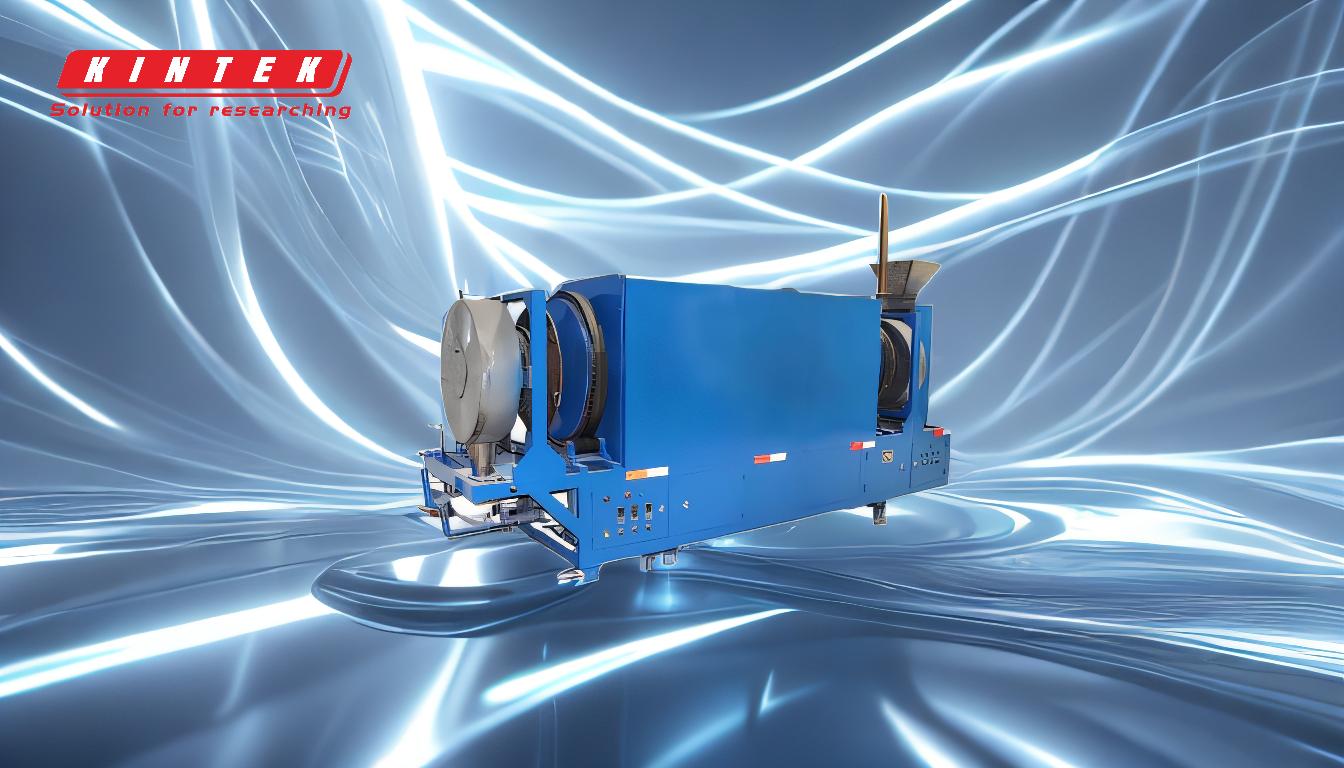
-
Continuous Operation and Movement of Components
- In a continuous furnace, components are loaded at the charging door and move through the furnace to the discharging door. This movement can be achieved using various designs, such as a rotating hearth or a straight-chamber furnace.
- The continuous flow ensures that items are processed without interruption, making it suitable for high-volume production.
-
Heat Transfer Mechanisms
- Continuous furnaces rely on convective heat transfer to heat materials evenly. This can occur through gravity convection, where warmer air naturally displaces cooler air, or mechanical convection, which uses blowers and baffles to distribute heat more quickly and uniformly.
- The design of the furnace ensures that each item is heated individually as it moves through the chamber, maintaining a consistent temperature throughout the process.
-
Energy Efficiency and Reduced Thermal Mass
- Continuous furnaces operate at a constant temperature, which minimizes energy fluctuations and reduces overall energy consumption.
- The absence of racks or baskets in the furnace chamber lowers the thermal mass, allowing for faster heating and cooling cycles. This design also ensures that energy is focused on heating the materials rather than unnecessary components.
-
Heated Zones and Cooling Sections
- Many continuous furnaces are divided into multiple heated zones, each maintained at a specific temperature to achieve precise heat treatment.
- A cooling section is often included at the end of the furnace chamber to reduce cooling times. This feature is particularly beneficial for processes requiring rapid cooling or quenching.
-
Advantages of Continuous Furnaces
- High Efficiency: Continuous furnaces are highly efficient, with energy savings achieved through constant operation and reduced thermal mass.
- Uniform Heating: The steady movement of items through the furnace ensures even heating and consistent results.
- Reduced Oxidation Losses: In applications like metal processing, continuous furnaces can minimize oxidation losses, as seen in tower furnaces where burners at the bottom melt aluminum efficiently.
- Scalability: These furnaces are ideal for industrial applications requiring high throughput and consistent quality.
By combining these features, continuous furnaces provide a reliable and efficient solution for heat treatment processes, making them a preferred choice in industries such as metallurgy, ceramics, and manufacturing.
Summary Table:
Feature | Description |
---|---|
Continuous Operation | Materials move steadily through the furnace, ensuring uninterrupted processing. |
Heat Transfer | Uses convective heat transfer (gravity or mechanical) for even heating. |
Energy Efficiency | Operates at constant temperature, reducing energy fluctuations and thermal mass. |
Heated Zones | Multiple zones maintain precise temperatures for accurate heat treatment. |
Cooling Section | Includes a cooling area to reduce cooling times, ideal for rapid processes. |
Advantages | High efficiency, uniform heating, reduced oxidation losses, and scalability. |
Discover how a continuous furnace can optimize your heat treatment process—contact us today!