A muffle furnace is a specialized laboratory instrument designed to heat materials to extremely high temperatures while isolating them from external contaminants and combustion byproducts. It achieves this through a heat-resistant inner chamber, known as the muffle, which protects the material being heated. The furnace operates using electric heating elements, which radiate or convect heat into the chamber, ensuring uniform temperature distribution. Muffle furnaces are widely used in laboratories for applications such as ashing, sintering, annealing, and material testing, where contamination-free heating is critical. Their design ensures energy efficiency, rapid heating, and precise temperature control, making them indispensable for high-temperature experiments and material processing.
Key Points Explained:
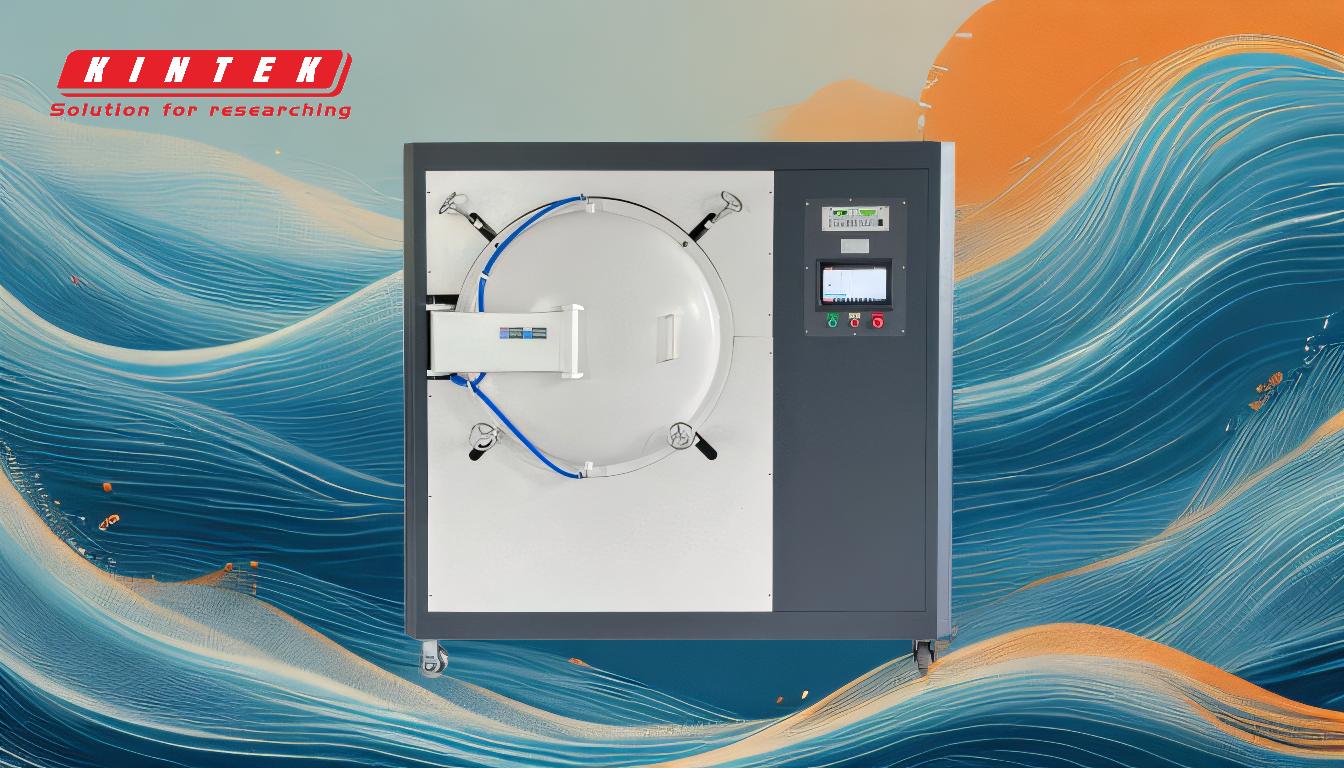
-
Definition and Purpose of a Muffle Furnace
- A muffle furnace is a high-temperature heating device used in laboratories to heat materials while isolating them from external contaminants and combustion byproducts.
- Its primary purpose is to provide a contamination-free environment for processes like ashing, sintering, annealing, and material testing.
-
Key Components and Design
- Muffle (Inner Chamber): The muffle is a heat-resistant container made of materials like ceramic or refractory metals. It isolates the material being heated from the heating elements and external contaminants.
- Heating Elements: Electric coils or other heating elements generate heat, which is transferred to the chamber via radiation or convection.
- Insulation: The furnace is insulated to prevent heat loss, ensuring energy efficiency and maintaining high temperatures.
- Temperature Control System: Modern muffle furnaces include precise temperature control mechanisms, such as thermocouples and digital controllers, to maintain consistent and accurate heating.
-
How It Works
- The material to be heated is placed inside the muffle, which is then sealed to prevent exposure to external contaminants.
- The heating elements generate heat, which is transferred to the chamber, raising the temperature to the desired level.
- The muffle ensures that the material is heated uniformly and without direct contact with combustion byproducts or other contaminants.
-
Applications of a Muffle Furnace
- Ashing: Used to determine the ash content of materials like rubber, polymers, and organic compounds by burning them at high temperatures.
- Sintering: Heating powdered materials to form solid structures without melting them completely.
- Annealing and Tempering: Heat treatment processes used to alter the properties of metals and other materials.
- Material Testing: Used in scientific research to study the behavior of materials at high temperatures without contamination.
-
Advantages of a Muffle Furnace
- Contamination-Free Heating: The muffle isolates the material from combustion byproducts, ensuring clean and accurate results.
- Energy Efficiency: Insulation and advanced heating elements minimize heat loss, reducing energy consumption.
- Precise Temperature Control: Digital controllers and thermocouples allow for accurate and consistent temperature regulation.
- Versatility: Suitable for a wide range of applications, from material testing to industrial processes.
-
Considerations for Purchasing a Muffle Furnace
- Temperature Range: Ensure the furnace can reach the required temperatures for your specific applications.
- Chamber Size: Choose a furnace with an appropriate chamber size to accommodate your samples.
- Heating Rate and Uniformity: Look for models with fast heating rates and uniform temperature distribution.
- Safety Features: Consider furnaces with safety mechanisms like over-temperature protection and automatic shutoff.
- Energy Efficiency: Opt for models with good insulation and energy-saving features to reduce operational costs.
By understanding these key points, you can better appreciate how a muffle furnace works and its importance in laboratory and industrial settings. Whether you're conducting high-temperature experiments or processing materials, a muffle furnace provides a reliable and contamination-free solution.
Summary Table:
Aspect | Details |
---|---|
Purpose | Provides contamination-free heating for processes like ashing and sintering. |
Key Components | Muffle (inner chamber), heating elements, insulation, temperature control. |
Applications | Ashing, sintering, annealing, material testing. |
Advantages | Contamination-free, energy-efficient, precise temperature control. |
Purchase Considerations | Temperature range, chamber size, heating rate, safety features. |
Need a reliable muffle furnace for your lab? Contact us today to find the perfect solution!