A press machine is a versatile piece of equipment used to shape, cut, or mold materials by applying mechanical or hydraulic force. It is widely used in industries such as manufacturing, metalworking, and construction. The working principle of a press machine involves the application of pressure to a workpiece, which is placed between two dies or molds. This pressure can be generated mechanically, hydraulically, or pneumatically, depending on the type of press. Mechanical presses use a motor-driven flywheel to store and transfer energy, while hydraulic presses rely on fluid pressure to generate force. The process typically involves positioning the material, applying force to deform or shape it, and then releasing the pressure to remove the finished product. Press machines are essential for tasks like stamping, forging, and bending, offering precision and efficiency in material processing.
Key Points Explained:
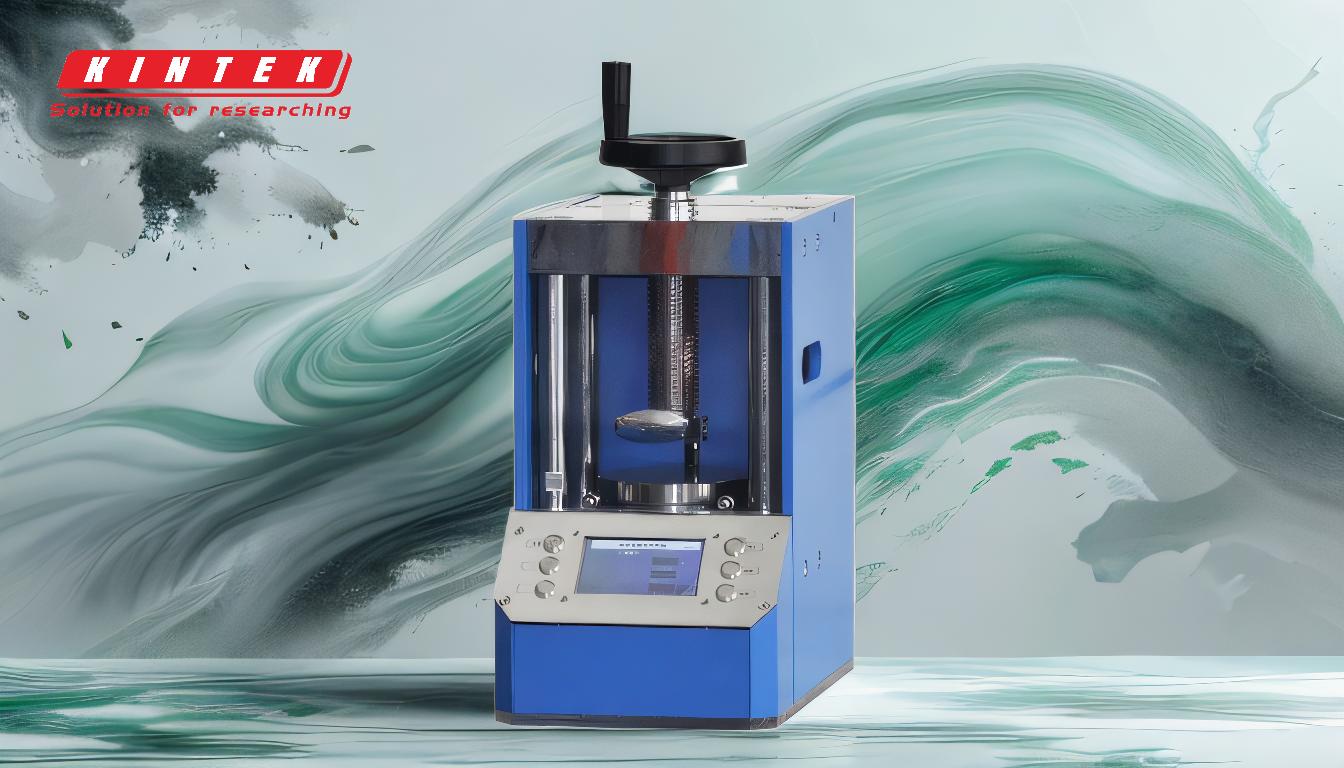
-
Types of Press Machines:
- Mechanical Press: Uses a motor-driven flywheel to store energy, which is then transferred to the ram (the moving part) to apply force. Mechanical presses are known for their speed and are commonly used for high-volume production.
- Hydraulic Press: Relies on hydraulic fluid to generate pressure, which is then applied to the ram. Hydraulic presses offer greater control over force and speed, making them ideal for tasks requiring precision, such as deep drawing or molding.
- Pneumatic Press: Uses compressed air to generate force. These are typically smaller and used for lighter tasks.
- Hot Press Machine: A specialized type of press that applies heat along with pressure, often used in industries like woodworking or composite manufacturing. The heat softens the material, making it easier to shape or bond. For more details, visit hot press machine.
-
Working Mechanism:
- Force Application: The press machine applies force to the workpiece through a ram or platen. The force can be adjusted based on the material and the desired outcome.
- Die and Mold Interaction: The workpiece is placed between two dies or molds. The upper die moves downward to shape or cut the material, while the lower die remains stationary.
- Cycle Operation: The press operates in a cycle—starting with the ram in the raised position, moving down to apply force, and then returning to the starting position to release the finished product.
-
Applications of Press Machines:
- Stamping: Used to cut or shape metal sheets into specific forms, such as automotive parts or household appliances.
- Forging: Involves shaping metal by applying compressive force, often used to create strong, durable components like gears or crankshafts.
- Bending: Used to bend metal sheets or bars into desired angles or shapes.
- Molding: In industries like plastics or composites, press machines are used to mold materials into specific shapes under heat and pressure.
-
Advantages of Press Machines:
- Precision: Offers high accuracy in shaping and cutting materials.
- Efficiency: Capable of handling large volumes of work in a short time.
- Versatility: Can be used for a wide range of materials and applications.
- Automation: Many press machines can be automated, reducing labor costs and increasing productivity.
-
Key Components:
- Ram/Platen: The moving part that applies force to the workpiece.
- Die/Mold: The tooling used to shape or cut the material.
- Frame: Provides structural support and ensures stability during operation.
- Control System: Allows operators to adjust parameters like force, speed, and cycle time.
-
Safety Considerations:
- Guarding: Press machines should be equipped with safety guards to protect operators from moving parts.
- Emergency Stop: A readily accessible emergency stop button is essential for halting operations in case of an issue.
- Training: Operators must be trained to understand the machine's operation and safety protocols.
By understanding these key points, equipment and consumable purchasers can make informed decisions when selecting a press machine for their specific needs, ensuring optimal performance and safety in their operations.
Summary Table:
Aspect | Details |
---|---|
Types | Mechanical, Hydraulic, Pneumatic, Hot Press |
Working Mechanism | Force application via ram, die/mold interaction, and cycle operation |
Applications | Stamping, forging, bending, molding |
Advantages | Precision, efficiency, versatility, automation |
Key Components | Ram/platen, die/mold, frame, control system |
Safety Considerations | Guarding, emergency stop, operator training |
Discover the perfect press machine for your needs—contact our experts today!