A rotary kiln rotates to facilitate the movement and processing of materials within its cylindrical structure. The rotation is achieved through a combination of mechanical and structural design elements, ensuring that materials are evenly heated, mixed, and transported from the upper end to the lower end of the kiln. The kiln is slightly inclined from the horizontal, allowing gravity to assist in the movement of materials. The rotation is powered by a drive system, which typically includes motors, gears, and support rollers. The kiln's rotation ensures that materials are tumbled and exposed uniformly to heat, preventing localized overheating and ensuring consistent processing.
Key Points Explained:
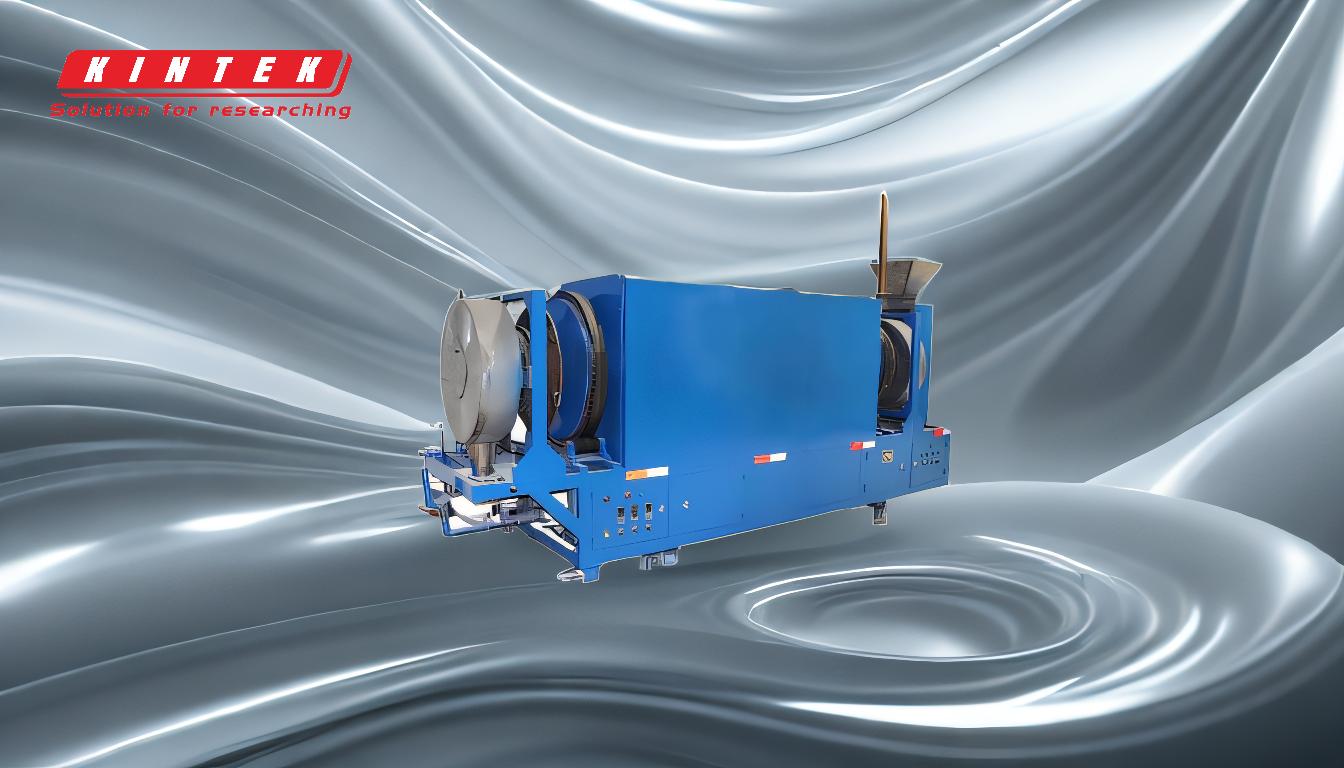
-
Structural Design and Inclination:
- The rotary kiln is a cylindrical vessel that is slightly inclined from the horizontal. This inclination is crucial as it allows gravity to assist in moving the material from the upper end (where it is fed) to the lower end (where it exits).
- The inclination angle is carefully calculated to ensure optimal movement of the material without causing it to move too quickly or too slowly through the kiln.
-
Rotation Mechanism:
- The kiln rotates slowly about its longitudinal axis. This rotation is powered by a drive system, which typically includes a motor, gears, and support rollers.
- The rotation speed is controlled to ensure that the material is tumbled and mixed effectively, promoting even exposure to heat and preventing the material from clumping or sticking to the kiln walls.
-
Material Movement and Mixing:
- As the kiln rotates, the material inside is lifted by the rotation and then tumbles back down due to gravity. This tumbling action ensures that the material is continuously mixed and exposed to the heat evenly.
- The tumbling also prevents the material from remaining in one spot for too long, which could lead to uneven heating or damage to the kiln's internal surfaces.
-
Heat Application:
- The kiln can be heated either internally (direct heating) or externally (indirect heating). Internal heating is often achieved through a flame projected from a burner-pipe, which can use various fuels such as gas, oil, or pulverized coal.
- Hot gases flow through the kiln, either in the same direction as the material (co-current) or in the opposite direction (counter-current). This flow of hot gases is essential for maintaining the desired temperature profile within the kiln.
-
Temperature and Retention Time Control:
- The temperature inside the kiln and the retention time (the duration the material spends in the kiln) are carefully controlled based on chemical and thermal analyses. This ensures that the material undergoes the necessary chemical reactions or physical changes.
- The rotation speed and inclination angle are adjusted to achieve the desired retention time, ensuring that the material is processed effectively.
-
Sealing and Atmosphere Control:
- The kiln is sealed at both ends to control the internal atmosphere and temperature. This sealing is crucial for maintaining the desired conditions for the chemical reactions or physical changes to occur.
- The sealing also prevents the escape of heat and gases, improving the efficiency of the kiln and ensuring that the process is managed effectively.
-
Applications and Benefits:
- Rotary kilns are used in various industries, including cement production, waste processing, and chemical manufacturing. The rotation ensures that materials are processed uniformly, leading to consistent product quality.
- The ability to control temperature, retention time, and atmosphere makes rotary kilns versatile and effective for a wide range of applications.
In summary, the rotation of a rotary kiln is a carefully controlled process that involves a combination of structural design, mechanical systems, and precise control of temperature and material flow. This ensures that materials are processed efficiently and uniformly, making rotary kilns an essential tool in many industrial processes.
Summary Table:
Key Aspect | Details |
---|---|
Structural Design | Cylindrical vessel inclined to use gravity for material movement. |
Rotation Mechanism | Powered by a drive system (motor, gears, rollers) for controlled rotation. |
Material Movement | Tumbling action ensures even mixing and heat exposure. |
Heat Application | Internal/external heating with hot gas flow (co-current or counter-current). |
Temperature Control | Precise control of temperature and retention time for optimal processing. |
Atmosphere Control | Sealed ends to maintain internal conditions and improve efficiency. |
Applications | Used in cement, waste processing, and chemical industries. |
Learn how a rotary kiln can optimize your industrial processes—contact our experts today!