An induction heating furnace operates by utilizing electromagnetic induction to generate heat within conductive materials. The process involves passing an alternating current through a copper coil, creating a powerful electromagnetic field. When a conductive material is placed within this field, eddy currents are induced within the material, generating heat internally. This method ensures efficient and uniform heating without direct contact between the coil and the material. The heat is produced through Joule heating, where the resistance of the material converts the induced currents into thermal energy. Additionally, in ferromagnetic materials, magnetic hysteresis contributes to further heating. This technology is widely used in applications such as melting, forging, and heat treatment due to its precision and energy efficiency.
Key Points Explained:
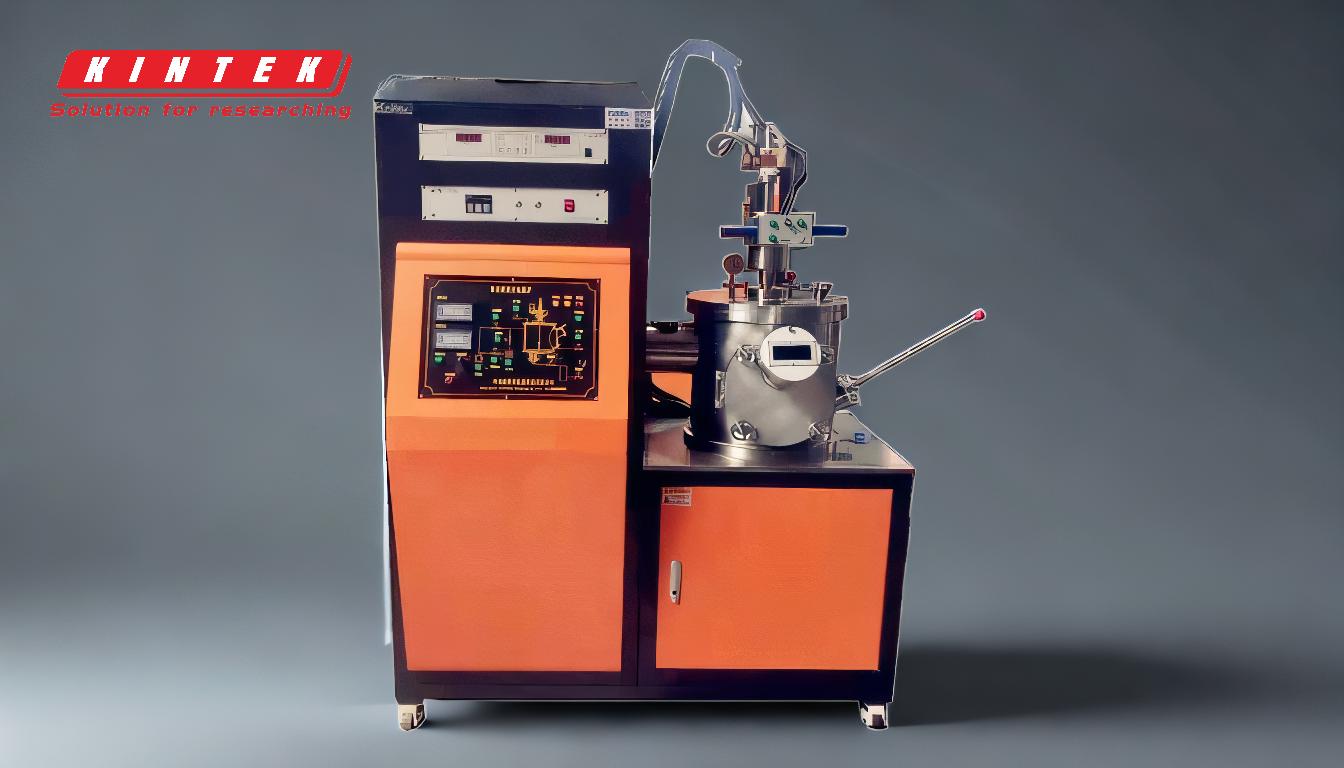
-
Electromagnetic Induction:
- The core principle behind induction heating is electromagnetic induction. When an alternating current flows through a copper coil, it generates a rapidly reversing magnetic field.
- This magnetic field penetrates the conductive material placed within the coil, inducing eddy currents inside the material.
-
Eddy Currents and Joule Heating:
- The induced eddy currents flow against the electrical resistance of the material, generating heat through Joule heating.
- Joule heating is the process by which the energy of the electric current is converted into thermal energy due to the resistance of the material.
-
Magnetic Hysteresis in Ferromagnetic Materials:
- In ferromagnetic materials like iron, additional heating occurs due to magnetic hysteresis. This is the energy loss that occurs when the magnetic domains within the material realign with the changing magnetic field.
- This phenomenon contributes to the overall heating efficiency in materials that exhibit magnetic properties.
-
Non-Contact Heating:
- Induction heating is a non-contact process, meaning the heating coil does not physically touch the material being heated.
- This eliminates contamination and reduces wear and tear on the heating equipment, making it ideal for precision applications.
-
Efficiency and Uniform Heating:
- The heat is generated internally within the material, leading to efficient and uniform heating.
- This internal generation of heat minimizes heat loss to the surrounding environment, making induction heating more energy-efficient compared to traditional heating methods.
-
Medium Frequency Induction Heating:
- In some applications, the power frequency alternating current (50Hz) is converted to a medium frequency (300Hz to 1000Hz) using a power supply device.
- This medium frequency current flows through a capacitor and an induction coil, generating high-density magnetic lines that enhance the induction heating effect.
-
Applications of Induction Heating:
- Induction heating is widely used in various industrial processes, including metal melting, forging, brazing, and heat treatment.
- Its ability to provide precise and controlled heating makes it suitable for applications requiring high-quality thermal processing.
-
Components of an Induction Heating Furnace:
- Induction Coil: The primary component that generates the electromagnetic field.
- Power Supply: Converts standard electrical power into the required frequency and current for induction heating.
- Crucible: A non-conductive container that holds the metal charge, ensuring that the heat is concentrated within the material.
By understanding these key points, one can appreciate the sophisticated yet efficient nature of induction heating technology, which leverages fundamental physical principles to achieve precise and controlled heating in various industrial applications.
Summary Table:
Key Aspect | Description |
---|---|
Electromagnetic Induction | Alternating current in a coil creates a magnetic field, inducing eddy currents. |
Eddy Currents & Joule Heating | Heat is generated internally as eddy currents flow against material resistance. |
Magnetic Hysteresis | Additional heating in ferromagnetic materials due to magnetic domain realignment. |
Non-Contact Heating | No physical contact between coil and material, reducing contamination and wear. |
Efficiency & Uniform Heating | Heat is generated internally, ensuring energy efficiency and uniform heating. |
Medium Frequency Heating | Enhanced heating effect using medium frequency currents (300Hz–1000Hz). |
Applications | Used in melting, forging, brazing, and heat treatment for precision results. |
Key Components | Induction coil, power supply, and crucible for effective heat generation. |
Ready to harness the power of induction heating for your industrial needs? Contact us today to learn more!