An industrial furnace operates by generating and controlling heat to process materials, often at high temperatures. It consists of key components such as a heating chamber, heating elements (electric or fuel-based), temperature control systems, and sometimes atmosphere or gas control systems for specialized applications. The furnace heats materials uniformly, monitored and regulated by thermocouples and controllers, ensuring precise temperature management. Depending on the type (e.g., muffle, resistance, or crucible furnaces), it may include insulation, safety mechanisms, and exhaust systems. Industrial furnaces are used for processes like tempering, annealing, and firing, tailored to specific material requirements and operating conditions.
Key Points Explained:
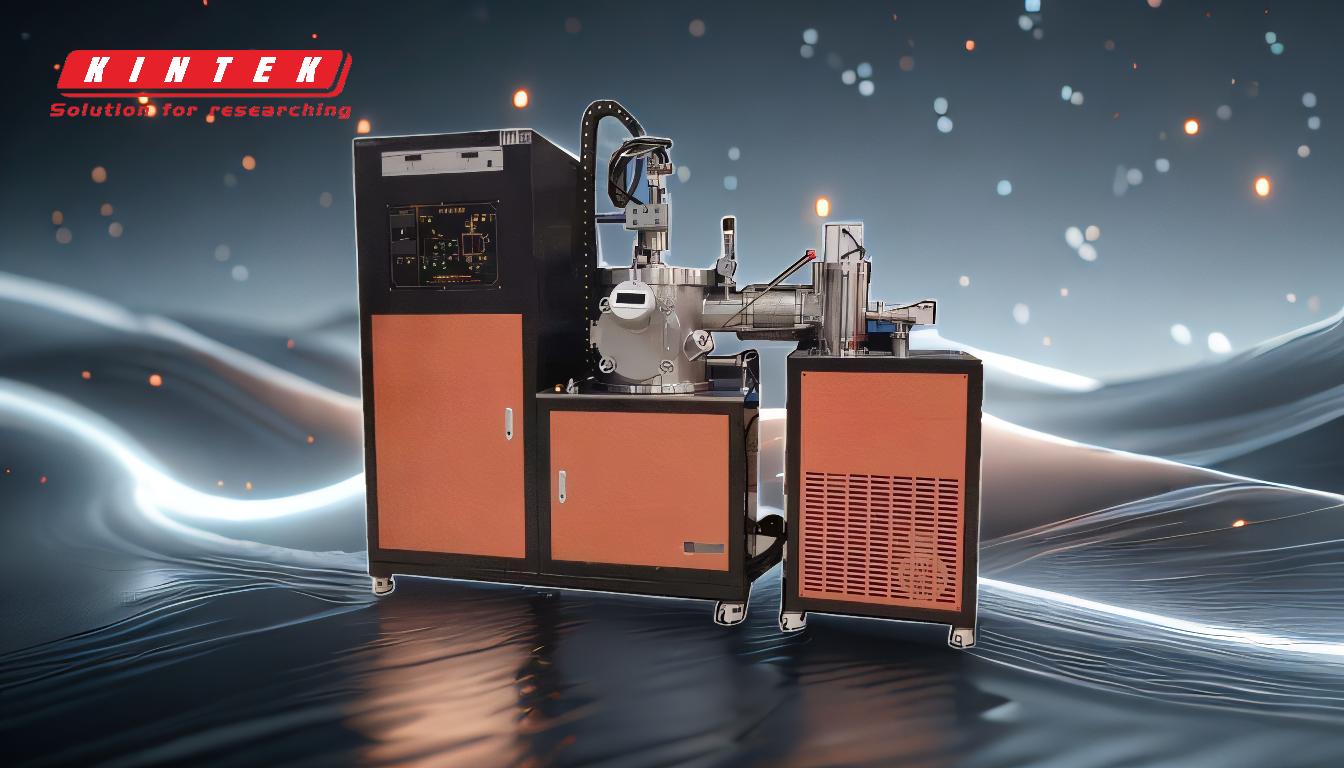
-
Heating Chamber and Insulation
- The heating chamber is the core of the furnace, constructed from high-temperature-resistant materials like ceramics or refractory metals to withstand extreme heat.
- Insulation materials surround the chamber to minimize heat loss, improve energy efficiency, and maintain uniform temperatures.
- For example, muffle furnaces use an insulated chamber (the muffle) to isolate samples from direct contact with heating elements.
-
Heating Elements
- Heating elements generate heat through electric resistance (in resistance furnaces) or combustion (in gas- or oil-fired furnaces).
- Electric furnaces use resistance wires or ceramic heating elements, converting electrical energy into heat via the Joule effect.
- Gas- or oil-fired furnaces rely on burners and blowers to combust fuel, producing heat for processes like melting or tempering.
-
Temperature Control Systems
- Temperature control is critical for precise material processing.
- Thermocouples measure the temperature inside the furnace and send signals to a control panel, which adjusts the heat output.
- Advanced controllers allow users to set specific temperature profiles, timers, and safety limits.
- For instance, tempering furnaces operate within a narrow temperature range (300°C to 750°C) to achieve desired material properties.
-
Atmosphere and Gas Control
- Some furnaces, like atmosphere furnaces, require controlled gas environments to prevent oxidation or achieve specific chemical reactions.
- A gas supply system introduces gases like nitrogen or hydrogen, while an atmosphere control system maintains the desired gas composition.
- This is essential for processes like annealing or sintering, where material properties depend on the surrounding atmosphere.
-
Safety and Exhaust Systems
- Safety mechanisms, such as automatic shutoff switches, protect against overheating or equipment failure.
- Exhaust systems vent flue gases or fumes generated during combustion or material processing, ensuring a safe working environment.
- For example, crucible furnaces include tilt mechanisms and exhaust channels to safely handle molten materials and vent combustion byproducts.
-
Specialized Furnace Types
- Muffle Furnace: Uses an insulated chamber to isolate samples, ideal for high-temperature applications like ashing or heat treatment.
- Resistance Furnace: Relies on electric heating elements, suitable for precise temperature control in laboratories or industrial settings.
- Crucible Furnace: Designed for melting metals, featuring a tiltable design and combustion-based heating.
- Tempering Furnace: Operates at moderate temperatures to improve material toughness and durability.
By integrating these components and systems, industrial furnaces provide reliable and efficient heat processing for a wide range of applications, from metalworking to ceramics and beyond.
Summary Table:
Component | Function |
---|---|
Heating Chamber | Core area for material processing, made of high-temperature-resistant materials. |
Heating Elements | Generate heat via electric resistance or combustion for processes like melting or tempering. |
Temperature Control | Ensures precise heat regulation using thermocouples and advanced controllers. |
Atmosphere Control | Maintains specific gas environments for processes like annealing or sintering. |
Safety & Exhaust Systems | Protects against overheating and vents harmful gases, ensuring a safe working environment. |
Specialized Furnace Types | Includes muffle, resistance, crucible, and tempering furnaces for diverse applications. |
Discover the right industrial furnace for your needs—contact our experts today!