Carburizing is a heat treatment process used to increase the surface hardness of low-carbon steel alloys by diffusing carbon atoms into the surface and sub-surface layers. This process enhances wear resistance, fatigue strength, and overall mechanical properties while maintaining a soft, ductile core. The steel is heated to high temperatures in a carbon-rich environment, allowing carbon to diffuse into the surface. After carburizing, the material is quenched, typically in oil, to harden the surface. Case depths typically range from 0.020″ to 0.050″, making it ideal for producing durable mechanical components, tools, and fasteners.
Key Points Explained:
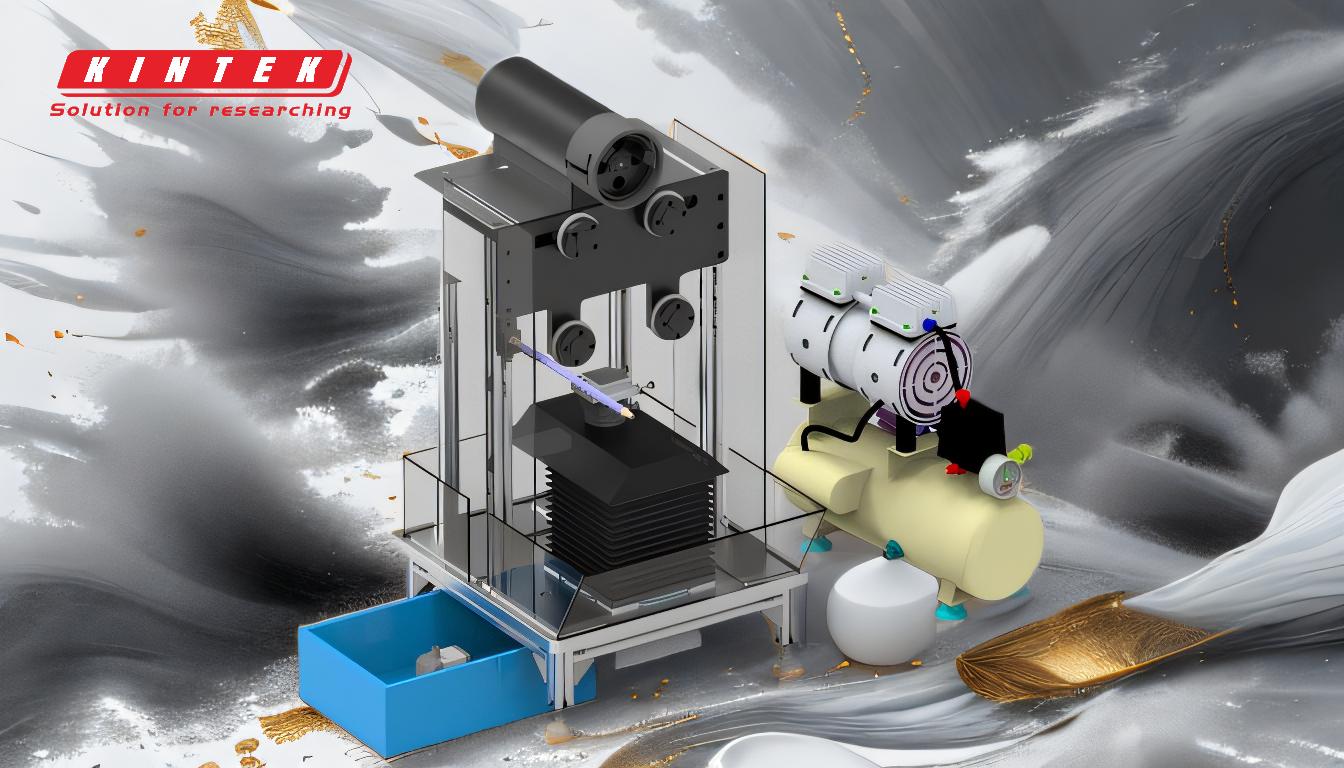
-
Purpose of Carburizing:
- Carburizing is primarily used to increase the surface hardness of low-carbon steel alloys.
- It improves wear resistance, fatigue strength, and mechanical properties while retaining a ductile core.
- This makes it suitable for components that require a hard surface for durability and a tough core to withstand mechanical stress.
-
Process Overview:
- The steel is heated to high temperatures (typically between 850°C and 950°C) in a carbon-rich environment.
- Carbon atoms diffuse into the surface and sub-surface layers of the steel.
- After carburizing, the material is quenched, usually in oil, to harden the surface.
- The result is a hard, wear-resistant surface layer with a softer, ductile core.
-
Types of Carburizing:
- Gas Carburizing: Involves heating the steel in a furnace with a carbon-rich gas (e.g., methane or propane). The gas decomposes at high temperatures, releasing carbon that diffuses into the steel.
- Vacuum Carburizing: The steel is placed in a vacuum furnace, heated, and then exposed to a carbon-rich gas (e.g., propane). The vacuum environment ensures precise control over the carbon diffusion process.
- Liquid Carburizing: The steel is immersed in a molten salt bath containing carbon-rich compounds. This method is less common but offers uniform heating and carbon diffusion.
- Pack Carburizing: The steel is packed in a carbon-rich material (e.g., charcoal) and heated in a sealed container. Carbon from the packing material diffuses into the steel.
-
Carbon Diffusion Mechanism:
- At high temperatures, carbon atoms migrate from the carbon-rich environment into the steel's surface.
- The diffusion process is driven by the concentration gradient, with carbon atoms moving from areas of high concentration (the environment) to low concentration (the steel surface).
- The depth of carbon penetration (case depth) depends on the temperature, time, and carbon potential of the environment.
-
Quenching and Hardening:
- After carburizing, the steel is rapidly cooled (quenched) to lock the carbon atoms in place and harden the surface.
- Quenching transforms the austenite (a high-temperature phase of steel) into martensite, a hard, brittle structure.
- The soft core remains ductile because it does not undergo the same phase transformation.
-
Applications of Carburizing:
- Carburizing is widely used in industries requiring durable, wear-resistant components.
- Common applications include gears, shafts, bearings, fasteners, and tools.
- It is particularly useful for parts subjected to high stress, abrasion, or cyclic loading.
-
Advantages of Carburizing:
- Enhances surface hardness and wear resistance without compromising the core's toughness.
- Improves fatigue strength, making it suitable for high-stress applications.
- Can be applied selectively to specific areas using masking techniques (e.g., carbon stopping paint).
- Compatible with a wide range of low-carbon steels and alloy steels.
-
Limitations of Carburizing:
- Requires precise control of temperature, time, and carbon potential to achieve desired case depth and hardness.
- The process can be energy-intensive and time-consuming, especially for deep case depths.
- May cause distortion or cracking in complex geometries due to uneven heating or quenching.
-
Comparison with Other Processes:
- Carbonitriding: Similar to carburizing but involves diffusing both carbon and nitrogen into the steel. This process is used for parts requiring through-hardening.
- Induction Hardening: A localized hardening process that uses electromagnetic induction to heat specific areas of the steel. It is faster but does not provide the same depth of hardening as carburizing.
-
Future Trends:
- Advances in vacuum carburizing technology are improving process control and reducing energy consumption.
- The development of eco-friendly carburizing gases and quenching media is gaining attention to reduce environmental impact.
- Automation and digital monitoring systems are being integrated to enhance precision and repeatability.
By understanding these key points, equipment and consumable purchasers can make informed decisions about the suitability of carburizing for their specific applications and select the appropriate materials and processes to achieve the desired results.
Summary Table:
Key Aspect | Details |
---|---|
Purpose | Increases surface hardness, wear resistance, and fatigue strength. |
Process | Heating steel in a carbon-rich environment, followed by quenching. |
Types | Gas, vacuum, liquid, and pack carburizing. |
Applications | Gears, shafts, bearings, fasteners, and tools. |
Advantages | Hard surface, tough core, improved fatigue strength, and selective hardening. |
Limitations | Energy-intensive, risk of distortion, and requires precise control. |
Discover how carburizing can improve your components' performance—contact our experts today for tailored solutions!