Heat treatment annealing is a critical process used to enhance the mechanical properties of metallic alloys, such as hardness, strength, ductility, and toughness. By heating the material to a specific temperature, holding it for a predetermined time, and then cooling it at a controlled rate, annealing refines the microstructure of the metal. This process reduces internal stresses, improves grain uniformity, and increases ductility, making the material more workable and machinable. Additionally, annealing can modify electrical properties and relieve stresses in castings, making it suitable for both ferrous and non-ferrous alloys. Specific annealing techniques, such as low hydrogen annealing, can further influence mechanical properties by altering dislocation dynamics and reducing hydrogen embrittlement.
Key Points Explained:
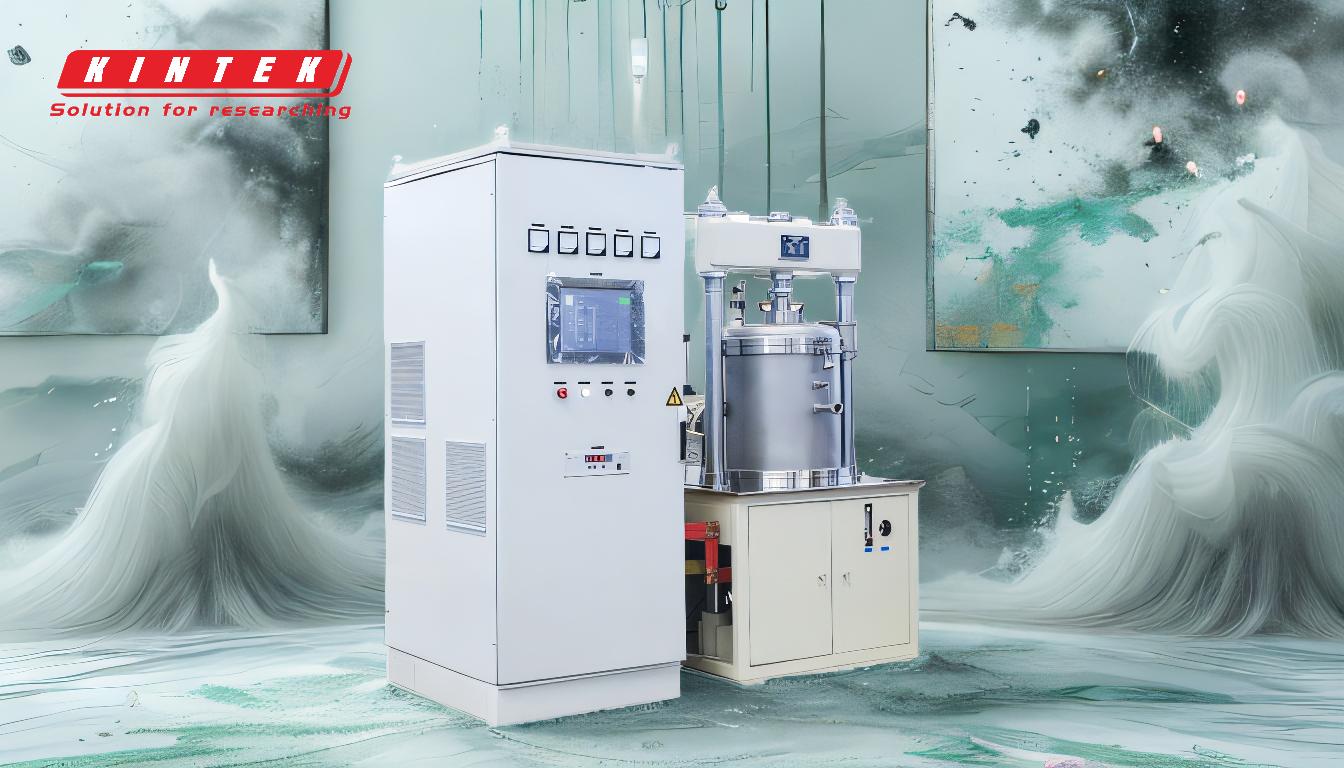
-
Refinement of Microstructure:
- Annealing involves heating the material to a specific temperature and holding it there to allow for the diffusion of atoms within the microstructure. This process refines the grain structure, making it more uniform and reducing defects such as dislocations and voids.
- A refined microstructure improves mechanical properties like ductility and toughness, as the material becomes more homogeneous and less prone to localized stress concentrations.
-
Reduction of Internal Stresses:
- During manufacturing processes like casting, rolling, or welding, internal stresses can develop within the material. These stresses can lead to cracking, warping, or premature failure.
- Annealing relieves these internal stresses by allowing the material to relax and redistribute its internal energy. This makes the material more stable and less likely to fail under load.
-
Increased Ductility and Workability:
- By reducing hardness and increasing ductility, annealing makes the material easier to machine, shape, or form. This is particularly important for materials that need to undergo further processing, such as cold working or machining.
- Increased ductility also improves the material's ability to absorb energy before fracturing, enhancing its toughness.
-
Control of Mechanical Properties:
- Annealing allows for precise control over mechanical properties such as hardness, strength, and elasticity. For example, in steels, annealing can reduce hardness and increase ductility, making the material more suitable for applications requiring flexibility.
- The cooling rate during annealing plays a significant role in determining the final properties. Slow cooling typically results in softer, more ductile materials, while faster cooling can retain some hardness.
-
Impact on Dislocation Dynamics:
- In specific annealing processes, such as low hydrogen annealing, the diffusion of atoms (e.g., carbon) into interstitial sites of dislocations can form a Cottrell atmosphere. This pins dislocations and reduces the density of movable dislocations, increasing yield strength but potentially decreasing elongation.
- This phenomenon is particularly relevant in high-strength steels, where annealing can improve resistance to hydrogen embrittlement by reducing internal hydrogen content.
-
Suitability for Ferrous and Non-Ferrous Alloys:
- Annealing is versatile and can be applied to a wide range of materials, including both ferrous (e.g., steel) and non-ferrous (e.g., aluminum, copper) alloys. The specific temperature and cooling rates are tailored to the material's composition and desired properties.
- For example, in aluminum alloys, annealing can improve formability and reduce residual stresses, making it easier to fabricate complex shapes.
-
Modification of Electrical Properties:
- In addition to mechanical properties, annealing can also influence electrical conductivity and resistivity. For instance, annealing copper wires can improve their conductivity by reducing defects and impurities in the crystal structure.
- This makes annealing a valuable process in the production of electrical components and wiring.
-
Application in Specific Scenarios:
- Low hydrogen annealing, as seen in X80 pipeline steel, demonstrates how annealing can address specific challenges like hydrogen embrittlement. By reducing internal hydrogen content, the material becomes more resistant to cracking and failure under stress.
- However, annealing may not be effective for surface-absorbed hydrogen, highlighting the importance of selecting the appropriate heat treatment process for the specific material and application.
By understanding these key points, a purchaser of equipment or consumables can make informed decisions about the heat treatment processes required to achieve the desired mechanical and electrical properties in their materials.
Summary Table:
Key Benefits of Annealing | Description |
---|---|
Refinement of Microstructure | Improves grain uniformity, reduces defects, and enhances ductility and toughness. |
Reduction of Internal Stresses | Relieves stress from manufacturing processes, preventing cracking and failure. |
Increased Ductility and Workability | Makes materials easier to machine, shape, or form. |
Control of Mechanical Properties | Adjusts hardness, strength, and elasticity for specific applications. |
Impact on Dislocation Dynamics | Reduces hydrogen embrittlement and improves yield strength in high-strength steels. |
Suitability for Various Alloys | Applicable to ferrous (e.g., steel) and non-ferrous (e.g., aluminum, copper) alloys. |
Modification of Electrical Properties | Enhances conductivity and reduces resistivity in materials like copper. |
Application in Specific Scenarios | Addresses challenges like hydrogen embrittlement in X80 pipeline steel. |
Ready to optimize your materials with heat treatment annealing? Contact our experts today to get started!