Isostatic pressing is a manufacturing process that applies uniform pressure in all directions to compact powder materials into a desired shape. This technique, based on Pascal's law, ensures uniform density and eliminates frictional forces that hinder conventional pressing methods. It is divided into cold isostatic pressing (CIP) and hot isostatic pressing (HIP), with CIP performed at ambient temperatures and HIP at elevated temperatures. CIP uses a flexible mold and a liquid medium, such as an oil-water mixture, to transmit hydrostatic pressure, reaching up to 100,000 psi. This process is advantageous for producing high-integrity billets with uniform density, reduced internal stresses, and minimal distortion or cracking. CIP is widely used in industries requiring complex shapes, close tolerances, and high-performance materials.
Key Points Explained:
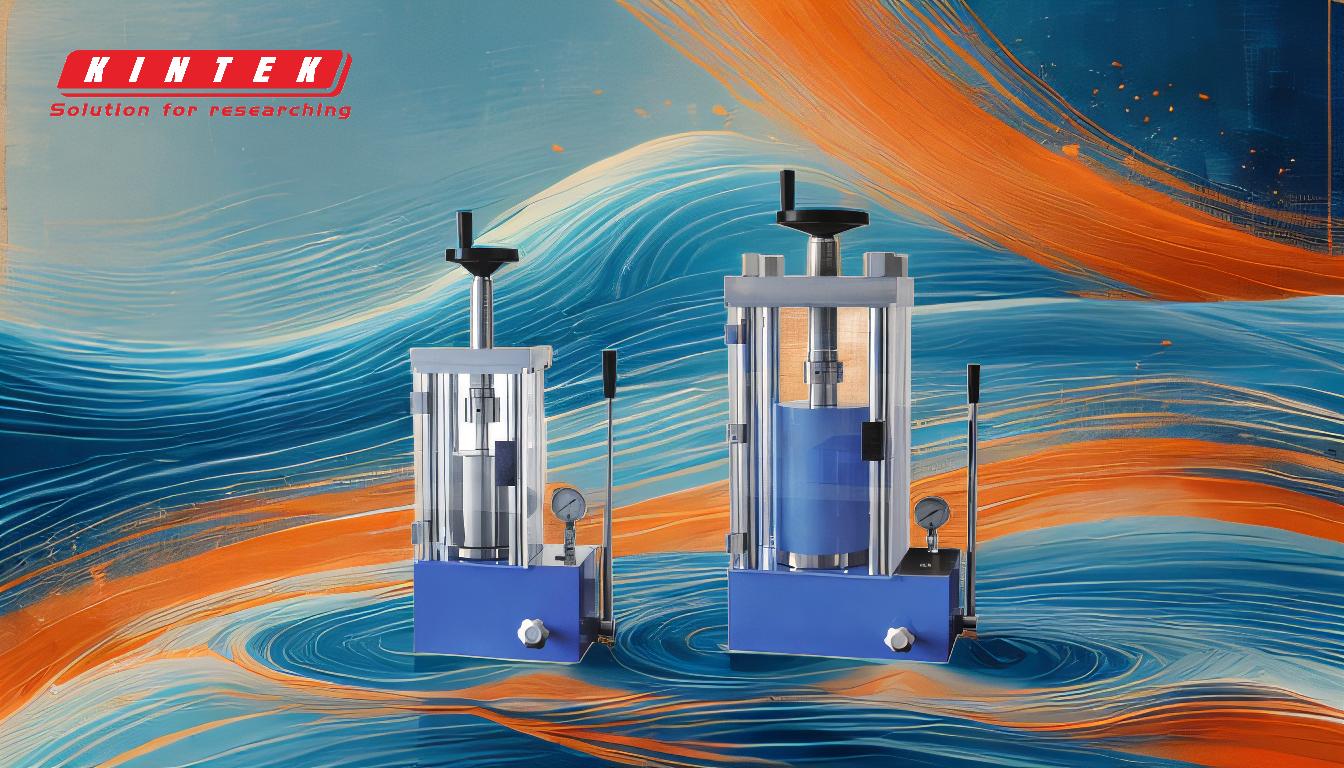
-
Principle of Isostatic Pressing
- Isostatic pressing operates on Pascal's law, which states that pressure applied to a confined fluid is transmitted uniformly in all directions.
- This principle ensures that the powder material is compacted uniformly, eliminating frictional forces that are common in conventional pressing techniques.
- The uniform pressure distribution results in products with consistent density and minimal internal stresses.
-
Types of Isostatic Pressing
-
Cold Isostatic Pressing (CIP):
- Performed at ambient temperatures.
- Uses a flexible mold (rubber or plastic) and a liquid medium (e.g., oil-water mixture) to apply hydrostatic pressure.
- Ideal for creating green parts with high integrity and minimal distortion.
-
Hot Isostatic Pressing (HIP):
- Conducted at elevated temperatures to fully consolidate parts through solid-state diffusion.
- Suitable for densifying materials and eliminating porosity in finished products.
-
Cold Isostatic Pressing (CIP):
-
Cold Isostatic Pressing Process
- The powder material is placed inside a flexible mold, which is then inserted into the CIP processing chamber.
- A liquid medium is pumped into the chamber and pressurized uniformly on all sides, reaching pressures as high as 100,000 psi.
- The uniform pressure compacts the powder into a dense, high-strength preform or billet.
- CIP is divided into two methods:
- Wet Bag Method: The mold is removed and refilled after each pressing cycle.
- Dry Bag Method: The mold remains in the chamber, and powder is filled and pressed repeatedly.
-
Advantages of Cold Isostatic Pressing
- Uniform Density: Ensures consistent material properties throughout the product.
- Reduced Internal Stresses: Minimizes the risk of cracks, strains, and laminations.
- High Green Strength: Produces parts with sufficient strength for handling and machining.
- Complex Shapes: Allows for the production of intricate geometries and close tolerances.
- Cost-Effective: The CIP process is relatively inexpensive compared to other molding techniques.
-
Applications of Isostatic Pressing
- Advanced Ceramics: Used to produce dense, high-performance ceramic components.
- Powder Metallurgy: Ideal for compacting metal powders into near-net-shape parts.
- Solid-State Batteries: Enables the production of thin, dense solid electrolyte layers.
- Aerospace and Automotive: Used for manufacturing high-strength, lightweight components.
-
Cold Isostatic Pressing Machine
- A cold isostatic pressing machine is the core equipment used in the CIP process.
- It consists of a high-pressure chamber, a pump system for pressurizing the liquid medium, and a control system to regulate pressure and timing.
- The machine's design ensures uniform pressure application, making it suitable for a wide range of materials and applications.
-
Future Trends and Technological Maturity
- The CIP process is gaining popularity due to its ability to improve product performance and quality.
- Advances in mold materials and pressure control systems are expanding its application fields.
- The technology is becoming more mature, with increasing adoption in industries requiring high-performance materials.
By leveraging the principles of isostatic pressing, manufacturers can produce high-quality components with superior mechanical properties, making it a valuable process in modern manufacturing.
Summary Table:
Aspect | Details |
---|---|
Principle | Based on Pascal's law, applying uniform pressure in all directions. |
Types | Cold Isostatic Pressing (CIP) and Hot Isostatic Pressing (HIP). |
CIP Process | Uses a flexible mold and liquid medium to apply up to 100,000 psi pressure. |
Advantages | Uniform density, reduced internal stresses, and cost-effectiveness. |
Applications | Advanced ceramics, powder metallurgy, aerospace, and automotive industries. |
Future Trends | Increasing adoption in high-performance material industries. |
Unlock the potential of isostatic pressing for your manufacturing needs—contact us today!