Temperature plays a critical role in the forging process, influencing the material's workability, microstructure, and final mechanical properties. Forging involves shaping metal using compressive forces, and the temperature at which this occurs determines the ease of deformation, the formation of defects, and the quality of the forged part. Higher temperatures generally make metals more malleable, reducing the force required for shaping, but excessive heat can lead to grain growth, oxidation, or even melting. Conversely, forging at lower temperatures can result in increased strength but may cause cracking or incomplete shaping. Understanding the optimal forging temperature range for specific materials is essential to achieve the desired balance between formability and mechanical properties.
Key Points Explained:
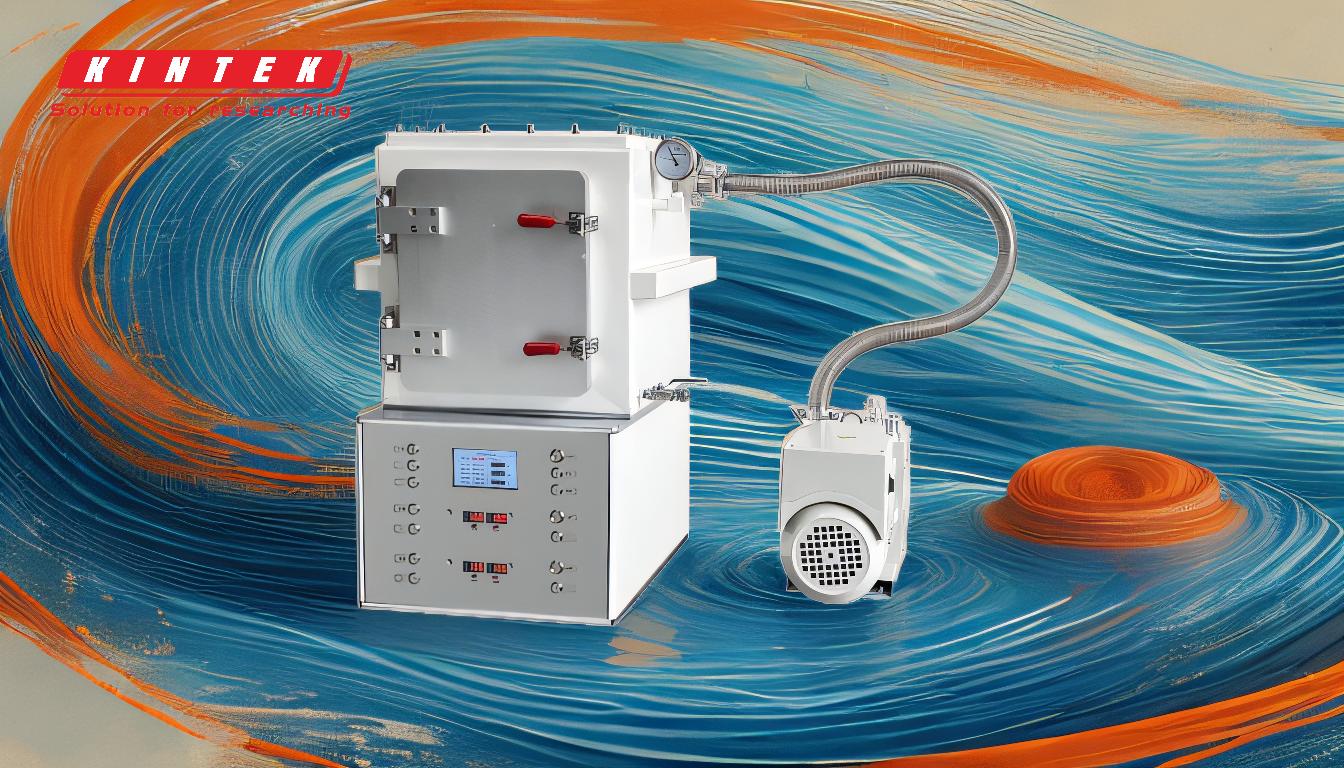
-
Temperature and Material Workability:
- Metals become more ductile and easier to shape as temperature increases. This is because higher temperatures reduce the material's yield strength, allowing it to deform more easily under compressive forces.
- Forging at elevated temperatures (hot forging) is common for materials like steel, aluminum, and titanium, as it minimizes the risk of cracking and ensures uniform deformation.
- Cold forging, performed at or near room temperature, is used for materials that exhibit sufficient ductility without heating, such as certain aluminum alloys. However, cold forging requires higher forces and may lead to work hardening.
-
Microstructural Changes:
- Temperature significantly affects the microstructure of the metal during forging. Hot forging promotes dynamic recrystallization, where new, strain-free grains form, improving the material's toughness and ductility.
- If the temperature is too high, excessive grain growth can occur, weakening the material. Conversely, forging at too low a temperature may result in incomplete recrystallization, leading to residual stresses and reduced mechanical properties.
-
Oxidation and Surface Quality:
- High temperatures during forging can cause oxidation, forming a layer of scale on the metal's surface. This scale must be removed to ensure a clean finish, but it can also lead to material loss and dimensional inaccuracies.
- Proper temperature control and protective atmospheres can minimize oxidation, preserving the surface quality and dimensional precision of the forged part.
-
Thermal Expansion and Dimensional Accuracy:
- Metals expand when heated, and this thermal expansion must be accounted for in the forging process. Overheating can lead to excessive expansion, making it challenging to achieve precise dimensions.
- Accurate temperature control ensures that the forged part cools uniformly, maintaining dimensional stability and reducing the risk of warping or distortion.
-
Energy Efficiency and Process Optimization:
- Higher forging temperatures reduce the force required for deformation, making the process more energy-efficient. However, excessive heating can lead to energy waste and increased operational costs.
- Optimizing the forging temperature range for specific materials and applications ensures a balance between energy efficiency, material properties, and production costs.
-
Material-Specific Temperature Ranges:
- Different metals have unique forging temperature ranges. For example, steel is typically forged between 950°C and 1250°C, while aluminum alloys are forged at lower temperatures (around 350°C to 500°C).
- Exceeding the recommended temperature range can lead to melting or undesirable phase changes, while forging below the range may result in inadequate deformation and poor mechanical properties.
-
Post-Forging Heat Treatment:
- The temperature during forging also influences the need for subsequent heat treatments. Forged parts may require annealing, quenching, or tempering to achieve the desired hardness, strength, and toughness.
- Proper temperature control during forging ensures that the material is in an optimal state for post-forging treatments, enhancing the final product's performance.
In conclusion, temperature is a critical factor in forging, affecting everything from material workability and microstructure to surface quality and dimensional accuracy. By carefully controlling the forging temperature, manufacturers can produce high-quality parts with the desired mechanical properties while minimizing defects and energy consumption. Understanding the temperature requirements for specific materials and applications is essential for optimizing the forging process and achieving consistent results.
Summary Table:
Aspect | Impact of Temperature |
---|---|
Material Workability | Higher temperatures increase ductility, reducing deformation force. |
Microstructure | Hot forging promotes recrystallization; excessive heat causes grain growth. |
Oxidation & Surface | High temps cause oxidation; controlled temps preserve surface quality. |
Dimensional Accuracy | Thermal expansion affects precision; uniform cooling prevents warping. |
Energy Efficiency | Higher temps reduce force but may waste energy; optimize for cost-effectiveness. |
Material-Specific Ranges | Steel: 950°C–1250°C; Aluminum: 350°C–500°C. Exceeding ranges risks defects. |
Post-Forging Treatment | Proper forging temps ensure optimal conditions for annealing, quenching, or tempering. |
Need expert advice on optimizing forging temperatures for your materials? Contact us today to get started!