The Physical Vapor Deposition (PVD) process is a vacuum-based coating technique used to deposit thin films of materials onto a substrate. It involves converting a solid material into a vapor state through physical means, such as high-temperature vacuum or plasma, transporting the vapor to the substrate, and condensing it to form a thin, uniform layer. PVD is widely used for its ability to create durable, high-performance coatings with applications in reducing friction, improving oxidation resistance, and enhancing hardness. The process is conducted under low-pressure conditions and typically involves steps like sputtering, evaporation, and thermal treatment.
Key Points Explained:
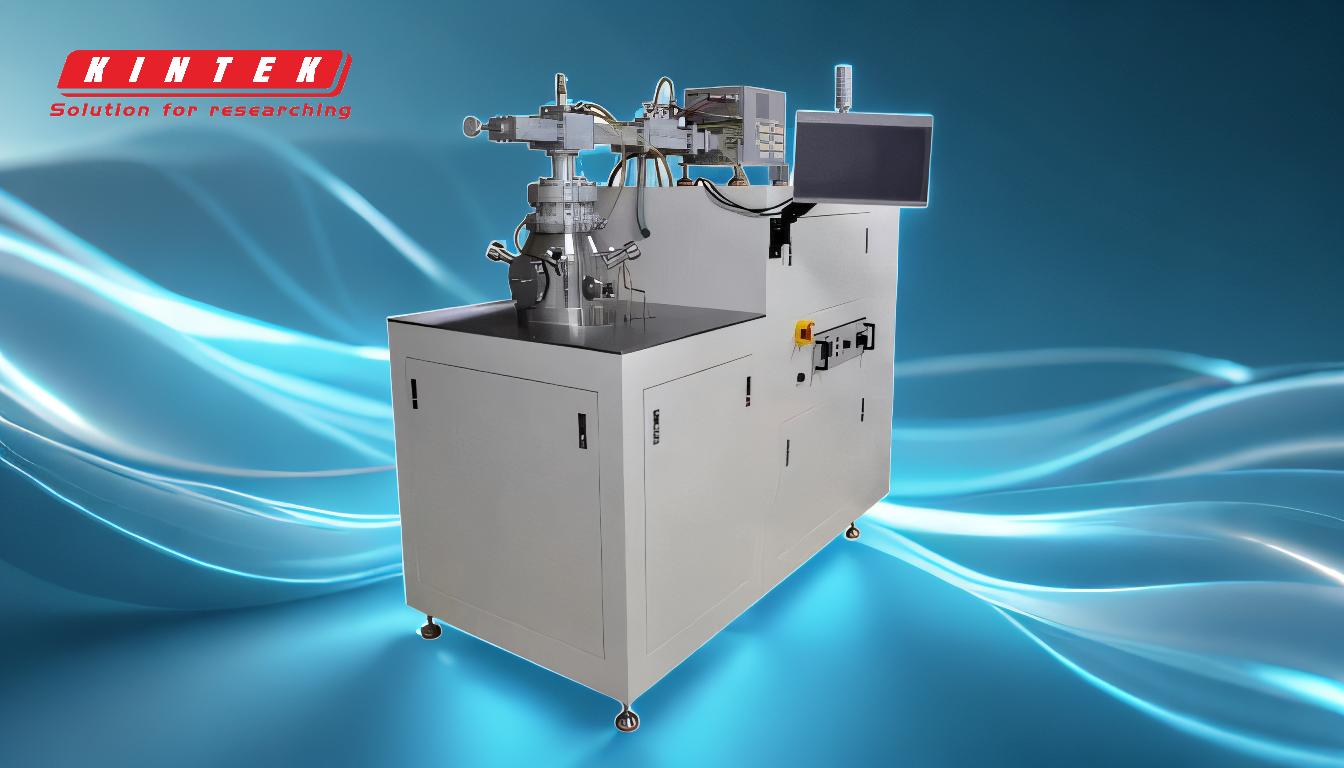
-
Vaporization of the Source Material:
- The PVD process begins with the conversion of a solid precursor material into a vapor. This is achieved through physical methods such as high-temperature vacuum, electron beam bombardment, or plasma discharge.
- For example, a solid metal target is bombarded with high-energy electrons or ions, causing atoms to be ejected from the surface in a process known as sputtering.
- The vaporized atoms are then transported through a low-pressure environment to the substrate.
-
Transport of Vapor to the Substrate:
- The vaporized material is transported from the source to the substrate in a vacuum chamber. This step ensures that the vaporized atoms travel in a straight line (line-of-sight deposition) without interference from background gases.
- The vacuum environment minimizes contamination and ensures a clean deposition process.
- In some cases, reactive gases may be introduced into the chamber to create compound coatings (e.g., nitrides or oxides).
-
Condensation and Film Formation:
- Once the vaporized atoms reach the substrate, they condense and form a thin, uniform film. The thickness of the film can range from nanometers to micrometers, depending on the application.
- The condensation process is influenced by factors such as substrate temperature, deposition rate, and the presence of reactive gases.
- The resulting film adheres strongly to the substrate, providing enhanced properties such as hardness, wear resistance, and corrosion resistance.
-
Types of PVD Techniques:
- Sputtering: A target material is bombarded with high-energy ions, causing atoms to be ejected and deposited onto the substrate. This technique is widely used for depositing metals, alloys, and compounds.
- Evaporation: The source material is heated to its evaporation point, and the vaporized atoms are deposited onto the substrate. This method is commonly used for depositing thin films of metals and semiconductors.
- Arc Vapor Deposition: An electric arc is used to vaporize the source material, which is then deposited onto the substrate. This technique is often used for hard coatings like titanium nitride (TiN).
-
Advantages of PVD:
- High-Quality Coatings: PVD produces dense, uniform coatings with excellent adhesion and durability.
- Versatility: It can deposit a wide range of materials, including metals, ceramics, and some organic compounds.
- Environmentally Friendly: PVD is a clean process that does not involve hazardous chemicals or produce harmful byproducts.
- Precision: The process allows for precise control over film thickness and composition, making it suitable for applications in microelectronics, optics, and tool coatings.
-
Applications of PVD:
- Tool and Die Coatings: PVD is used to coat cutting tools, molds, and dies with hard, wear-resistant materials like titanium nitride (TiN) and diamond-like carbon (DLC).
- Decorative Coatings: PVD is used to create durable, scratch-resistant coatings on watches, jewelry, and consumer electronics.
- Semiconductor Manufacturing: PVD is employed to deposit thin films of metals and dielectrics in the fabrication of integrated circuits and microelectronic devices.
- Optical Coatings: PVD is used to create anti-reflective, reflective, and protective coatings on lenses, mirrors, and other optical components.
-
Process Control and Monitoring:
- The PVD process is carefully controlled to ensure consistent film quality. Parameters such as chamber pressure, substrate temperature, and deposition rate are monitored and adjusted as needed.
- A quartz crystal rate monitor is often used to measure the thickness of the deposited film in real-time, ensuring precise control over the coating process.
In summary, the PVD process is a versatile and precise method for depositing thin films with a wide range of applications. By converting a solid material into a vapor and condensing it onto a substrate, PVD creates coatings that enhance the performance and durability of various products.
Summary Table:
Aspect | Details |
---|---|
Process Overview | Converts solid material into vapor, transports it, and condenses it into a thin film. |
Key Techniques | Sputtering, Evaporation, Arc Vapor Deposition |
Advantages | High-quality, durable, versatile, environmentally friendly, precise control |
Applications | Tool coatings, decorative coatings, semiconductors, optical coatings |
Process Control | Monitored parameters: pressure, temperature, deposition rate |
Discover how PVD coatings can enhance your products—contact our experts today for tailored solutions!