Vacuum coating is a sophisticated thin-film technology used to deposit protective or functional layers on metal parts by creating a sub-atmospheric pressure environment. This process involves vaporizing or ionizing coating materials (metallic or ceramic) in a vacuum chamber using thermal energy or plasma. The two primary methods are Physical Vapor Deposition (PVD) and Chemical Vapor Deposition (CVD), which create nanoscale coatings with enhanced properties such as hardness, wear resistance, and corrosion protection. The process typically includes surface preparation, application of the coating material, and curing to form a durable, solid layer.
Key Points Explained:
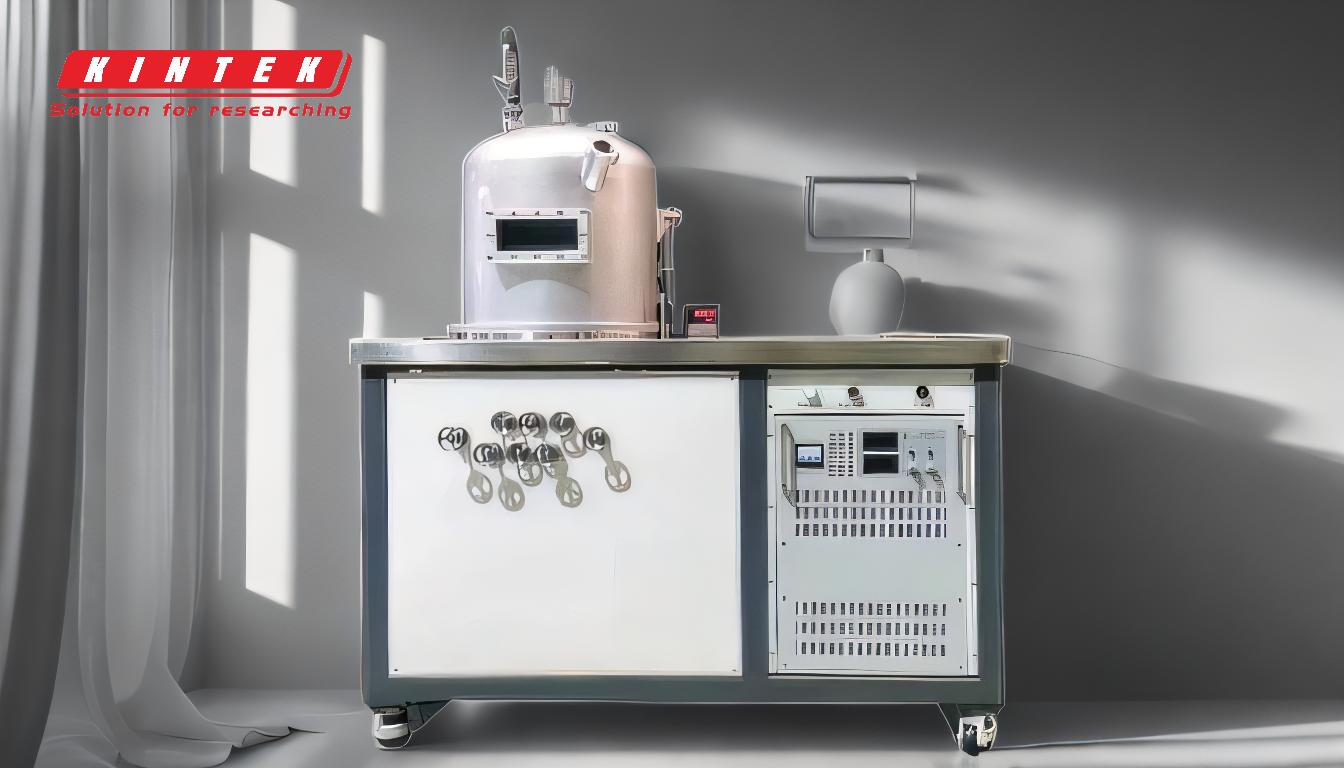
-
Vacuum Environment:
- Vacuum coating operates in a sub-atmospheric pressure environment, which minimizes contamination and ensures a clean deposition process. This environment allows for better control over the coating's properties and uniformity.
- The vacuum chamber is essential for creating the right conditions for vaporization or ionization of the coating material, ensuring that the atoms or molecules can travel freely and adhere uniformly to the substrate.
-
Coating Material Vaporization/Ionization:
- The coating material (metallic or ceramic) is vaporized or ionized using thermal energy or plasma within the vacuum chamber. This step is crucial for creating the atomic or molecular condensable vapor source.
- Vaporization can be achieved through methods like sputtering, evaporation, or arc deposition, depending on the material and desired coating properties.
-
Deposition Methods (PVD and CVD):
- Physical Vapor Deposition (PVD): Involves physically vaporizing the coating material and depositing it onto the substrate. PVD techniques include sputtering, evaporation, and ion plating. These methods are known for producing dense, adherent coatings with excellent mechanical properties.
- Chemical Vapor Deposition (CVD): Involves chemical reactions to form the coating material on the substrate. CVD is used for creating coatings with complex compositions and structures, often at higher temperatures.
-
Surface Preparation:
- Before coating, the surface of the metal parts is thoroughly cleaned, often using abrasive liquids, to remove contaminants and ensure strong adhesion of the coating.
- Proper surface preparation is critical for achieving a uniform and durable coating.
-
Application and Curing:
- The coating material is applied in liquid or powder form, depending on the process. After application, the coating is dried and cured to form a solid, protective layer.
- Curing may involve heat treatment or chemical reactions to harden the coating and enhance its properties.
-
Properties of Vacuum Coatings:
- Vacuum coatings are extremely thin, often at the nanoscale, but they provide significant improvements in hardness, wear resistance, and corrosion protection.
- These coatings can also enhance the aesthetic appearance of the metal parts, making them suitable for decorative applications.
-
Applications:
- Vacuum coating is widely used in industries such as aerospace, automotive, electronics, and medical devices. It is also used for decorative finishes on consumer products.
- The ability to create thin, durable, and functional coatings makes vacuum coating a versatile technology for various applications.
By understanding these key points, one can appreciate the complexity and precision involved in vacuum coating processes, which are essential for creating high-performance and durable coatings on metal parts.
Summary Table:
Aspect | Details |
---|---|
Vacuum Environment | Sub-atmospheric pressure minimizes contamination, ensuring clean deposition. |
Coating Methods | PVD (sputtering, evaporation) and CVD (chemical reactions). |
Surface Preparation | Cleaning with abrasive liquids for strong adhesion. |
Coating Properties | Nanoscale thickness, improved hardness, wear resistance, and aesthetics. |
Applications | Aerospace, automotive, electronics, medical devices, and decorative uses. |
Discover how vacuum coating can transform your metal parts—contact us today for expert solutions!