Graphene is a remarkable material with unique properties, and its production methods are crucial for determining its quality and applications. The synthesis of graphene can be broadly categorized into two approaches: top-down and bottom-up methods. The top-down methods involve deriving graphene from graphite, while bottom-up methods, such as chemical vapor deposition (CVD), build graphene atom by atom. Among these, CVD is the most promising for producing large-area, high-quality graphene, making it the preferred method for industrial applications. Other methods, such as mechanical exfoliation and liquid-phase exfoliation, are more suited for research purposes due to their limitations in scalability and quality.
Key Points Explained:
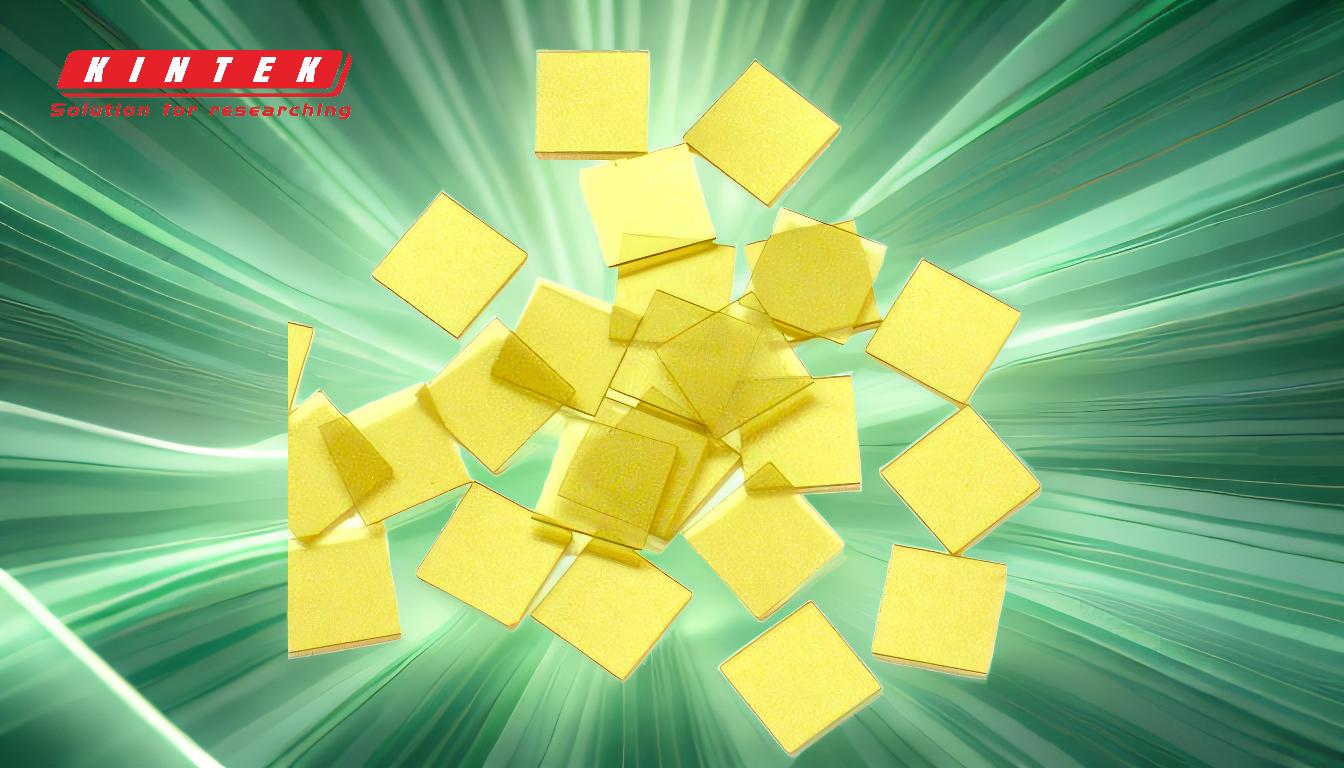
-
Top-Down Methods:
- Mechanical Exfoliation: This method involves peeling layers of graphene from graphite using adhesive tape. It is a simple and cost-effective technique, often used in research settings to produce high-quality graphene flakes. However, it is not scalable for industrial production.
- Liquid-Phase Exfoliation: Graphite is dispersed in a liquid medium and subjected to ultrasonic waves to separate the layers. This method is scalable but produces graphene with lower electrical quality, limiting its use in high-performance applications.
- Reduction of Graphene Oxide (GO): Graphene oxide is chemically reduced to produce graphene. This method is cost-effective and scalable but often results in graphene with structural defects and impurities.
-
Bottom-Up Methods:
- Chemical Vapor Deposition (CVD): CVD is the most widely used method for producing high-quality, large-area graphene. It involves the decomposition of carbon-containing gases (e.g., methane) at high temperatures on a substrate, typically a transition metal like copper or nickel. The carbon atoms then form a graphene layer on the substrate. CVD is scalable and produces graphene with excellent electrical and mechanical properties, making it ideal for industrial applications.
- Epitaxial Growth: Graphene is grown on a crystalline substrate, such as silicon carbide (SiC), by heating the substrate to high temperatures, causing the silicon to sublimate and leaving behind a graphene layer. This method produces high-quality graphene but is expensive and limited by the availability of suitable substrates.
- Arc Discharging: This method involves creating an electric arc between two graphite electrodes in an inert gas atmosphere. The arc vaporizes the graphite, and the carbon atoms recombine to form graphene. While this method can produce graphene with good quality, it is less controlled and scalable compared to CVD.
-
CVD Process in Detail:
- Step 1: Precursor Pyrolysis: A carbon-containing gas (e.g., methane) is introduced into a high-temperature chamber, where it decomposes into carbon atoms. The substrate (e.g., copper or nickel) is heated to facilitate the adsorption of carbon atoms on its surface.
- Step 2: Graphene Formation: The carbon atoms diffuse across the substrate surface and bond together to form a continuous graphene layer. The use of catalysts (e.g., copper) helps reduce the reaction temperature and improve the quality of the graphene.
- Step 3: Cooling and Transfer: After the graphene layer is formed, the substrate is cooled, and the graphene is transferred to a desired surface for further use. This step is critical for maintaining the integrity of the graphene layer.
-
Advantages and Disadvantages of Different Methods:
- Mechanical Exfoliation: Produces high-quality graphene but is not scalable.
- Liquid-Phase Exfoliation: Scalable but results in lower-quality graphene.
- Reduction of Graphene Oxide: Cost-effective but introduces defects.
- CVD: Produces high-quality, large-area graphene but requires precise control of process parameters and is relatively expensive.
- Epitaxial Growth: High-quality graphene but limited by substrate availability and cost.
- Arc Discharging: Produces good-quality graphene but is less controlled and scalable.
In conclusion, the choice of graphene production method depends on the intended application. For research purposes, mechanical exfoliation and liquid-phase exfoliation are suitable, while CVD is the preferred method for industrial-scale production due to its ability to produce high-quality, large-area graphene. Each method has its own set of advantages and trade-offs, and ongoing research aims to optimize these processes for broader applications.
Summary Table:
Method | Type | Scalability | Quality | Cost | Best Use |
---|---|---|---|---|---|
Mechanical Exfoliation | Top-Down | Low | High | Low | Research |
Liquid-Phase Exfoliation | Top-Down | Medium | Medium | Low | Research/Applications |
Reduction of Graphene Oxide | Top-Down | High | Low-Medium | Low | Cost-effective Production |
Chemical Vapor Deposition (CVD) | Bottom-Up | High | High | High | Industrial Applications |
Epitaxial Growth | Bottom-Up | Low | High | High | High-quality Production |
Arc Discharging | Bottom-Up | Medium | Medium | Medium | General Applications |
Want to learn more about graphene production methods? Contact our experts today for tailored solutions!