PVD (Physical Vapor Deposition) coating is a sophisticated process used to apply thin, highly adherent, and durable coatings to various substrates. The process involves several key steps, including cleaning and pretreatment of the substrate, vaporization of the target material, transportation of vaporized atoms, reaction with gases (if necessary), and deposition onto the substrate. This results in a micron-thick layer that interpenetrates with the underlying material, providing excellent adhesion and resistance to flaking or chipping. The process is conducted in a vacuum environment using inert gases like Argon to ensure a chemically unreactive atmosphere, which enhances the quality and durability of the coating.
Key Points Explained:
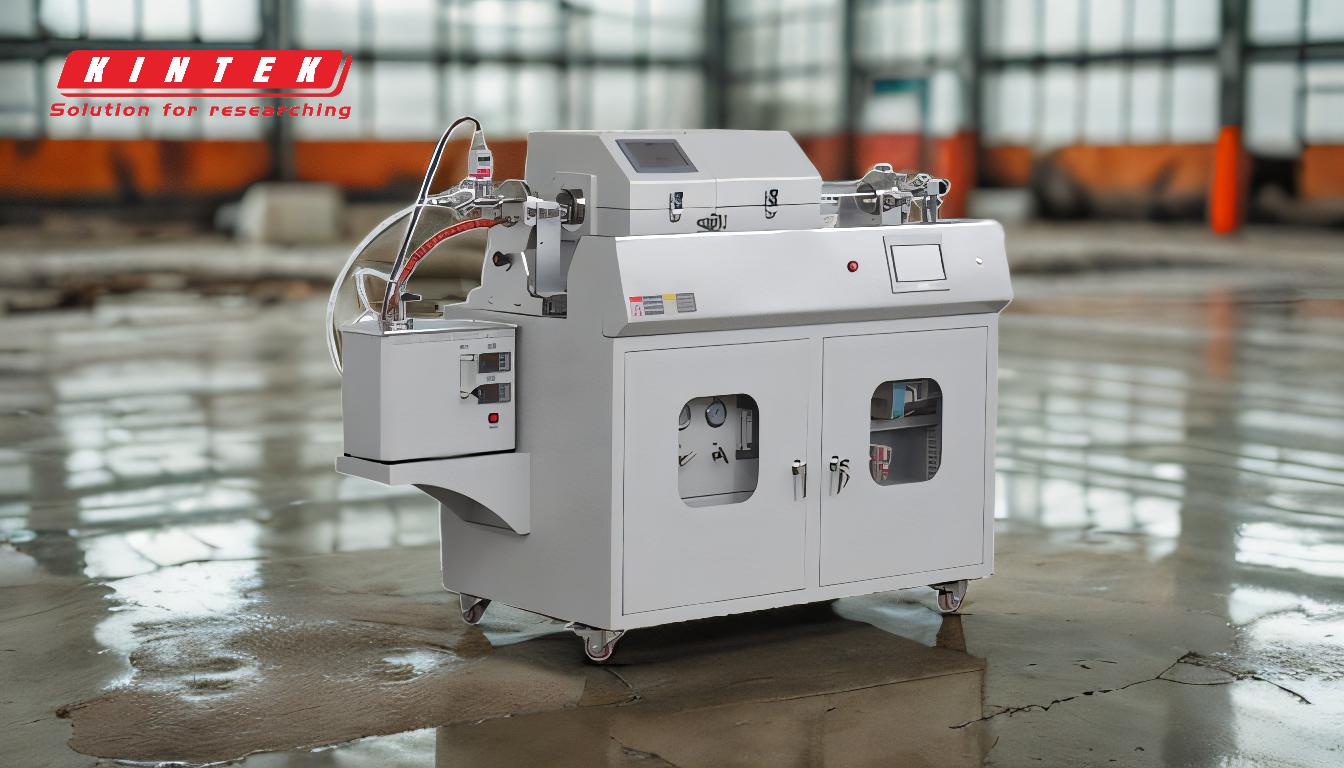
-
Cleaning and Pretreatment of the Substrate:
- Cleaning: The substrate must be thoroughly cleaned to remove any contaminants such as oils, dust, or oxides. This is crucial because any impurities on the surface can negatively affect the adhesion and quality of the coating. Cleaning methods may include ultrasonic cleaning, chemical cleaning, or plasma cleaning.
- Pretreatment: After cleaning, the substrate often undergoes pretreatment processes to improve coating adhesion. This may involve surface roughening, ion bombardment, or the application of a primer layer. Pretreatment ensures that the surface is chemically and physically prepared to receive the coating.
-
Vaporization of the Target Material:
- Evaporation/Ablation: The target material, which is the source of the coating, is placed in a vacuum chamber. High-energy sources such as electrons, ions, or lasers are used to bombard the target material, causing it to vaporize. This process converts the solid target material into a vapor phase.
- Transportation: The vaporized atoms or molecules are then transported through the vacuum chamber towards the substrate. The vacuum environment ensures that the vaporized particles travel without interference from air molecules, allowing for a more controlled and uniform deposition.
-
Reaction with Gases (if necessary):
- Reaction: In some cases, the vaporized atoms react with selected gases (such as nitrogen, oxygen, or methane) introduced into the chamber. This reaction forms compounds like metal oxides, nitrides, or carbides, which determine the final properties of the coating, such as hardness, color, and chemical resistance.
- Control of Reaction Conditions: The reaction conditions, including gas composition, pressure, and temperature, are carefully controlled to achieve the desired coating properties. For example, introducing nitrogen gas can result in the formation of metal nitrides, which are known for their hardness and wear resistance.
-
Deposition onto the Substrate:
- Condensation: The vaporized atoms or molecules condense onto the substrate surface, forming a thin film. The deposition process is controlled to ensure uniform coverage and thickness. The coating builds up layer by layer, bonding strongly with the substrate.
- Adhesion: The coating interpenetrates with the underlying material, creating a strong bond that prevents flaking or chipping. This is one of the key advantages of PVD coatings, as they provide excellent adhesion and durability.
-
Quality Control and Finishing:
- Quality Control: After deposition, the coated substrate undergoes quality control checks to ensure that the coating meets the required specifications. This may include measurements of thickness, hardness, adhesion, and surface roughness. Any defects or inconsistencies are identified and addressed.
- Finishing: Depending on the application, the coated substrate may undergo additional finishing processes to enhance its appearance or performance. This could include polishing, annealing, or applying a topcoat to improve corrosion resistance or aesthetic appeal.
-
Use of Inert Gases:
- Inert Atmosphere: Throughout the PVD process, inert gases like Argon are used to create a chemically unreactive atmosphere. This prevents unwanted reactions between the coating material and the environment, ensuring the purity and quality of the coating. The inert gas also helps to remove residual vapors from the chamber after the deposition process is complete.
-
Vacuum Environment:
-
High-Vacuum Conditions: The entire PVD process takes place in a high-vacuum environment. This is essential for several reasons:
- Minimizing Contamination: The vacuum reduces the presence of contaminants that could interfere with the coating process.
- Controlled Deposition: The vacuum allows for precise control over the deposition process, ensuring uniform and high-quality coatings.
- Energy Efficiency: The vacuum environment minimizes energy losses, making the process more efficient.
-
High-Vacuum Conditions: The entire PVD process takes place in a high-vacuum environment. This is essential for several reasons:
-
Applications and Benefits:
- Wide Range of Applications: PVD coatings are used in various industries, including automotive, aerospace, medical devices, and consumer electronics. They are valued for their ability to enhance the performance, durability, and aesthetics of components.
- Benefits: PVD coatings offer numerous benefits, including high hardness, wear resistance, corrosion resistance, and the ability to create decorative finishes. They are also environmentally friendly, as they do not involve harmful chemicals or produce hazardous waste.
In summary, the PVD coating process is a highly controlled and precise method for applying thin, durable, and adherent coatings to a wide range of substrates. By understanding each step of the process, from cleaning and pretreatment to deposition and quality control, one can appreciate the complexity and sophistication involved in creating high-performance PVD coatings.
Summary Table:
Step | Description |
---|---|
Cleaning & Pretreatment | Removes contaminants and prepares the substrate for better adhesion. |
Vaporization | Target material is vaporized using high-energy sources in a vacuum chamber. |
Reaction with Gases | Vaporized atoms react with gases to form compounds like nitrides or carbides. |
Deposition | Vaporized atoms condense onto the substrate, forming a thin, durable coating. |
Quality Control | Ensures the coating meets specifications for thickness, hardness, and adhesion. |
Inert Gases | Argon or other inert gases create a chemically unreactive atmosphere for high-quality coatings. |
Vacuum Environment | High-vacuum conditions minimize contamination and ensure precise, uniform deposition. |
Applications | Used in automotive, aerospace, medical devices, and consumer electronics for enhanced performance. |
Benefits | High hardness, wear resistance, corrosion resistance, and decorative finishes. |
Ready to enhance your components with PVD coatings? Contact us today to learn more!