XRF (X-ray fluorescence) testing is a non-destructive analytical technique used to determine the elemental composition of materials. It works by emitting X-rays that excite the atoms in a sample, causing them to fluoresce and emit secondary X-rays. These emitted X-rays are detected and analyzed to identify the elements present and their concentrations. The process involves four main steps: emission, excitation, measurement, and analysis. XRF is widely used in industries such as metallurgy, recycling, and environmental monitoring due to its speed, accuracy, and ability to analyze materials without damaging them. However, factors like sample preparation, moisture, and matrix effects must be carefully managed to ensure reliable results.
Key Points Explained:
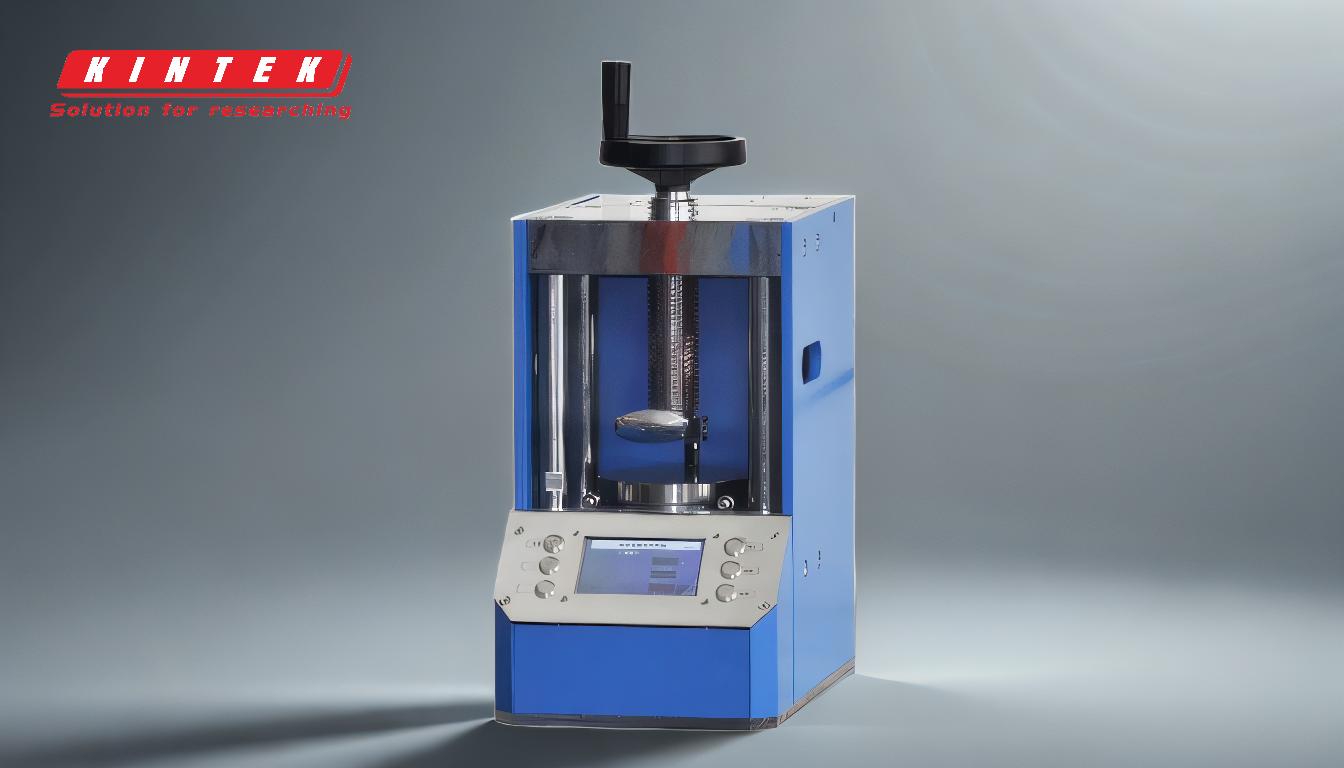
-
How XRF Works:
- XRF analyzers emit X-rays that interact with the sample, causing the atoms in the sample to fluoresce and emit secondary X-rays.
- These secondary X-rays are detected by the analyzer, which measures their energy spectrum to identify the elements present and their quantities.
- The process is non-destructive, meaning the sample remains intact after testing.
-
Steps in XRF Testing:
- Emission: The analyzer emits X-rays toward the sample.
- Excitation: The X-rays hit the sample, causing the atoms to fluoresce and emit characteristic X-rays.
- Measurement: The detector measures the energy spectrum of the emitted X-rays, identifying the elements and their concentrations.
- Analysis: The results are processed and used for applications such as material verification, recycling, and environmental assessments.
-
Applications of XRF:
- XRF is widely used in metallurgy to determine the composition of metals and alloys.
- It is also used in scrap recycling to identify and sort materials.
- Environmental monitoring uses XRF to detect contaminants in soil, water, and air.
-
Sample Preparation:
- For loose powdered materials, the sample is placed in a plastic cup with a support film to ensure a flat surface and proper support over the X-ray beam.
- The sample should be finely ground to achieve homogeneity and minimize void spaces.
- For metal powders, care must be taken to prevent overheating in high-power instruments, which could melt the support film.
-
Factors Affecting XRF Results:
- Sample Container or Display: The type of container or film used can influence the results.
- Particle Size: Finely ground samples provide more accurate results.
- Moisture: Wet samples can affect the fluorescence intensity.
- Heterogeneity: Non-uniform samples may yield inconsistent results.
- Sample Matrix: The composition of the sample matrix can interfere with the analysis.
-
Advantages of XRF:
- Non-Destructive: The sample remains intact after analysis.
- Fast and Reliable: Results are obtained quickly with high accuracy.
- Versatile: Suitable for a wide range of materials and applications.
-
Limitations of XRF:
- Surface Sensitivity: XRF primarily analyzes the surface of the sample, so surface contamination can affect results.
- Matrix Effects: The composition of the sample matrix can interfere with the analysis, requiring careful calibration.
- Detection Limits: XRF may not detect trace elements at very low concentrations.
By understanding these key points, users can effectively apply XRF testing in various industries and ensure accurate and reliable results. Proper sample preparation and consideration of influencing factors are crucial for optimal performance.
Summary Table:
Aspect | Details |
---|---|
How XRF Works | Emits X-rays to excite atoms, causing fluorescence and secondary X-ray emission. |
Steps in XRF Testing | Emission → Excitation → Measurement → Analysis. |
Applications | Metallurgy, recycling, environmental monitoring. |
Sample Preparation | Finely ground, placed in a plastic cup with support film for loose powders. |
Factors Affecting Results | Sample container, particle size, moisture, heterogeneity, matrix effects. |
Advantages | Non-destructive, fast, reliable, and versatile. |
Limitations | Surface sensitivity, matrix effects, detection limits for trace elements. |
Discover how XRF testing can benefit your industry—contact our experts today for more information!