Molecular sieves are highly effective desiccants used to adsorb water and other molecules from gases and liquids. Their lifespan depends on several factors, including the type of molecular sieve, the operating conditions, and the regeneration process. Generally, molecular sieves can last for several years if properly maintained and regenerated. However, their performance degrades over time due to factors such as contamination, thermal degradation, and physical wear. Regular regeneration and proper handling can significantly extend their lifespan. Below, the key factors influencing the lifespan of molecular sieves are explained in detail.
Key Points Explained:
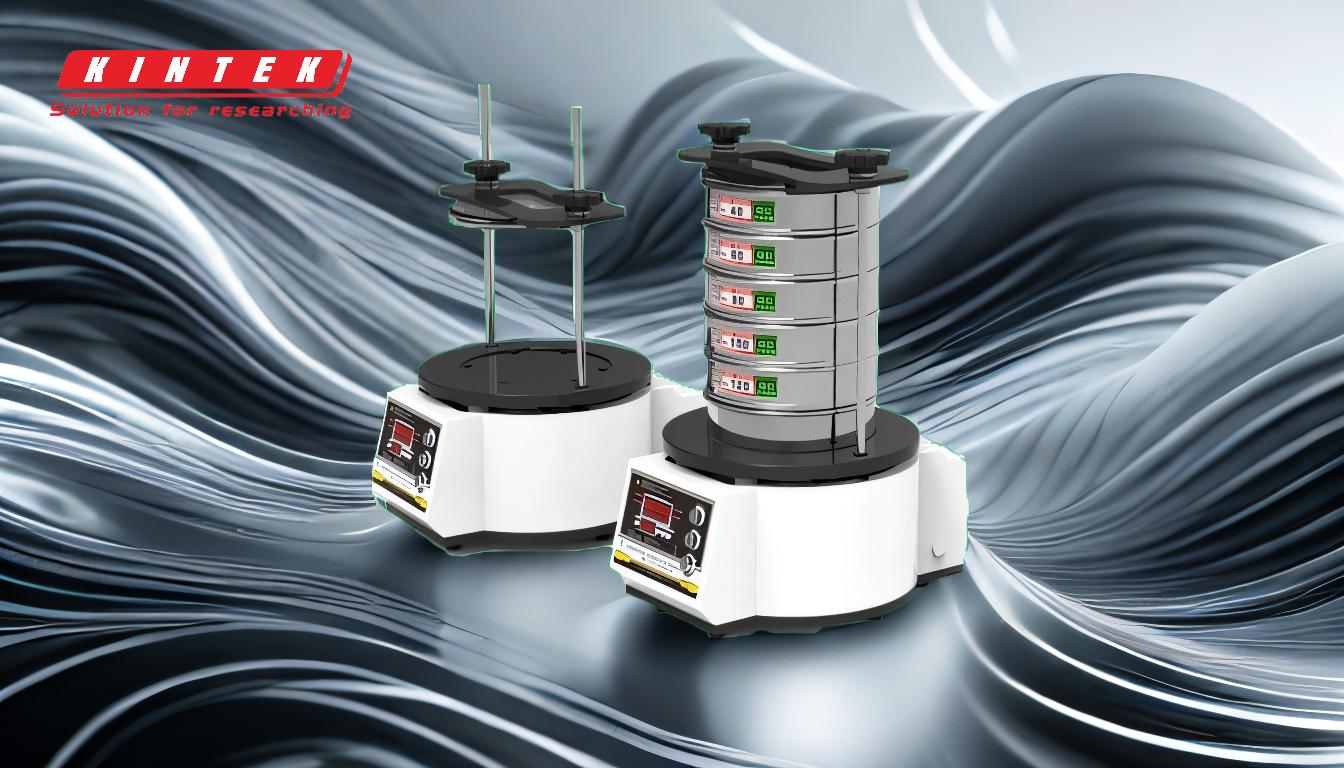
-
Type of Molecular Sieve:
- Different types of molecular sieves (e.g., 3A, 4A, 5A, 13X) have varying lifespans due to their unique pore sizes and chemical compositions.
- For example, 3A molecular sieves are commonly used for drying gases like natural gas and are less prone to contamination, which can extend their lifespan.
- 13X molecular sieves, used for broader applications, may degrade faster if exposed to contaminants like hydrocarbons or heavy metals.
-
Operating Conditions:
- The lifespan of molecular sieves is heavily influenced by the environment in which they operate.
- High humidity levels, elevated temperatures, and exposure to aggressive chemicals can accelerate degradation.
- For instance, molecular sieves used in industrial gas drying systems may last longer than those used in high-temperature processes like catalytic cracking.
-
Regeneration Process:
- Proper regeneration is critical to maintaining the effectiveness and longevity of molecular sieves.
- Regeneration typically involves heating the molecular sieves to remove adsorbed moisture and contaminants. The temperature and duration of regeneration must be carefully controlled to avoid thermal damage.
- Improper regeneration (e.g., insufficient heating or overheating) can lead to irreversible degradation, reducing the lifespan of the sieves.
-
Contamination:
- Contaminants such as oils, hydrocarbons, and heavy metals can clog the pores of molecular sieves, reducing their adsorption capacity.
- Once contaminated, molecular sieves may lose their effectiveness and require replacement, even if they are regenerated.
- Pre-filtration systems can help minimize contamination and extend the lifespan of molecular sieves.
-
Physical Wear:
- Mechanical stress from handling, vibration, or pressure changes can cause physical wear and tear on molecular sieves.
- Over time, this can lead to the breakdown of the sieve particles, reducing their adsorption efficiency.
- Using high-quality molecular sieves and proper handling techniques can mitigate physical wear.
-
Expected Lifespan:
- Under optimal conditions, molecular sieves can last for several years, often ranging from 2 to 5 years or more.
- However, in harsh environments or with improper maintenance, their lifespan may be significantly shorter.
- Regular monitoring of adsorption performance and timely regeneration are essential to maximize their lifespan.
-
Signs of Degradation:
- Reduced adsorption capacity, increased pressure drop across the sieve bed, and changes in the color or texture of the sieves are indicators of degradation.
- When these signs are observed, it may be time to replace or regenerate the molecular sieves.
-
Cost Considerations:
- While molecular sieves are a cost-effective solution for many applications, their replacement and regeneration costs should be factored into the overall budget.
- Investing in high-quality sieves and proper maintenance can reduce long-term costs by extending their lifespan.
By understanding these key factors, equipment and consumable purchasers can make informed decisions about the selection, maintenance, and replacement of molecular sieves, ensuring optimal performance and cost-effectiveness.
Summary Table:
Factor | Impact on Lifespan |
---|---|
Type of Molecular Sieve | Different types (e.g., 3A, 4A, 13X) have varying lifespans due to pore size and composition. |
Operating Conditions | High humidity, temperature, and chemical exposure accelerate degradation. |
Regeneration Process | Proper heating and duration are critical; improper regeneration reduces lifespan. |
Contamination | Oils, hydrocarbons, and heavy metals clog pores, reducing adsorption capacity. |
Physical Wear | Mechanical stress from handling or pressure changes causes wear and tear. |
Expected Lifespan | 2-5 years under optimal conditions; shorter in harsh environments. |
Signs of Degradation | Reduced adsorption, increased pressure drop, or changes in color/texture. |
Cost Considerations | High-quality sieves and maintenance reduce long-term replacement costs. |
Maximize the lifespan of your molecular sieves—contact our experts today for tailored advice!