The lifespan of a heating element in a furnace depends on several factors, including watt density, operating conditions, maintenance, and the type of furnace. While there is no fixed lifespan, heating elements can last for years if operated under optimal conditions. Lower watt density, proper installation, and regular maintenance can extend their life. However, elements may fail prematurely due to factors like rapid heating/cooling cycles, reducing atmospheres, or improper sizing. Manufacturers only warranty against defects, as operational variables significantly impact longevity. On average, a well-maintained furnace lasts 15–20 years, but heating elements may need replacement during this period, depending on usage and conditions.
Key Points Explained:
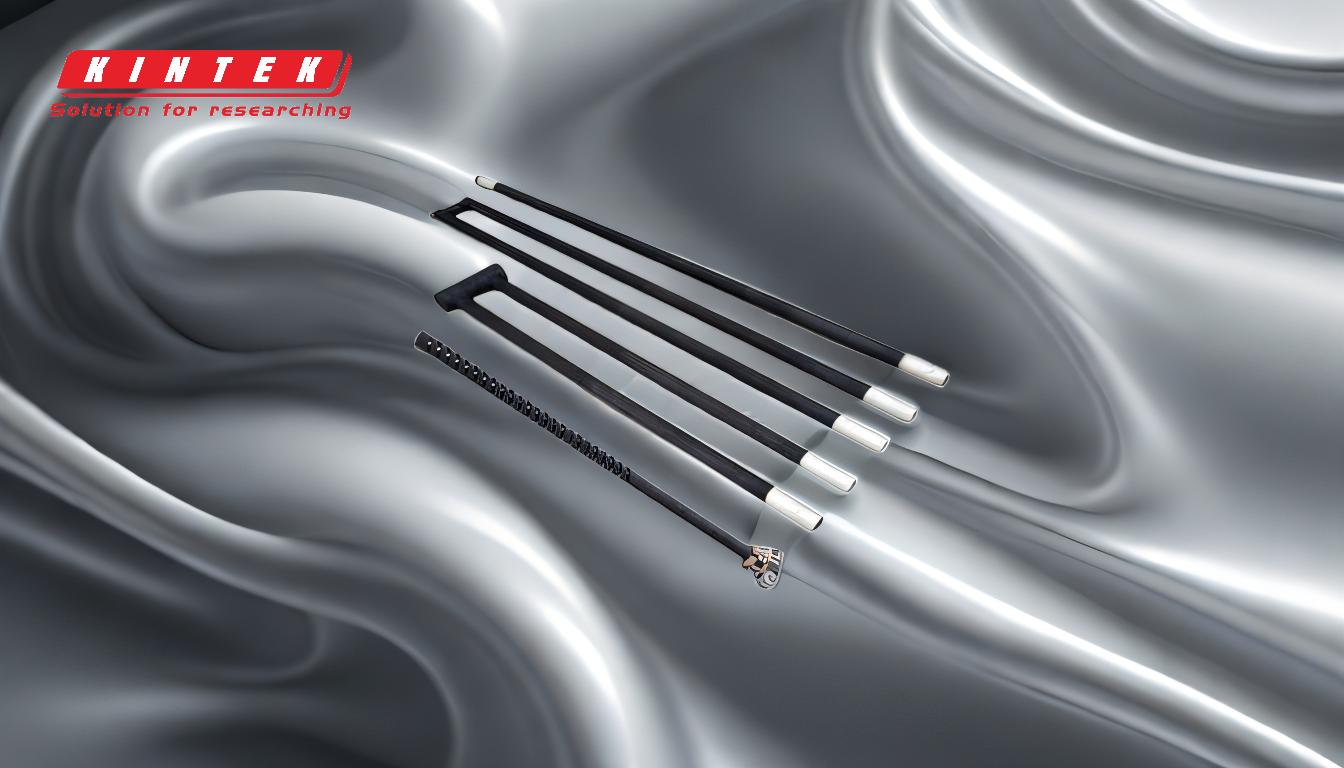
-
Factors Affecting Heating Element Lifespan:
- Watt Density: Lower watt density reduces stress on heating elements, extending their life. This can be achieved by using more elements operating at lower watt density, though it increases space and cost requirements.
- Operating Conditions: Rapid heating and cooling cycles, reducing atmospheres, and high working temperatures can shorten element life.
- Maintenance: Proper installation, sizing, and regular maintenance are critical for maximizing element lifespan.
-
Replacement of Heating Elements:
- Heating elements are replaced only when they fail, and they can be replaced individually. This means that only the failed elements in a series need replacement, not the entire set.
- This modular approach reduces downtime and maintenance costs.
-
Manufacturer Warranties:
- Manufacturers typically warrant heating elements only against manufacturing defects. They do not cover failures caused by operational factors such as improper use, reducing atmospheres, or rapid temperature changes.
-
Types of Heating Elements and Their Lifespan:
- Ferrochromium-Aluminum Wire Elements: Suitable for temperatures up to 1200°C, these elements are durable but may degrade faster under extreme conditions.
- Silicon Carbide Bar Elements: Can withstand temperatures up to 1400°C, making them ideal for high-temperature applications. However, their lifespan depends on operating conditions and maintenance.
-
Furnace Atmosphere and Element Selection:
- The choice of heating element is influenced by the furnace atmosphere (e.g., endo gas or low-pressure carburizing) and the availability of natural gas. The atmosphere affects which element design provides the most reliable performance.
-
Average Furnace Lifespan:
- A well-maintained furnace typically lasts 15–20 years. However, heating elements may need replacement during this period, depending on usage, operating conditions, and maintenance practices.
-
Cost-Benefit Analysis:
- Extending heating element life through lower watt density or higher-quality materials may involve higher upfront costs. These costs must be weighed against the expected lifespan extension and reduced downtime.
Summary Table:
Factor | Impact on Lifespan |
---|---|
Watt Density | Lower watt density extends lifespan but increases space and cost requirements. |
Operating Conditions | Rapid heating/cooling cycles and reducing atmospheres shorten lifespan. |
Maintenance | Proper installation, sizing, and regular maintenance maximize lifespan. |
Element Type | Ferrochromium-Aluminum (up to 1200°C) and Silicon Carbide (up to 1400°C) vary in durability. |
Furnace Atmosphere | Atmosphere type (e.g., endo gas) influences element selection and performance. |
Average Furnace Life | Well-maintained furnaces last 15–20 years, but heating elements may need replacement. |
Maximize your furnace's efficiency—contact our experts today for tailored advice!