The duration of a vacuum heat treatment cycle can vary significantly depending on factors such as the material being treated, the desired properties, and the specific process parameters. Typically, the cycle time ranges from three to 24 hours, but it can extend longer for more complex treatments. Vacuum heat treatment is advantageous because it removes air from the chamber, allowing for precise control over the process and achieving specific surface finishes or material properties.
Key Points Explained:
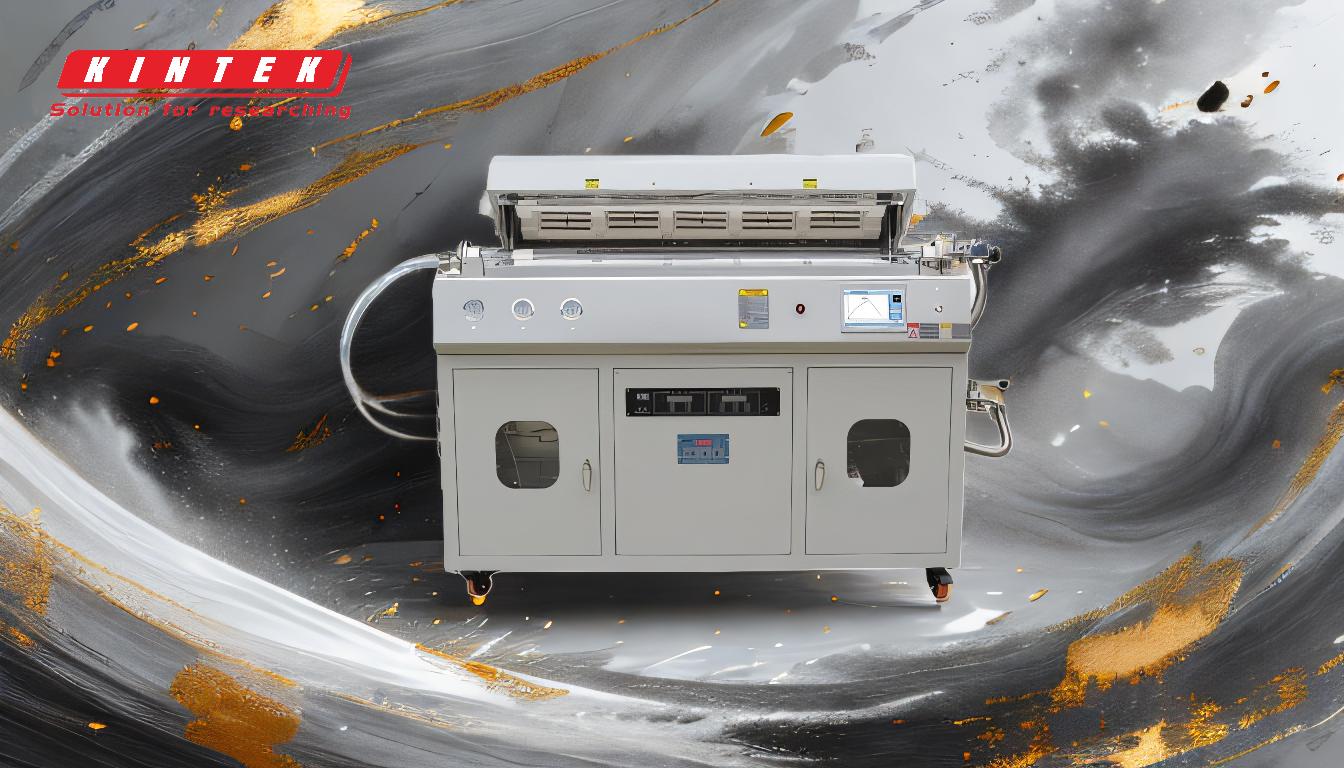
-
Typical Duration of Vacuum Heat Treatment Cycles:
- The cycle time for vacuum heat treatment generally ranges from three to 24 hours. This wide range is due to the varying requirements of different materials and the desired outcomes of the treatment. For instance, simpler processes like annealing may take less time, while more complex treatments like carburizing or nitriding can extend beyond 24 hours.
-
Factors Influencing Cycle Time:
- Material Type: Different materials require different heating and cooling rates. For example, high-alloy steels may need longer cycles to ensure uniform heating and proper microstructure development.
- Desired Properties: The specific mechanical or surface properties being targeted, such as hardness, toughness, or corrosion resistance, can influence the duration. Processes like tempering or stress relieving may require extended hold times at specific temperatures.
- Process Complexity: Advanced treatments, such as vacuum carburizing or nitriding, involve multiple steps (e.g., heating, soaking, diffusion, and cooling), which can significantly increase the total cycle time.
- Part Geometry and Size: Larger or more complex parts may require longer cycles to ensure uniform heat distribution and avoid thermal stresses.
-
Advantages of Vacuum Heat Treatment:
- Controlled Atmosphere: The vacuum environment eliminates oxidation and decarburization, ensuring clean and precise surface finishes. This is particularly beneficial for materials sensitive to atmospheric contamination.
- Enhanced Properties: Vacuum heat treatment can improve mechanical properties such as hardness, wear resistance, and fatigue strength, making it ideal for high-performance applications.
- Environmentally Friendly: Unlike traditional heat treatment methods that use gaseous atmospheres, vacuum heat treatment produces no harmful emissions, making it a more sustainable option.
-
Applications Requiring Extended Cycle Times:
- Aerospace and Automotive Industries: Components like turbine blades, gears, and engine parts often undergo vacuum heat treatment to achieve superior strength and durability. These applications may require longer cycles to meet stringent quality standards.
- Tool and Die Manufacturing: Tools and dies used in high-stress environments benefit from vacuum heat treatment to enhance their wear resistance and lifespan, often necessitating extended cycle times.
-
Optimizing Cycle Time:
- Process Design: Careful planning of heating rates, soak times, and cooling rates can help optimize the cycle time without compromising the quality of the treatment.
- Equipment Capabilities: Modern vacuum furnaces with advanced controls and automation can reduce cycle times by ensuring precise temperature management and efficient heat transfer.
In summary, the duration of a vacuum heat treatment cycle is highly variable and depends on multiple factors, including material type, desired properties, and process complexity. While typical cycles last between three to 24 hours, more intricate treatments can extend beyond this range. The use of vacuum heat treatment offers significant advantages in terms of control, surface finish, and environmental impact, making it a preferred choice for high-performance applications.
Summary Table:
Aspect | Details |
---|---|
Typical Cycle Duration | 3 to 24 hours, with longer times for complex treatments like carburizing. |
Factors Influencing Time | Material type, desired properties, process complexity, part size & geometry. |
Advantages | Controlled atmosphere, enhanced properties, environmentally friendly. |
Applications | Aerospace, automotive, tool & die manufacturing requiring extended cycles. |
Optimization Tips | Process design, modern equipment with advanced controls & automation. |
Need help optimizing your vacuum heat treatment process? Contact our experts today for tailored solutions!