The settling time for PVD (Posterior Vitreous Detachment) floaters, often referred to as "floaters," can vary from person to person. Generally, it takes about 3 to 6 months for these floaters to improve. However, if they persist beyond this period and significantly affect daily activities such as reading or driving, surgical intervention may be considered. This timeline is based on the natural healing process of the eye and the gradual adaptation of the brain to ignore these visual disturbances.
Key Points Explained:
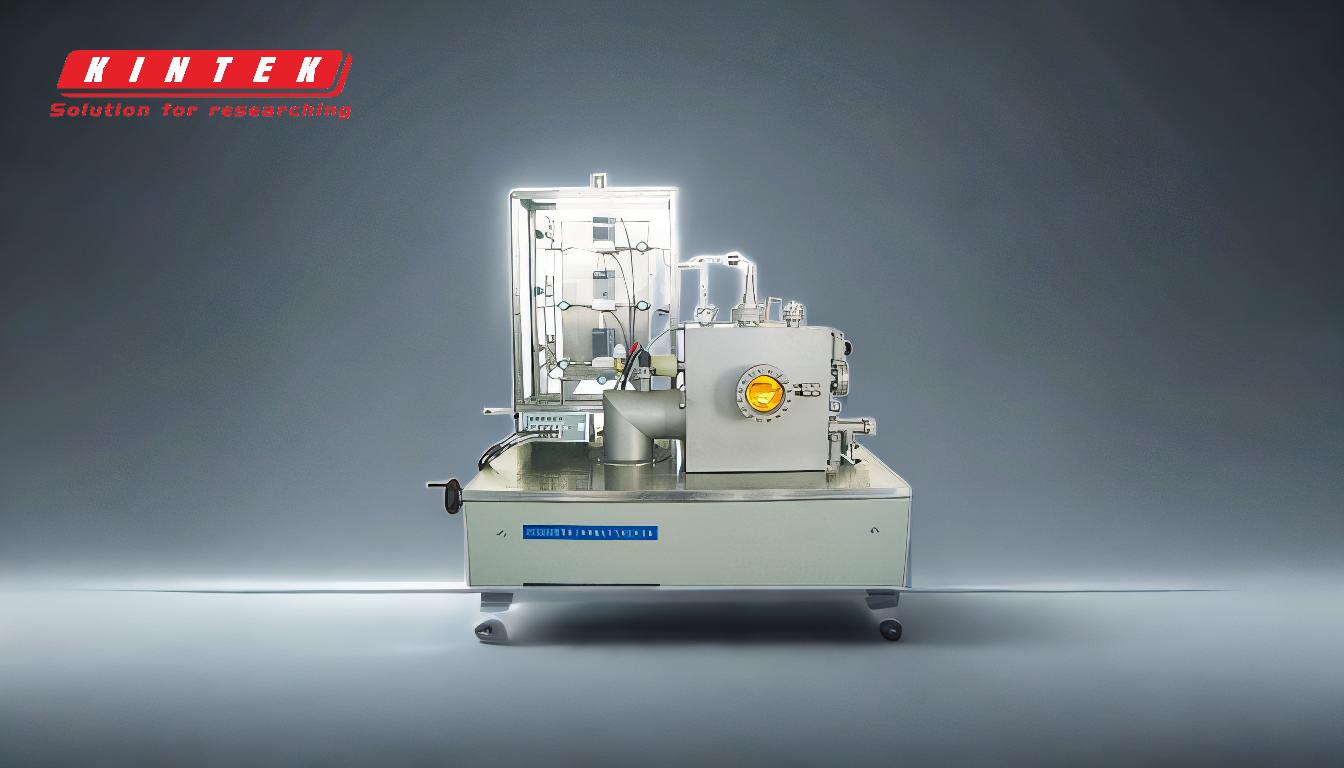
-
Understanding PVD Floaters:
- PVD occurs when the vitreous gel inside the eye separates from the retina. This process can cause floaters, which are small clumps of gel or cells inside the vitreous that cast shadows on the retina.
- Floaters are often perceived as spots, threads, or cobweb-like structures that drift across the field of vision.
-
Typical Improvement Timeline:
- 3-6 Months: Most individuals experience a noticeable improvement in floaters within this period. The brain tends to adapt and ignore these visual disturbances over time.
- Gradual Adaptation: The improvement is not immediate but occurs gradually as the brain learns to filter out the floaters.
-
Factors Influencing the Timeline:
- Severity of PVD: The extent of the vitreous detachment can influence how long it takes for floaters to settle.
- Individual Differences: Each person's experience with PVD and floaters can vary based on factors such as age, overall eye health, and the presence of other eye conditions.
-
When to Seek Medical Advice:
- Persistent Floaters: If floaters persist beyond 6 months and continue to impact daily activities, it is advisable to consult an ophthalmologist.
- Sudden Increase in Floaters: A sudden increase in the number of floaters, especially if accompanied by flashes of light or a loss of peripheral vision, could indicate a retinal tear or detachment and requires immediate medical attention.
-
Surgical Options:
- Vitrectomy: In cases where floaters are severely impairing vision and quality of life, a surgical procedure called vitrectomy may be considered. This involves removing the vitreous gel and replacing it with a saline solution.
- Risks and Considerations: While vitrectomy can be effective, it carries risks such as cataract formation, retinal detachment, and infection. Therefore, it is typically considered only when floaters are significantly debilitating.
-
Microwave Plasma Chemical Vapor Deposition:
- Although not directly related to PVD floaters, microwave plasma chemical vapor deposition is a technology used in various industrial applications, including the creation of thin films and coatings. It involves using microwave energy to generate plasma, which then facilitates the deposition of materials onto a substrate.
In summary, the settling time for PVD floaters is generally around 3 to 6 months, with most individuals experiencing gradual improvement. However, persistent or severe cases may require medical intervention, including surgical options. Understanding the factors that influence this timeline and knowing when to seek professional advice are crucial for managing PVD floaters effectively.
Summary Table:
Key Aspect | Details |
---|---|
Typical Improvement Time | 3-6 months for most individuals |
Gradual Adaptation | The brain learns to ignore floaters over time |
Factors Influencing Timeline | Severity of PVD, age, eye health, and other conditions |
When to Seek Medical Advice | Persistent floaters beyond 6 months or sudden increase in floaters |
Surgical Options | Vitrectomy for severe cases, with risks like cataracts or retinal detachment |
Concerned about persistent floaters? Consult an ophthalmologist today for expert advice!