PVD (Physical Vapor Deposition) coatings are renowned for their durability and resistance to wear, corrosion, and scratching. The lifespan of a PVD coating varies depending on usage conditions, maintenance, and environmental factors. Under standard daily wear, PVD coatings typically last between 1 to 3 years before showing signs of wear. With gentle use and proper care, such as minimizing exposure to harsh conditions and maintaining the coating, it can last upwards of 5 years. The durability of PVD coatings is influenced by factors like the type of substrate, coating thickness, bond strength, and exposure to high temperatures and wear. These coatings are exceptionally thin (0.5 to 5 microns) and highly resistant to corrosion and oxidation, making them suitable for demanding applications.
Key Points Explained:
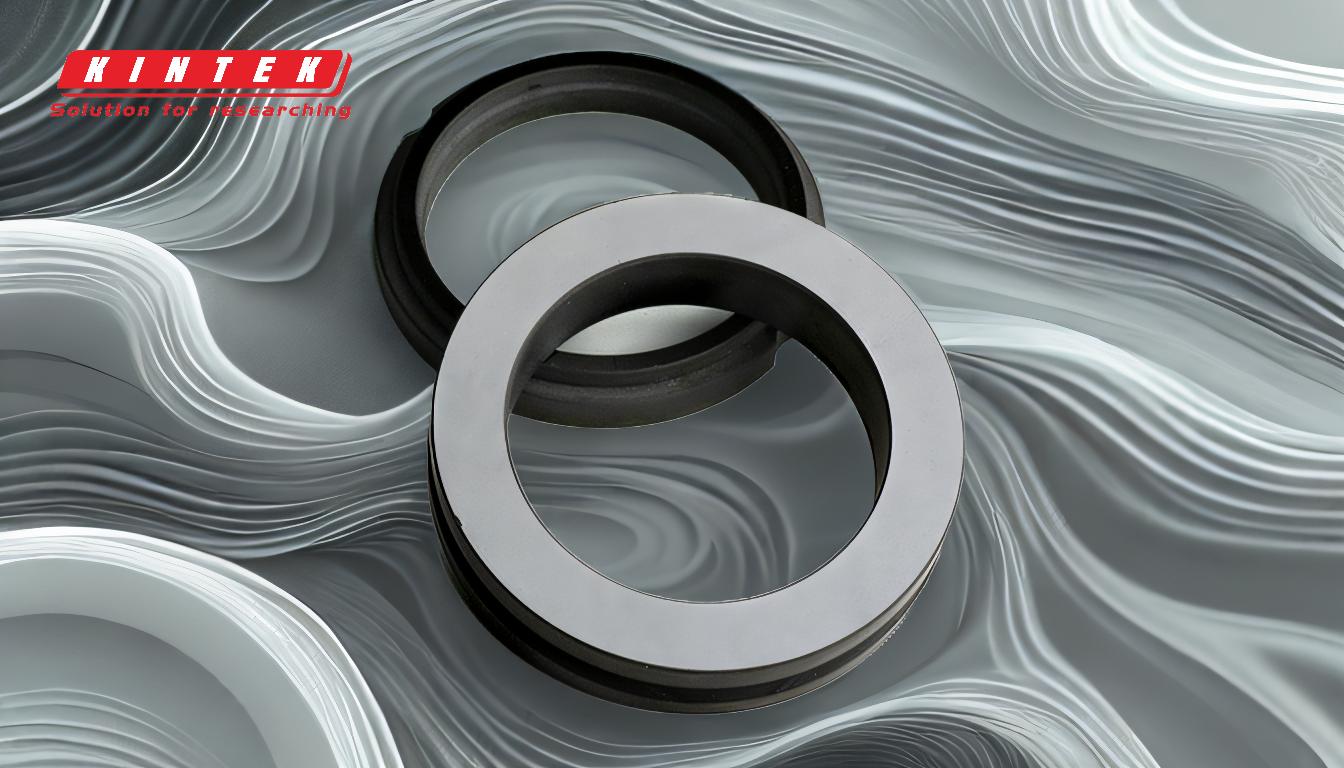
-
Lifespan of PVD Coatings:
- Standard Use: Under typical daily wear, PVD coatings last between 1 to 3 years before showing signs of wear. This is due to the gradual exposure to environmental factors and mechanical stress.
- Gentle Use: With careful maintenance and minimal exposure to harsh conditions, PVD coatings can last upwards of 5 years. Proper care significantly extends their lifespan.
-
Factors Influencing Durability:
- Substrate Material: The type of material the coating is applied to plays a crucial role. For example, TiN coatings on Ti-6Al-4V alloy increase fatigue limits and endurance.
- Coating Thickness: PVD coatings are very thin, ranging from 0.5 to 5 microns. Despite their thinness, they are highly durable due to their hardness and strong bond with the substrate.
- Bond Strength: The vacuum environment during the PVD process ensures a strong bond between the coating and the substrate, enhancing durability.
- Environmental Exposure: Exposure to high temperatures, wear, and harsh conditions can accelerate wear. PVD coatings are resistant to corrosion and oxidation, but extreme conditions can still affect their lifespan.
-
Resistance Properties:
- Corrosion and Oxidation Resistance: PVD coatings are highly resistant to corrosion and oxidation due to the vacuum application process, which prevents contamination and degradation.
- Scratch Resistance: The hardness of PVD coatings makes them highly resistant to scratching, contributing to their longevity.
- Temperature Tolerance: PVD coatings have robust temperature tolerance, making them suitable for high-temperature applications.
-
Applications and Suitability:
- Demanding Applications: Due to their durability, PVD coatings are ideal for applications where resistance to wear, corrosion, and high temperatures is critical.
- Replication of Original Finish: PVD coatings can replicate the original finish of materials with minimal effort, making them versatile for various aesthetic and functional applications.
-
Maintenance and Care:
- Proper Maintenance: Regular cleaning and avoiding exposure to harsh chemicals can help maintain the integrity of PVD coatings.
- Avoiding Mechanical Stress: Minimizing mechanical stress and impact can extend the lifespan of the coating.
In summary, the lifespan of PVD coatings depends on usage conditions and maintenance. With proper care, PVD coatings can provide long-lasting durability and resistance to wear, making them a superior choice for various applications.
Summary Table:
Aspect | Details |
---|---|
Lifespan (Standard Use) | 1 to 3 years under typical daily wear |
Lifespan (Gentle Use) | Upwards of 5 years with proper care and minimal harsh conditions |
Key Influencing Factors | Substrate material, coating thickness, bond strength, environmental exposure |
Resistance Properties | High resistance to corrosion, oxidation, scratching, and high temperatures |
Applications | Ideal for demanding applications requiring durability and resistance |
Maintenance Tips | Regular cleaning, avoiding harsh chemicals, and minimizing mechanical stress |
Maximize the lifespan of your PVD coatings—contact our experts today for tailored advice!