The longevity of PVD (Physical Vapor Deposition) coating depends on several factors, including the substrate material, the type of coating applied, the thickness of the coating, and the environmental conditions it is exposed to. PVD coatings are known for their durability, resistance to wear, corrosion, and oxidation, making them suitable for a wide range of applications. Typically, PVD coatings can last for many years, especially when applied to high-quality substrates and used in environments that do not excessively stress the coating. The thin nature of the coating (ranging from 0.5 to 5 microns) does not compromise its durability, as it is designed to enhance the substrate's properties on a molecular level.
Key Points Explained:
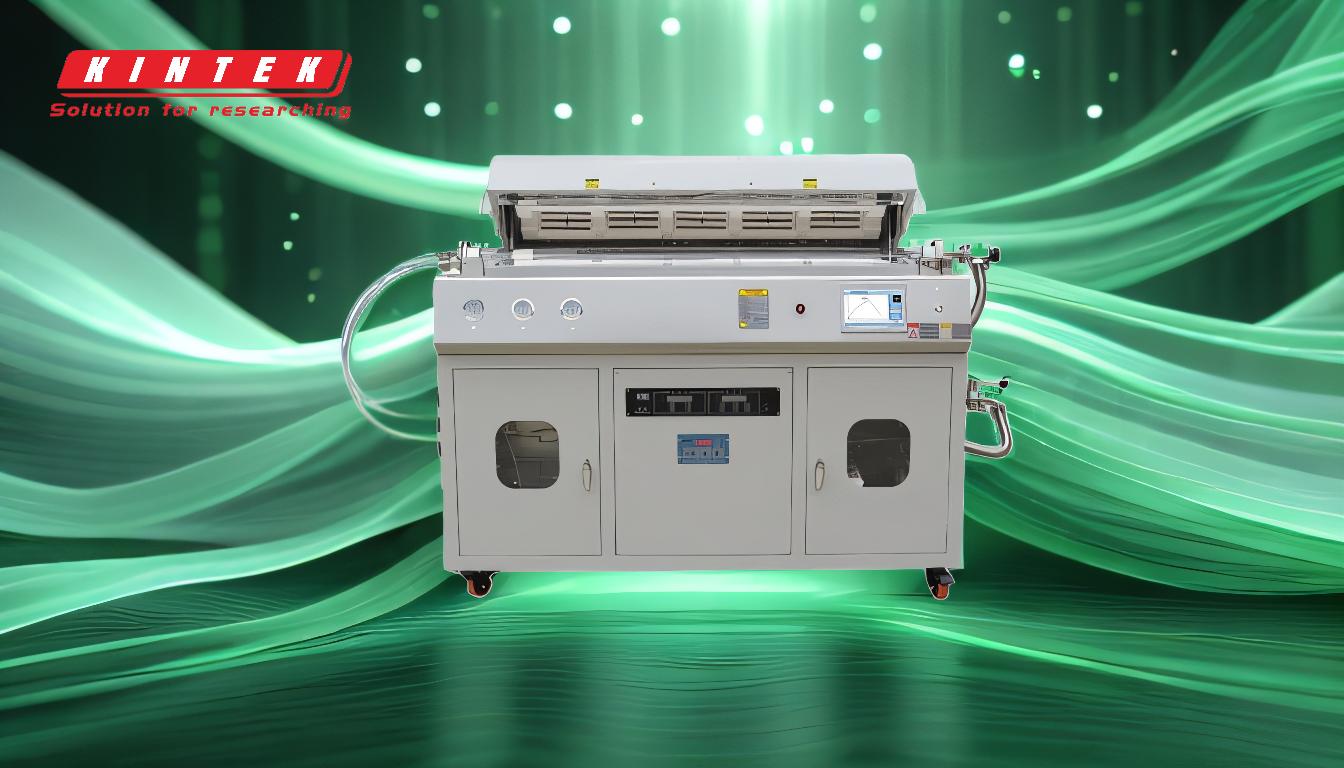
-
Durability and Wear Resistance:
- PVD coatings are highly durable due to their enhanced hardness and wear resistance. The coating process increases the hardness of the substrate material, which helps in reducing friction and wear over time. This makes PVD coatings ideal for applications where the material is subject to constant mechanical stress, such as cutting tools, automotive components, and industrial machinery.
-
Corrosion and Oxidation Resistance:
- One of the significant advantages of PVD coatings is their resistance to corrosion and oxidation. This property ensures that the coated materials can withstand harsh environments, including exposure to moisture, chemicals, and high temperatures. As a result, PVD-coated components are less likely to degrade over time, contributing to their long lifespan.
-
Coating Thickness:
- The thickness of the PVD coating, typically ranging from 0.5 to 5 microns, plays a crucial role in its longevity. While the coating is thin, it is dense and adheres strongly to the substrate, providing a protective barrier that enhances the material's properties. The thinness of the coating also helps in maintaining the sharpness of tools and reducing cutting forces, which can further extend the life of the coated item.
-
Substrate Material:
- The underlying substrate material significantly influences the performance and lifespan of the PVD coating. For example, when applied to high-strength alloys like Ti-6Al-4V, PVD coatings such as TiN (Titanium Nitride) can increase the fatigue limit and endurance of the material. The compatibility between the coating and the substrate ensures that the coating remains intact and functional over an extended period.
-
Environmental Factors:
- The environment in which the PVD-coated material is used can impact its lifespan. In conditions where the coating is exposed to extreme temperatures, abrasive materials, or corrosive substances, the coating may degrade faster. However, in typical use cases, PVD coatings are designed to withstand such challenges, ensuring a long service life.
-
Application-Specific Longevity:
- The lifespan of PVD coatings can vary depending on the specific application. For instance, in decorative applications like jewelry or architectural components, the coating may last indefinitely with proper care. In contrast, in high-wear applications like cutting tools, the coating may need to be reapplied after several years of use, depending on the intensity of the application.
In summary, PVD coatings are designed to last for many years, thanks to their enhanced hardness, wear resistance, and corrosion resistance. The specific lifespan will depend on factors such as the substrate material, coating thickness, and environmental conditions. With proper application and maintenance, PVD coatings can provide long-lasting protection and performance for a wide range of materials and applications.
Summary Table:
Factor | Impact on Longevity |
---|---|
Substrate Material | High-quality substrates enhance coating durability and lifespan. |
Coating Thickness | Thin coatings (0.5–5 microns) provide strong adhesion and durability. |
Environmental Exposure | Harsh conditions (e.g., extreme temperatures, chemicals) may reduce lifespan. |
Application Type | Decorative coatings last indefinitely; high-wear applications may require reapplication. |
Wear Resistance | High hardness and wear resistance ensure long-term performance. |
Corrosion Resistance | Protects against oxidation and corrosion, extending lifespan. |
Ensure your materials last longer with PVD coatings—contact us today for expert advice!