Compression molding is a manufacturing process that involves shaping raw materials like rubber, plastic, or metal into desired forms using heat and pressure. The process begins by placing a pre-measured charge of material into the mold cavity. The mold is then closed, and pressure is applied to compress the material, allowing it to flow and fill the cavity. Heat is often used to soften the material, making it easier to mold and speeding up production. Excess material, known as mold flash, is expelled through special grooves. This method is widely used in industries like automotive manufacturing for creating interior components such as sun visors and gear knobs. However, challenges such as accurately measuring the material and ensuring proper placement must be addressed to avoid defects like flow lines, blisters, or unfilled parts.
Key Points Explained:
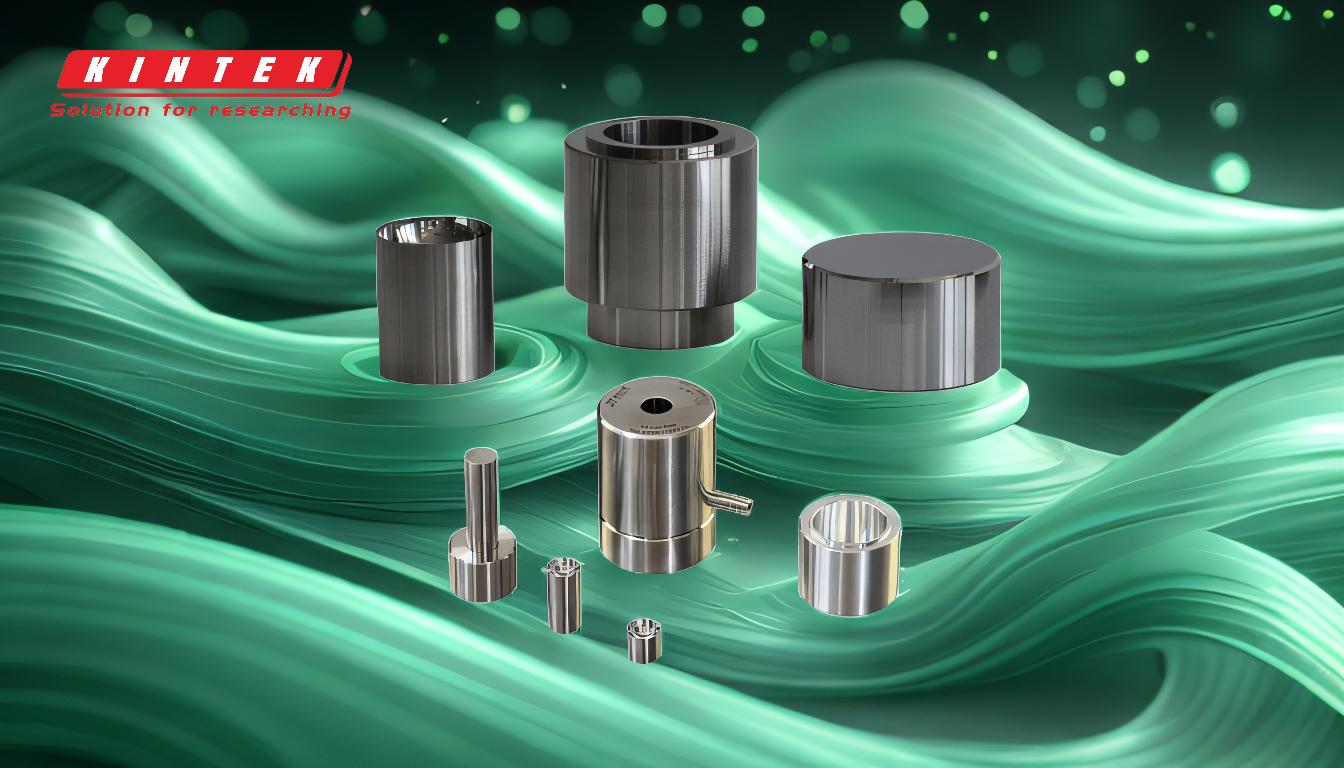
-
Preparation of the Mold and Material:
- Material Selection: Choose the appropriate raw material, such as rubber, plastic, or metal, depending on the desired product.
- Mold Design: Ensure the mold is designed with the correct cavity shape and includes grooves for excess material (mold flash) to escape.
- Material Measurement: Accurately cut or weigh the material to ensure the right amount is placed in each cavity. Too little material can lead to defects, while too much can cause excessive flash.
-
Inserting the Charge:
- Placement: Place the pre-measured charge of material in the center of the bottom mold cavity. Proper placement is crucial to ensure even distribution and avoid defects.
- Material Shape: Use well-shaped, un-branched rubber stock or other materials to facilitate smooth flow within the mold.
-
Closing the Mold:
- Application of Pressure: Close the top mold and apply pressure using a hydraulic press or similar equipment. The pressure forces the material to flow and fill the cavity.
- Temperature Control: Maintain the mold at a fixed temperature to soften the material, making it easier to mold and speeding up the production process.
-
Forming the Part:
- Material Flow: Under pressure and heat, the material flows to fill the mold cavity completely. Excess material is expelled through special grooves as mold flash.
- Curing Time: Allow sufficient time for the material to cure and solidify within the mold. The curing time depends on the material type and the desired properties of the final product.
-
Removing the Part:
- Opening the Mold: Once the material has cured, open the mold carefully to avoid damaging the newly formed part.
- Trimming Flash: Remove any excess material (mold flash) that has flowed out of the grooves. This step may require additional trimming or finishing processes.
-
Challenges and Solutions:
- Material Measurement: Accurate measurement is critical. Use precise weighing or cutting tools to ensure the correct amount of material is used.
- Defect Prevention: Proper placement and adequate pressure help prevent defects like flow lines, blisters, or unfilled parts. Excessive material can lead to heavy flash, which is difficult to remove.
- Process Optimization: Regularly monitor and adjust the pressure, temperature, and curing time to optimize the process and improve product quality.
-
Applications:
- Automotive Industry: Compression molding is ideal for manufacturing interior components such as sun visors, gear knobs, and trim covers. The process is efficient and cost-effective, reducing material waste and labor costs.
- Other Industries: This method is also used in various other industries to produce a wide range of products, from simple plastic parts to complex rubber components.
By following these steps and addressing the challenges, compression molding can be a highly effective method for producing high-quality parts with minimal waste.
Summary Table:
Key Step | Description |
---|---|
Material Selection | Choose rubber, plastic, or metal based on product requirements. |
Mold Design | Design molds with proper cavities and grooves for excess material (mold flash). |
Material Measurement | Accurately weigh or cut material to avoid defects or excessive flash. |
Inserting the Charge | Place material in the center of the mold for even distribution. |
Closing the Mold | Apply pressure and heat to soften and shape the material. |
Forming the Part | Allow material to flow and cure within the mold. |
Removing the Part | Open the mold and trim excess flash for a clean finish. |
Applications | Widely used in automotive and industrial manufacturing. |
Ready to optimize your manufacturing process with compression molding? Contact our experts today to get started!