Cooling a muffle furnace properly is critical to ensure its longevity, safety, and performance. The process involves allowing the furnace to cool naturally by cutting off the power supply and avoiding sudden temperature changes. Rapid cooling, such as opening the furnace door immediately after use, can lead to thermal shock, cracking, or damage to the furnace's internal components, particularly the refractories. The furnace door should only be opened when the temperature drops below 200 °C to prevent safety hazards and structural damage. Following the specified cooling rate and prioritizing gradual temperature reduction are essential steps in maintaining the furnace's integrity.
Key Points Explained:
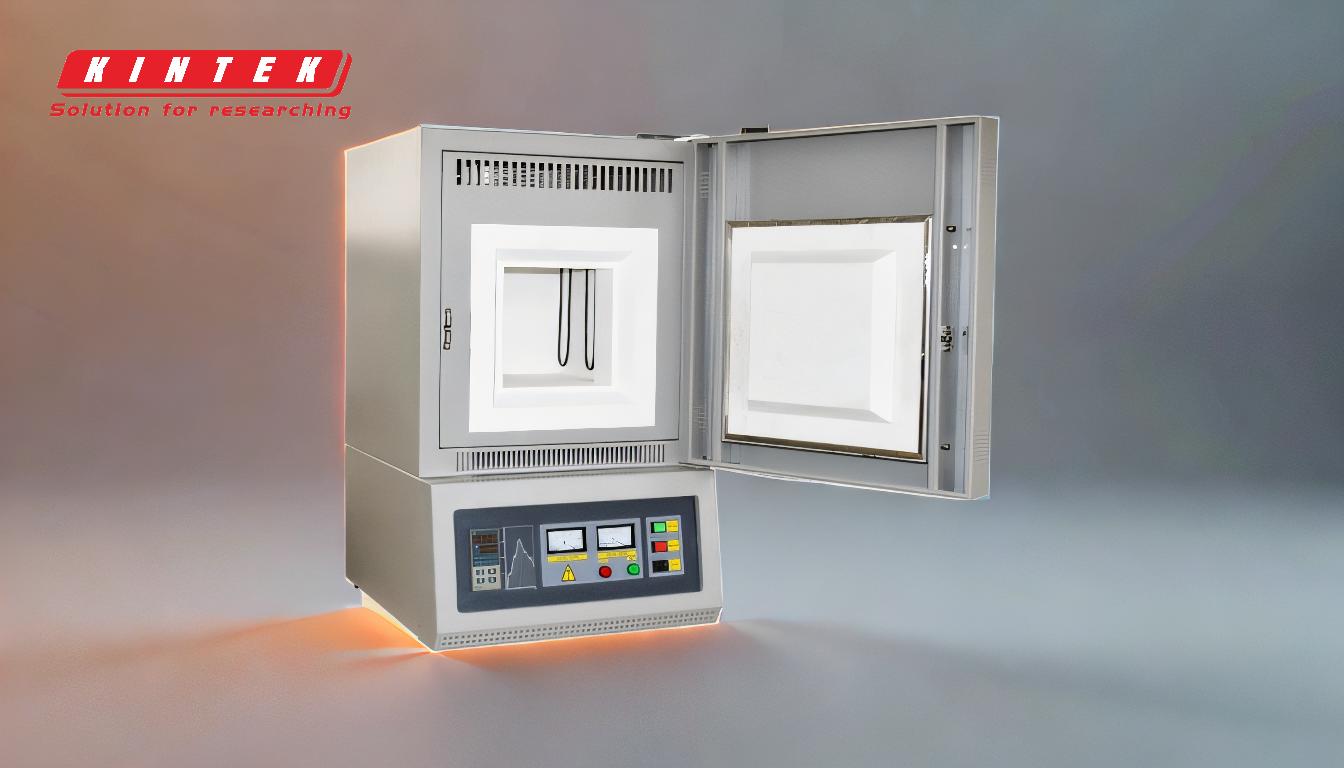
-
Cut Off the Power Supply:
- After using the muffle furnace, the first step is to turn off the power supply. This stops the heating process and allows the furnace to begin cooling naturally.
- Continuing to supply power after use can lead to unnecessary energy consumption and potential overheating, which may damage the furnace.
-
Allow Natural Cooling:
- Natural cooling is the safest method to bring the furnace temperature down. This process avoids rapid temperature changes that can cause thermal stress.
- Thermal stress occurs when different parts of the furnace cool at different rates, leading to cracks or damage in the refractories or heating elements.
-
Avoid Opening the Furnace Door Immediately:
- Opening the furnace door immediately after use exposes the hot interior to cooler ambient air, causing a sharp temperature decline. This rapid cooling can lead to thermal shock, which may crack the furnace lining or damage other components.
- The furnace door should remain closed until the internal temperature drops below 200 °C. This ensures a gradual and safe cooling process.
-
Follow the Specified Cooling Rate:
- Manufacturers often provide a recommended cooling rate for their muffle furnaces. Adhering to this rate is crucial to prevent damage and maintain the furnace's performance.
- Rapid cooling, even if the door remains closed, can still cause harm if the temperature drops too quickly. Gradual cooling ensures uniformity and reduces the risk of thermal stress.
-
Prioritize Safety:
- Safety is paramount when handling high-temperature equipment like muffle furnaces. Opening the door too soon can expose users to extreme heat, posing burn risks.
- Additionally, sudden temperature changes can release trapped gases or cause structural failures, leading to potential hazards.
-
Prevent Damage to Refractories:
- Refractories are heat-resistant materials lining the furnace chamber. They are designed to withstand high temperatures but are vulnerable to rapid cooling.
- Gradual cooling helps preserve the integrity of these materials, ensuring the furnace remains functional and efficient over time.
By following these steps, users can safely and effectively cool their muffle furnaces, extending their lifespan and maintaining optimal performance.
Summary Table:
Step | Description |
---|---|
Cut Off the Power Supply | Turn off the power to allow natural cooling and prevent overheating. |
Allow Natural Cooling | Avoid rapid temperature changes to prevent thermal stress and damage. |
Avoid Opening Door Immediately | Keep the door closed until the temperature drops below 200 °C to prevent thermal shock. |
Follow Specified Cooling Rate | Adhere to the manufacturer's recommended cooling rate for uniformity. |
Prioritize Safety | Prevent burn risks and structural failures by avoiding sudden temperature changes. |
Prevent Damage to Refractories | Gradual cooling preserves heat-resistant materials, ensuring long-term efficiency. |
Need expert advice on maintaining your muffle furnace? Contact us today for personalized guidance!