To make compound rubber, the process involves mixing raw rubber with various ingredients to achieve desired properties. The key steps include plasticizing the rubber, adding antioxidants, vulcanizers, fillers, softeners, and finally a vulcanization accelerator. These ingredients are sequentially introduced during rolling or mixing operations. The compounded rubber is then processed further through methods like extrusion, calendering, or vulcanization to create finished products. This process ensures the rubber acquires specific characteristics such as durability, elasticity, and resistance to environmental factors.
Key Points Explained:
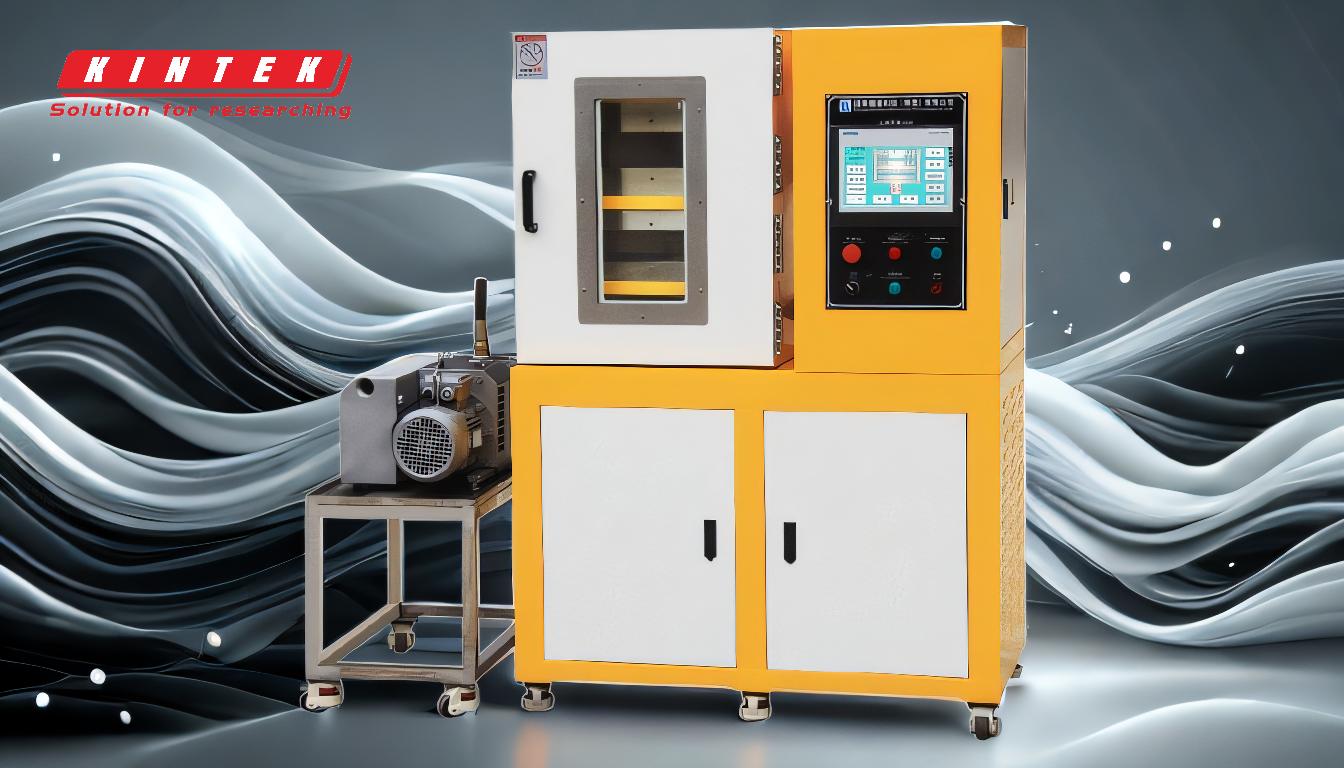
-
Plasticizing the Rubber
- The first step in making compound rubber is plasticizing the raw rubber. This involves softening the rubber to make it more workable and easier to mix with other ingredients. Plasticizing is typically done using mechanical methods like rolling or mixing in a Banbury mixer.
-
Adding Antioxidants
- Antioxidants are added to the rubber compound to prevent degradation caused by oxidation. These chemicals protect the rubber from environmental factors like heat, light, and ozone, which can cause cracking or loss of elasticity over time.
-
Incorporating Vulcanizers
- Vulcanizers, such as sulfur, are introduced to create cross-links between the rubber polymer chains. This process, known as vulcanization, enhances the rubber's strength, elasticity, and resistance to wear and tear. Vulcanization is a critical step in transforming raw rubber into a durable material.
-
Introducing Fillers and Softeners
- Fillers like carbon black or silica are added to improve the rubber's mechanical properties, such as tensile strength and abrasion resistance. Softeners, such as oils or resins, are included to enhance flexibility and processability.
-
Adding Vulcanization Accelerators
- Vulcanization accelerators are added last to speed up the vulcanization process. These chemicals reduce the time and temperature required for vulcanization, ensuring efficient production while maintaining the desired properties of the rubber.
-
Further Processing
- Once the compound rubber is prepared, it undergoes additional processes to create finished products. These include:
- Extrusion: Shaping the rubber into continuous profiles or sheets.
- Calendering: Rolling the rubber into thin sheets or coating it onto fabrics.
- Vulcanization: Curing the rubber to finalize its properties through open vulcanization or continuous vulcanization methods.
- Once the compound rubber is prepared, it undergoes additional processes to create finished products. These include:
-
Quality Control and Testing
- Throughout the process, quality control measures are implemented to ensure the compound rubber meets specific standards. This includes testing for properties like hardness, tensile strength, and elongation.
By following these steps, manufacturers can produce compound rubber with tailored properties suitable for a wide range of applications, from automotive tires to industrial seals and consumer products.
Summary Table:
Step | Description |
---|---|
Plasticizing the Rubber | Soften raw rubber using mechanical methods like rolling or mixing. |
Adding Antioxidants | Prevent degradation by protecting rubber from heat, light, and ozone. |
Incorporating Vulcanizers | Enhance strength and elasticity through cross-linking polymer chains. |
Introducing Fillers and Softeners | Improve mechanical properties and flexibility with carbon black, silica, or oils. |
Adding Vulcanization Accelerators | Speed up vulcanization for efficient production. |
Further Processing | Shape rubber via extrusion, calendering, or vulcanization for finished products. |
Quality Control and Testing | Ensure rubber meets standards by testing hardness, tensile strength, and elongation. |
Need high-quality compound rubber for your applications? Contact us today to learn more!