Additive manufacturing (AM), often referred to as 3D printing, is a transformative technology that has gained significant attention across industries. Whether it is cheaper than traditional manufacturing methods depends on several factors, including the complexity of the part, production volume, material costs, and the specific application. While AM can be cost-effective for low-volume, highly complex, or customized parts, it may not always be cheaper for high-volume production or simpler designs. The cost-effectiveness of AM is also influenced by advancements in technology, material availability, and economies of scale. Below, we explore the key factors that determine whether additive manufacturing is cheaper and under what circumstances it can offer cost advantages.
Key Points Explained:
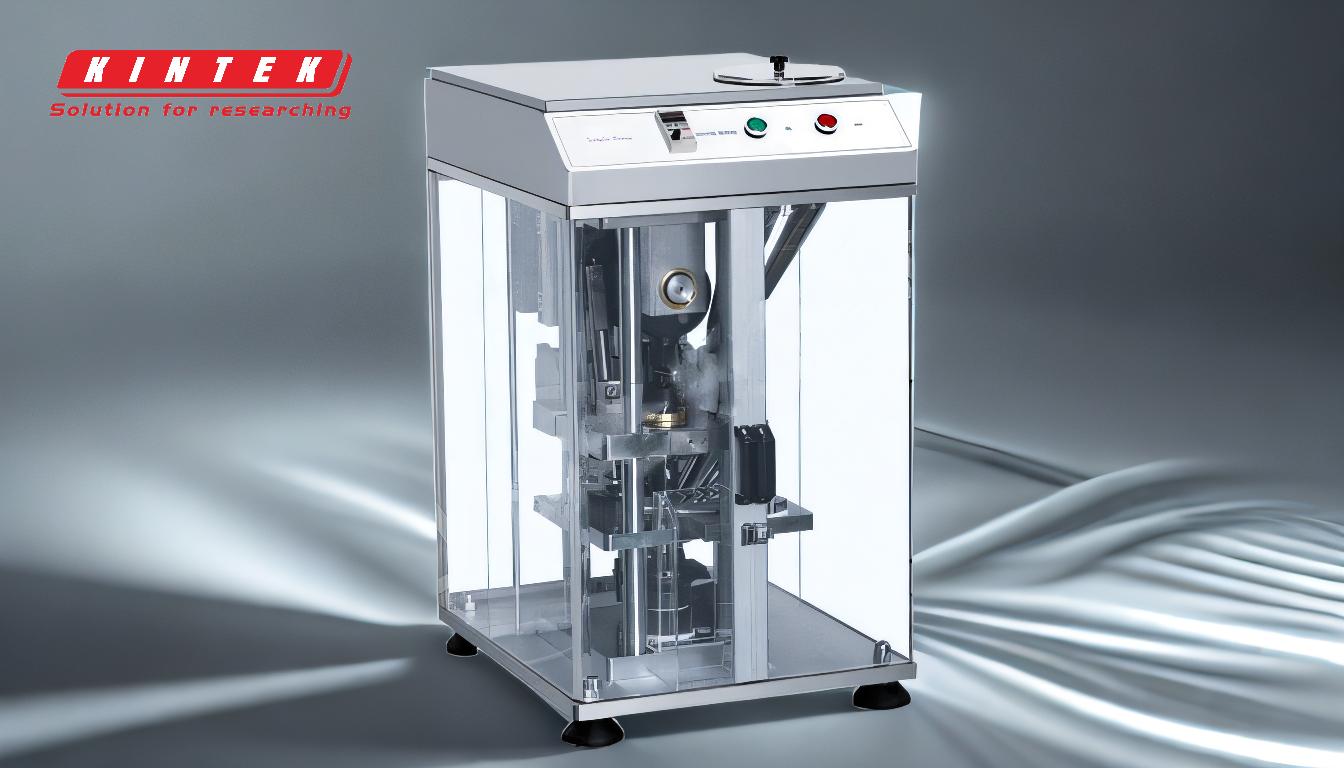
-
Complexity of the Part
- Additive manufacturing excels in producing complex geometries that are difficult or impossible to achieve with traditional methods like machining or injection molding.
- For intricate designs, AM can reduce costs by eliminating the need for multiple manufacturing steps, specialized tooling, or assembly of multiple components.
- Example: Aerospace components with internal lattices or medical implants tailored to patient anatomy are often cheaper to produce with AM due to reduced material waste and labor.
-
Production Volume
- AM is generally more cost-effective for low- to medium-volume production.
- Traditional manufacturing methods like injection molding or casting become more economical at higher volumes due to economies of scale.
- Example: Producing 10 custom prototypes with AM is cheaper than creating molds for injection molding, but producing 10,000 identical parts is typically more cost-effective with traditional methods.
-
Material Costs
- The cost of materials used in additive manufacturing can vary widely. Some AM-specific materials, such as high-performance polymers or metal powders, are more expensive than their traditional counterparts.
- However, AM often uses materials more efficiently, reducing waste compared to subtractive methods like machining.
- Example: Titanium parts made via AM can be cheaper due to reduced material waste, even though titanium powder is costly.
-
Tooling and Setup Costs
- Traditional manufacturing often requires expensive tooling, molds, or dies, which can be a significant upfront cost.
- AM eliminates the need for tooling, making it a cost-effective option for prototyping and small-batch production.
- Example: A company developing a new product can save thousands of dollars by using AM for prototypes instead of investing in molds.
-
Customization and Design Flexibility
- AM allows for easy customization without additional costs, making it ideal for personalized products or medical devices.
- Traditional methods often require retooling or redesign for custom parts, increasing costs.
- Example: Custom orthodontic aligners or hearing aids are cheaper to produce with AM due to the ability to tailor each product to the individual.
-
Post-Processing Requirements
- Some AM processes require significant post-processing, such as support removal, surface finishing, or heat treatment, which can add to the overall cost.
- The need for post-processing varies by technology and material, affecting the cost-effectiveness of AM.
- Example: Metal parts produced via AM often require machining or polishing to meet final specifications, which can offset some of the cost savings.
-
Technological Advancements
- As AM technology advances, costs are decreasing due to improved efficiency, faster printing speeds, and the development of more affordable materials.
- Innovations like multi-material printing and hybrid manufacturing are expanding the cost advantages of AM.
- Example: Newer AM systems can print with multiple materials simultaneously, reducing the need for assembly and lowering costs.
-
Industry-Specific Applications
- The cost-effectiveness of AM varies by industry. Industries like aerospace, healthcare, and automotive are leveraging AM for cost savings in specific applications.
- Example: In aerospace, AM reduces the weight of components, leading to fuel savings that offset the higher production costs.
-
Sustainability and Waste Reduction
- AM is often more sustainable than traditional methods due to reduced material waste and energy consumption.
- While sustainability may not directly reduce costs, it can lead to long-term savings and align with corporate sustainability goals.
- Example: Companies using AM can reduce waste disposal costs and improve their environmental footprint.
-
Economies of Scale and Market Trends
- As the AM industry grows, economies of scale are driving down the costs of machines, materials, and services.
- Increased competition and market adoption are making AM more accessible and affordable for a wider range of applications.
- Example: The cost of desktop 3D printers has dropped significantly, making AM a viable option for small businesses and hobbyists.
In conclusion, whether additive manufacturing is cheaper depends on the specific use case. For complex, low-volume, or customized parts, AM often provides significant cost advantages. However, for high-volume production of simple parts, traditional methods may still be more economical. As technology continues to evolve, the cost-effectiveness of AM is expected to improve, making it an increasingly attractive option across industries.
Summary Table:
Factor | Additive Manufacturing (AM) | Traditional Manufacturing |
---|---|---|
Part Complexity | Cost-effective for highly complex designs, reduces need for tooling and assembly. | Expensive for intricate designs, requires specialized tooling and multiple steps. |
Production Volume | Economical for low- to medium-volume production. | More cost-effective for high-volume production due to economies of scale. |
Material Costs | Some materials are expensive, but AM reduces waste, making it efficient for certain materials. | Material costs vary, but traditional methods may waste more material. |
Tooling and Setup Costs | No tooling required, ideal for prototyping and small batches. | High upfront costs for molds, dies, or tooling. |
Customization | Easy customization without additional costs, perfect for personalized products. | Customization requires retooling or redesign, increasing costs. |
Post-Processing | Some AM processes require significant post-processing, which can add to costs. | Post-processing requirements vary by method but are often less intensive than AM. |
Sustainability | Reduces material waste and energy consumption, aligning with sustainability goals. | Often less sustainable due to higher material waste and energy use. |
Still unsure if additive manufacturing is right for your project? Contact our experts today to explore cost-effective solutions tailored to your needs!