Brazing and soldering are both joining processes that use a filler metal to create a bond between two or more materials. However, they differ significantly in terms of the melting point of the filler metal, the strength of the joint, and the applications they are suited for. Brazing typically involves filler metals that melt above 450°C (840°F), creating stronger joints suitable for high-stress applications. Soldering, on the other hand, uses filler metals that melt below 450°C, making it ideal for delicate or low-temperature applications, such as electronics. While both processes rely on capillary action to distribute the filler metal, brazing is generally used for heavier-duty tasks, whereas soldering is preferred for precision work.
Key Points Explained:
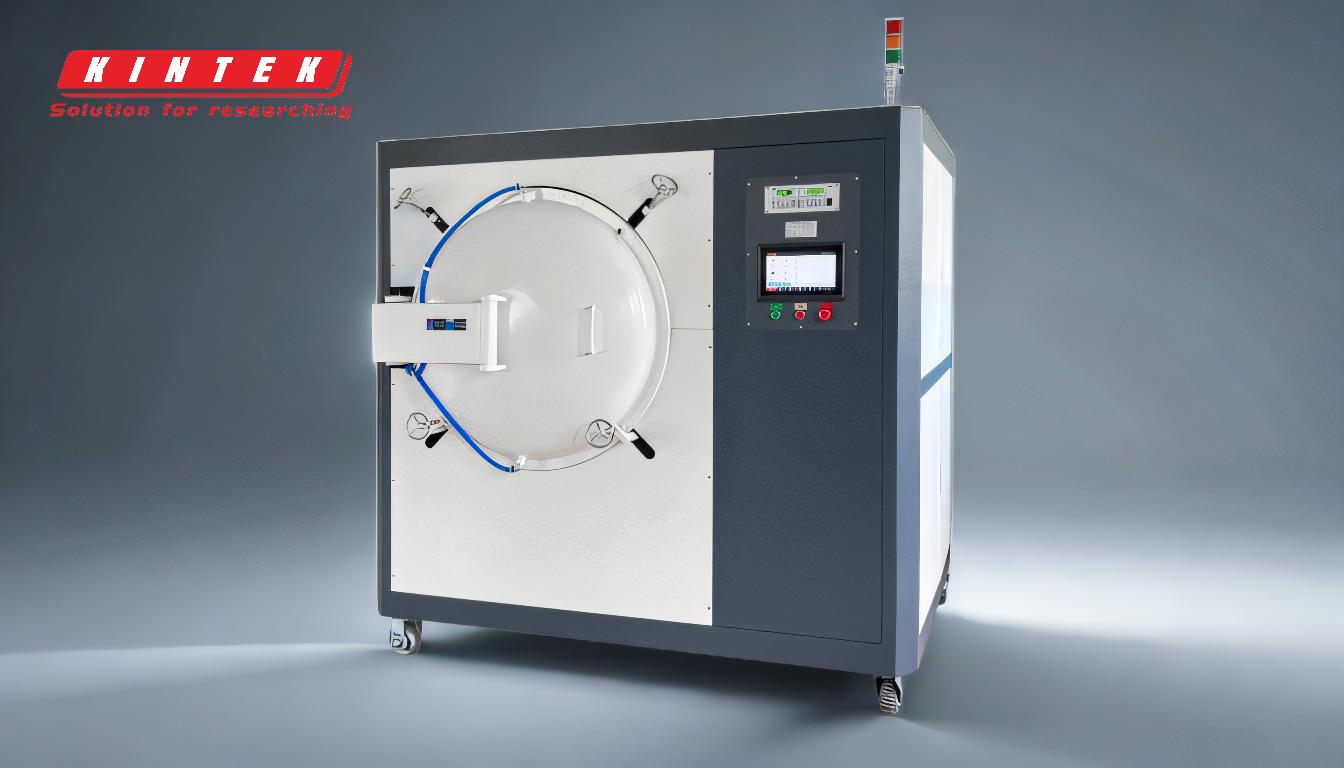
-
Difference in Melting Points:
- The primary distinction between brazing and soldering lies in the melting point of the filler metal used.
- Brazing employs filler metals that melt above 450°C (840°F), while soldering uses filler metals that melt below this temperature. This difference dictates the applications and strength of the joints formed.
-
Joint Strength:
- Brazing creates stronger joints due to the higher melting point of the filler metal, which often results in a metallurgical bond with the base materials.
- Soldering produces weaker joints, as the lower melting point filler metal does not form as strong a bond. However, this makes soldering ideal for applications where precision and low heat are critical.
-
Applications:
- Brazing is commonly used in industries requiring robust joints, such as automotive, aerospace, and HVAC systems. It is suitable for joining dissimilar metals and materials that must withstand high temperatures or mechanical stress.
- Soldering is widely used in electronics, plumbing, and jewelry making, where delicate components or low-temperature processes are necessary.
-
Process Mechanics:
- Both brazing and soldering rely on capillary action to distribute the molten filler metal into the gaps between the materials being joined.
- Brazing typically requires higher heat sources, such as torches or furnaces, while soldering often uses soldering irons or lower-temperature heat sources.
-
Filler Materials:
- Brazing filler materials include alloys like silver, copper, and nickel, which provide high strength and durability.
- Soldering filler materials are typically tin-lead, tin-silver, or lead-free alloys, chosen for their lower melting points and compatibility with sensitive materials.
-
Heat Impact on Base Materials:
- Brazing involves higher temperatures, which can affect the base materials, requiring careful control to avoid distortion or damage.
- Soldering, due to its lower temperatures, minimizes the risk of damaging heat-sensitive components, making it ideal for electronics and delicate assemblies.
By understanding these key differences, equipment and consumable purchasers can make informed decisions about which process and materials are best suited for their specific applications.
Summary Table:
Aspect | Brazing | Soldering |
---|---|---|
Melting Point | Above 450°C (840°F) | Below 450°C |
Joint Strength | Stronger joints, suitable for high-stress applications | Weaker joints, ideal for precision and low-heat applications |
Applications | Automotive, aerospace, HVAC systems | Electronics, plumbing, jewelry making |
Heat Source | Torches or furnaces | Soldering irons or low-temperature heat sources |
Filler Materials | Silver, copper, nickel alloys | Tin-lead, tin-silver, or lead-free alloys |
Heat Impact | Higher temperatures may affect base materials | Lower temperatures minimize damage to heat-sensitive components |
Need help deciding between brazing and soldering for your project? Contact our experts today for personalized advice!