Brazing and soldering are both methods used to join metal components using a filler material, but they differ significantly in terms of temperature, strength, and application. Brazing operates at higher temperatures (above 840°F) and typically results in stronger joints compared to soldering, which uses lower temperatures (below 840°F). Brazed joints are often as strong as the base metals themselves, making brazing a preferred method in industries requiring high durability, such as automotive, HVAC, and cookware manufacturing. Soldering, on the other hand, is more suited for delicate or low-stress applications, such as electronics or plumbing. The choice between brazing and soldering depends on the specific requirements of the project, including the materials involved, the desired joint strength, and the operating conditions.
Key Points Explained:
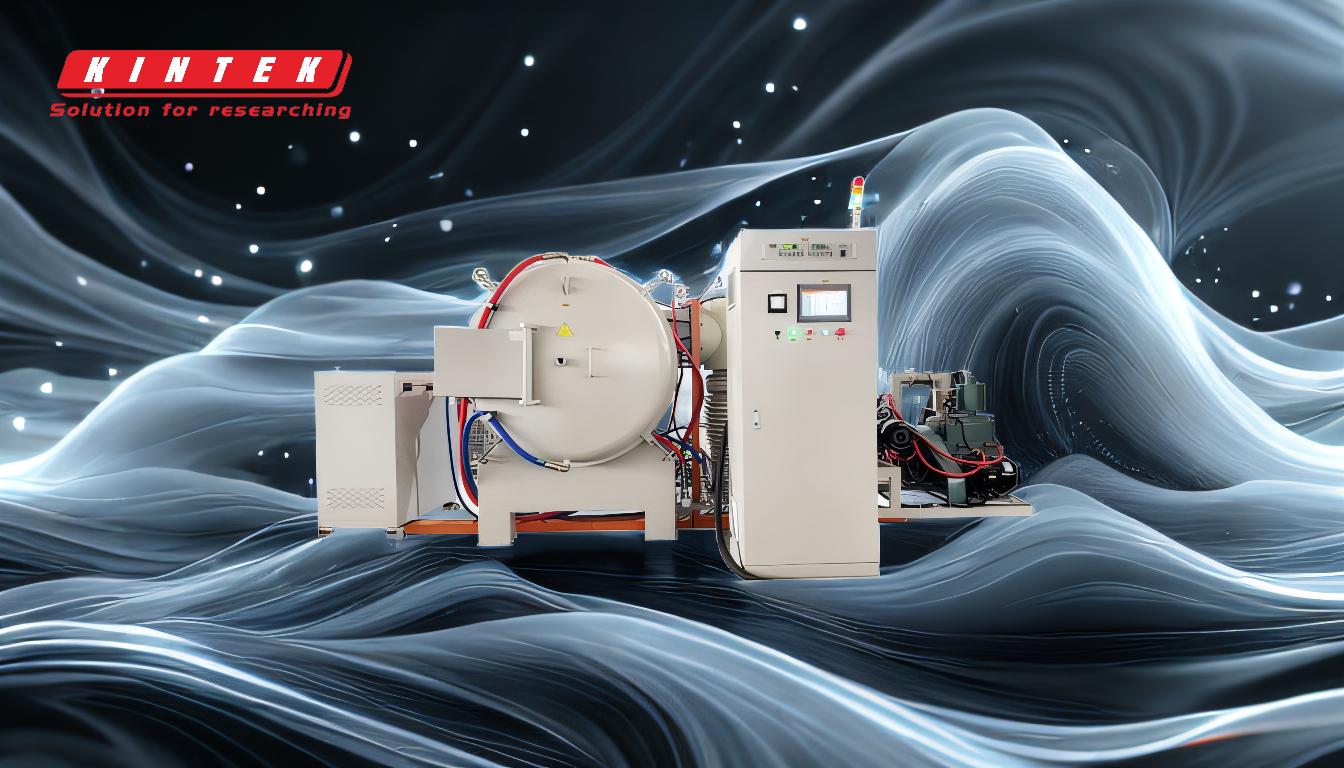
-
Temperature Differences:
- Brazing occurs at temperatures above 840°F, while soldering uses temperatures below 840°F.
- The higher temperature in brazing allows for the use of stronger filler materials, which contributes to the overall strength of the joint.
-
Joint Strength:
- Brazed joints are generally stronger than soldered joints. In many cases, brazed joints can be as strong as the base metals being joined.
- Soldered joints, while adequate for many applications, are typically weaker and more suitable for low-stress environments.
-
Applications:
- Brazing is widely used in industries that require high-strength joints, such as automotive manufacturing, HVAC systems, and cookware.
- Soldering is more commonly used in applications where precision and low heat are critical, such as in electronics assembly and plumbing.
-
Filler Materials:
- Brazing uses filler materials that are designed to withstand higher temperatures and provide greater strength.
- Soldering uses softer filler materials, which are easier to work with at lower temperatures but do not offer the same level of strength.
-
Durability and Longevity:
- Due to the higher strength of brazed joints, they are often more durable and longer-lasting, especially in high-stress or high-temperature environments.
- Soldered joints, while effective for their intended purposes, may not hold up as well under extreme conditions.
-
Cost and Complexity:
- Brazing can be more complex and costly due to the higher temperatures and specialized equipment required.
- Soldering is generally simpler and less expensive, making it a more accessible option for many applications.
In summary, while both brazing and soldering are effective joining techniques, brazing is typically stronger and more suitable for high-stress applications, whereas soldering is better suited for low-stress, precision tasks. The choice between the two methods should be based on the specific requirements of the project, including the materials involved and the conditions under which the joint will operate.
Summary Table:
Aspect | Brazing | Soldering |
---|---|---|
Temperature | Above 840°F | Below 840°F |
Joint Strength | As strong as base metals; ideal for high-stress applications | Weaker; suitable for low-stress environments |
Applications | Automotive, HVAC, cookware manufacturing | Electronics, plumbing, and precision tasks |
Filler Materials | Stronger, designed for high temperatures | Softer, easier to work with at lower temperatures |
Durability | More durable and long-lasting in high-stress or high-temperature conditions | Effective for intended purposes but less durable under extreme conditions |
Cost & Complexity | More complex and costly due to specialized equipment | Simpler and less expensive |
Still unsure which method is right for your project? Contact our experts today for personalized advice!