Diamond-like carbon (DLC) coatings are highly corrosion-resistant due to their chemical inertness and ability to perform well in corrosive environments. These coatings are composed of a mix of sp3 (diamond-like) and sp2 (graphite-like) carbon bonds, which contribute to their high hardness, low friction, and resistance to chemicals. DLC coatings are widely used in applications requiring durability, reduced friction, and protection against wear and corrosion. Their properties, such as high surface smoothness and biocompatibility, make them suitable for various industries, including automotive, medical, and optical sensing. The corrosion resistance of DLC coatings is further enhanced by their ability to form a protective barrier on surfaces, preventing chemical reactions that lead to degradation.
Key Points Explained:
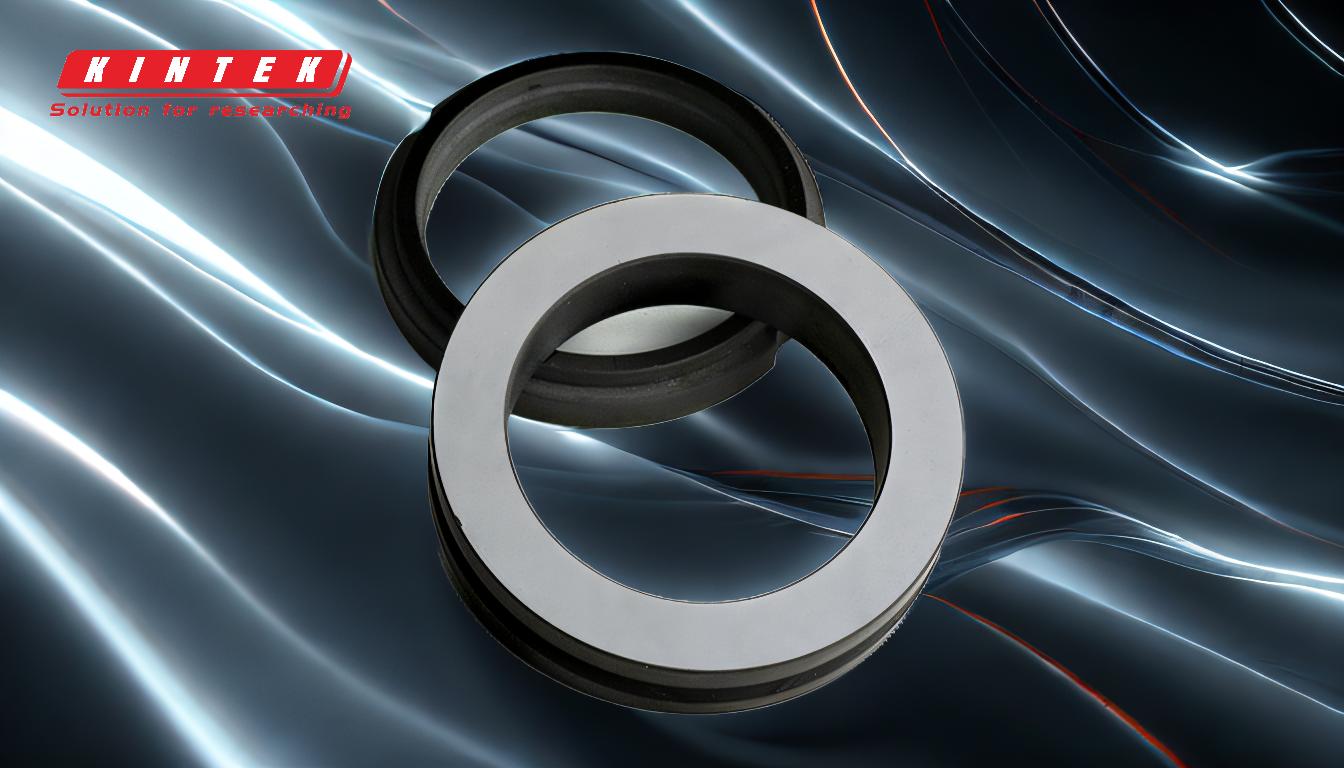
-
Chemical Inertness of DLC Coatings:
- DLC coatings are chemically inert, meaning they do not easily react with other substances. This property is crucial for corrosion resistance, as it prevents the coating from degrading when exposed to corrosive agents like acids, salts, or moisture.
- The chemical inertness is attributed to the strong carbon-carbon bonds (sp3 and sp2) in the coating, which create a stable and non-reactive surface.
-
Performance in Corrosive Environments:
- DLC coatings are specifically noted for their high performance in corrosive environments. This makes them ideal for applications where materials are exposed to harsh conditions, such as in marine, automotive, or industrial settings.
- The coating acts as a barrier, protecting the underlying material from chemical reactions that could lead to rust, oxidation, or other forms of corrosion.
-
High Hardness and Wear Resistance:
- The high hardness of DLC coatings contributes to their durability and ability to withstand mechanical wear. This hardness is a result of the sp3 carbon bonds, which mimic the properties of diamond.
- By resisting wear, the coating maintains its integrity over time, ensuring long-term protection against corrosion.
-
Low Coefficient of Friction:
- The low friction properties of DLC coatings reduce the likelihood of wear and tear, which can expose underlying materials to corrosive agents. This is particularly beneficial in moving parts or sliding applications.
- The reduced friction also minimizes heat generation, which can otherwise accelerate corrosion in certain environments.
-
Tailored Properties for Specific Applications:
- The properties of DLC coatings, such as grain size, surface roughness, and crystallinity, can be customized by controlling deposition parameters and gas phase composition during manufacturing.
- This flexibility allows for the optimization of corrosion resistance based on the specific requirements of the application.
-
Applications in Corrosion-Prone Industries:
- DLC coatings are used in industries where corrosion resistance is critical, such as automotive (for engine components), medical (for implants), and optical sensing (for protective layers).
- Their biocompatibility and resistance to chemicals make them suitable for medical devices that must withstand bodily fluids and sterilization processes.
-
Comparison to Other Coatings:
- Unlike some traditional coatings that may degrade over time or require frequent maintenance, DLC coatings offer long-lasting protection with minimal upkeep.
- Their combination of hardness, low friction, and chemical inertness makes them superior to many other coating materials in terms of corrosion resistance.
In summary, DLC coatings are highly corrosion-resistant due to their chemical inertness, high hardness, and ability to perform well in corrosive environments. These properties make them an excellent choice for applications requiring durable, low-friction, and chemically resistant surfaces.
Summary Table:
Property | Description |
---|---|
Chemical Inertness | Prevents reactions with corrosive agents like acids, salts, and moisture. |
High Hardness | Mimics diamond properties, ensuring durability and wear resistance. |
Low Friction | Reduces wear and tear, minimizing exposure to corrosive agents. |
Customizable Properties | Tailored grain size, roughness, and crystallinity for specific applications. |
Applications | Used in automotive, medical, and optical sensing industries for corrosion protection. |
Learn how DLC coatings can enhance your product's durability—contact our experts today!