PVD (Physical Vapor Deposition) plating is indeed a highly effective and advantageous coating technology. It is widely recognized for its ability to produce durable, corrosion-resistant, and aesthetically pleasing finishes on a variety of materials. PVD coatings are often harder and more durable than those applied by traditional methods like electroplating, making them suitable for a wide range of applications, from decorative items to industrial components. Additionally, PVD processes are more environmentally friendly compared to traditional coating methods, as they do not produce harmful by-products. The technology is versatile, allowing for the deposition of various inorganic and some organic materials on diverse substrates. Despite being more complex and costly than some alternatives, the superior quality, durability, and environmental benefits of PVD plating make it a preferred choice in many industries.
Key Points Explained:
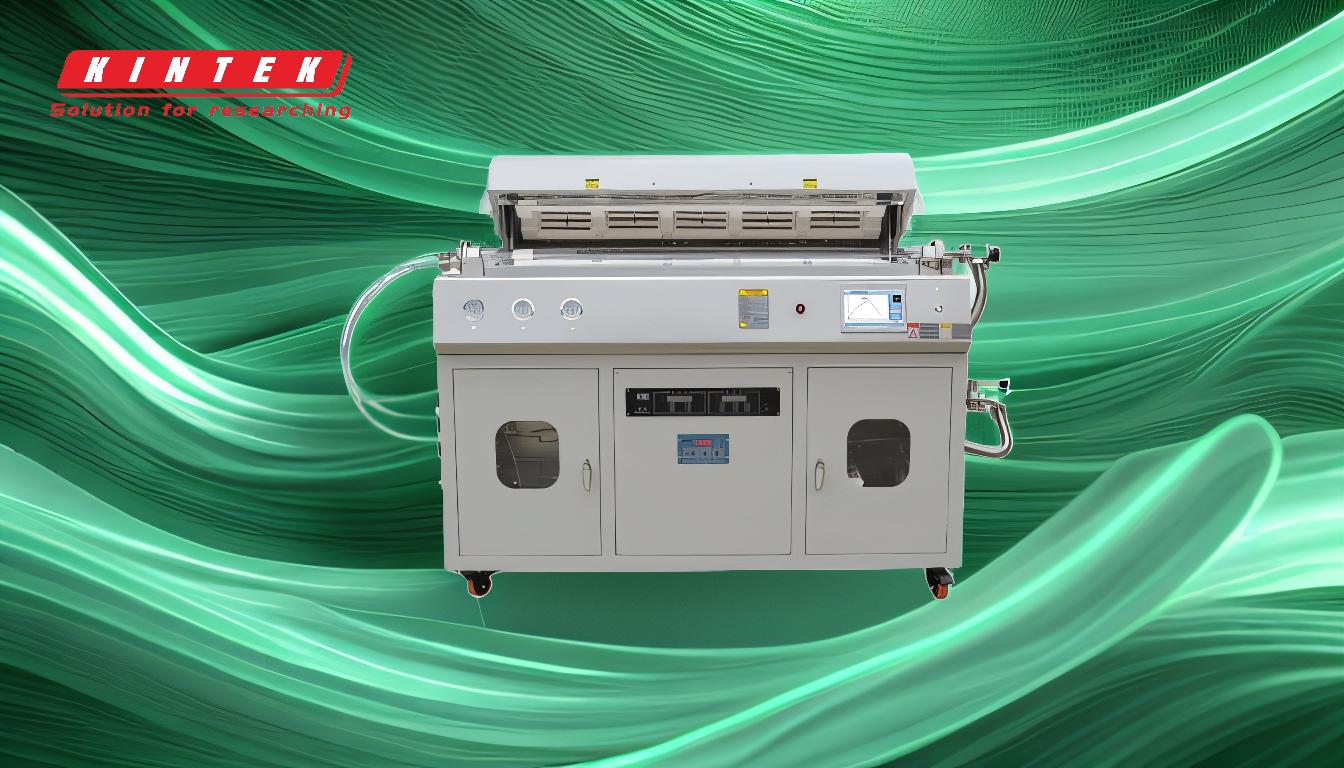
-
Durability and Corrosion Resistance:
- PVD coatings are known for their exceptional hardness and corrosion resistance, often surpassing those achieved through electroplating. This makes them ideal for applications where durability is critical, such as in marine environments or for heavy-duty industrial components.
-
High Temperature and Impact Strength:
- PVD coatings exhibit high temperature resistance and good impact strength, which are essential for applications involving extreme conditions. This is particularly beneficial in industries like automotive and aerospace, where components are subjected to high stress and temperature variations.
-
Abrasion Resistance and Longevity:
- The abrasion resistance of PVD coatings is superior, often eliminating the need for additional protective topcoats. This not only reduces the overall cost but also extends the lifespan of the coated products, sometimes by up to ten times, making them last more than 25 years in certain cases.
-
Versatility in Material and Substrate Compatibility:
- PVD technology can utilize a wide range of inorganic and some organic coating materials, making it highly versatile. It can be applied to various substrates, including metals, ceramics, and even some plastics, which broadens its applicability across different industries.
-
Environmental Friendliness:
- PVD processes are more environmentally friendly compared to traditional coating methods like electroplating and painting. They do not produce toxic substances, making them a greener alternative. This is increasingly important as industries move towards more sustainable practices.
-
Low-Temperature Processes and High Deposition Rates:
- PVD is advantageous for low-temperature processes, which is beneficial for substrates that cannot withstand high temperatures. It also works well at high deposition rates, making it efficient for mass production. However, for precise, isotropic coating of all surfaces, ALD (Atomic Layer Deposition) might be more suitable.
-
Cost and Complexity:
- While PVD processes, particularly ion beam sputtering, produce better film quality and uniformity, they are more costly and complex than simpler methods like evaporation. However, the higher initial investment is often justified by the superior performance and longevity of the coatings.
-
Applications in Various Industries:
- PVD technology is widely used in the manufacturing of jewelry, door and window hardware, kitchen and bathroom hardware, lamps, marine supplies, and handicrafts. It is also used to extend the life of car parts, surgical tools, drill bits, and guns, among other products.
In summary, PVD plating is a highly effective and versatile coating technology that offers numerous advantages, including durability, corrosion resistance, environmental friendliness, and compatibility with a wide range of materials and substrates. Despite its higher cost and complexity, the benefits it provides make it a preferred choice in many industries.
Summary Table:
Key Benefits of PVD Plating | Details |
---|---|
Durability & Corrosion Resistance | Superior hardness and corrosion resistance, ideal for harsh environments. |
High Temperature & Impact Strength | Withstands extreme conditions, perfect for automotive and aerospace. |
Abrasion Resistance & Longevity | Lasts up to 25 years, reducing the need for additional protective coatings. |
Versatility | Compatible with metals, ceramics, and plastics for diverse applications. |
Environmental Friendliness | No toxic by-products, making it a sustainable coating option. |
Applications | Used in jewelry, hardware, marine supplies, and industrial components. |
Ready to enhance your products with PVD plating? Contact us today to learn more!