Physical Vapor Deposition (PVD) and plating are both surface coating techniques, but they differ significantly in their processes, applications, and outcomes. PVD is a vacuum-based process that deposits thin films of material onto a substrate, offering superior durability, wear resistance, and environmental safety compared to traditional electroplating. Electroplating, on the other hand, involves depositing a metal coating through an electrochemical process, often requiring additional protective layers to prevent tarnishing or corrosion. While both methods aim to enhance surface properties, PVD is generally more advanced and environmentally friendly, making it suitable for high-performance applications.
Key Points Explained:
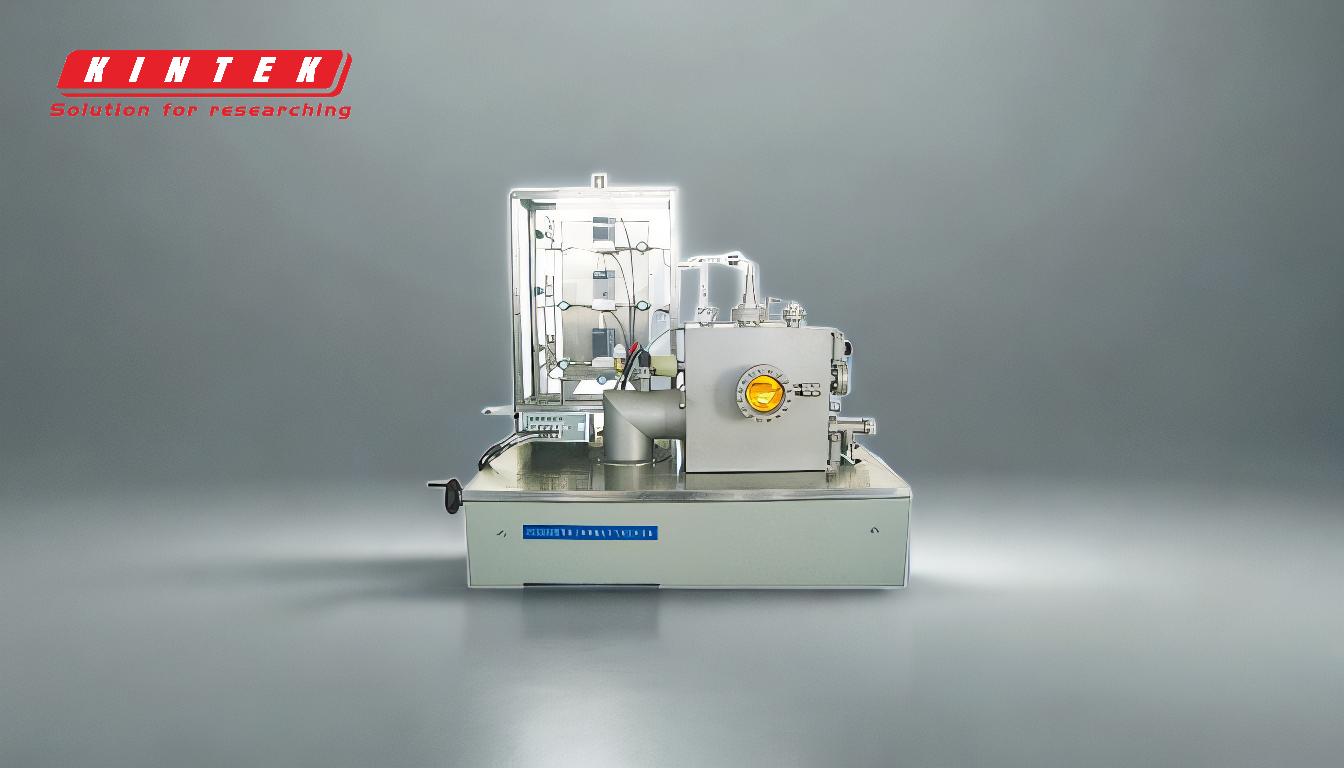
-
Process Differences:
- PVD: A vacuum-based process where materials are vaporized and then deposited onto a substrate. Techniques like cathodic arc evaporation and magnetron sputtering are commonly used.
- Electroplating: An electrochemical process where metal ions are deposited onto a substrate through an electrolyte solution. It often requires additional clear coats to prevent tarnishing or corrosion.
-
Durability and Resistance:
- PVD: Known for its exceptional durability, wear resistance, and resistance to fading, tarnishing, and corrosion. It does not require additional protective layers, making it more robust in harsh environments.
- Electroplating: While effective, it often requires clear coats that degrade over time, leading to potential tarnishing or corrosion. This makes it less durable compared to PVD.
-
Environmental Impact:
- PVD: Environmentally friendly, as it does not release harmful chemicals or by-products during the process. It is considered a cleaner alternative to traditional plating methods.
- Electroplating: Often involves the use of hazardous chemicals and produces waste that requires careful disposal, making it less environmentally friendly.
-
Applications:
- PVD: Commonly used in high-performance applications such as aerospace, automotive, and medical devices. It is suitable for materials like titanium, zirconium, aluminium, stainless steel, and copper.
- Electroplating: Widely used for decorative finishes, jewelry, and consumer electronics. It is often applied to materials like brass, nickel, and gold.
-
Deposition Rates and Functional Characteristics:
- PVD: Offers moderate deposition rates and produces materials with excellent functional characteristics, such as high hardness and chemical resistance.
- Electroplating: Generally has lower deposition rates compared to PVD and may not achieve the same level of functional performance in terms of wear resistance and durability.
-
Innovative Techniques:
- Hybrid PVD: Combines elements of cathodic arc evaporation and magnetron sputtering, offering potential advantages in deposition rate and ionization degree. This technique is less common but shows promise for specialized applications.
- PECVD (Plasma-Enhanced Chemical Vapor Deposition): Offers higher deposition rates compared to traditional PVD and can produce materials with similar functional characteristics, addressing novel aspects of functional coating fabrication.
In summary, while both PVD and plating aim to enhance surface properties, PVD is generally more advanced, durable, and environmentally friendly, making it suitable for high-performance and specialized applications. Electroplating remains a cost-effective option for decorative and less demanding uses but falls short in terms of durability and environmental impact.
Summary Table:
Aspect | PVD | Plating |
---|---|---|
Process | Vacuum-based, vaporizes and deposits materials | Electrochemical, deposits metal ions through an electrolyte solution |
Durability | Superior wear resistance, no additional protective layers required | Requires clear coats, less durable over time |
Environmental Impact | No harmful chemicals or by-products, eco-friendly | Uses hazardous chemicals, produces waste |
Applications | Aerospace, automotive, medical devices | Decorative finishes, jewelry, consumer electronics |
Deposition Rates | Moderate | Lower compared to PVD |
Innovative Techniques | Hybrid PVD, PECVD | Limited advancements |
Still unsure which coating method is right for your project? Contact our experts today for personalized advice!