Sintering and melting are two distinct processes used in material processing, each with its own advantages and applications. Sintering involves compacting and heating powdered materials below their melting point to form a solid mass, while melting involves heating materials until they liquefy. The choice between sintering and melting depends on the specific requirements of the application, such as material properties, energy efficiency, and environmental impact. Sintering is often preferred for its ability to produce complex shapes with minimal material waste, while melting is advantageous for achieving high purity and homogeneity in the final product.
Key Points Explained:
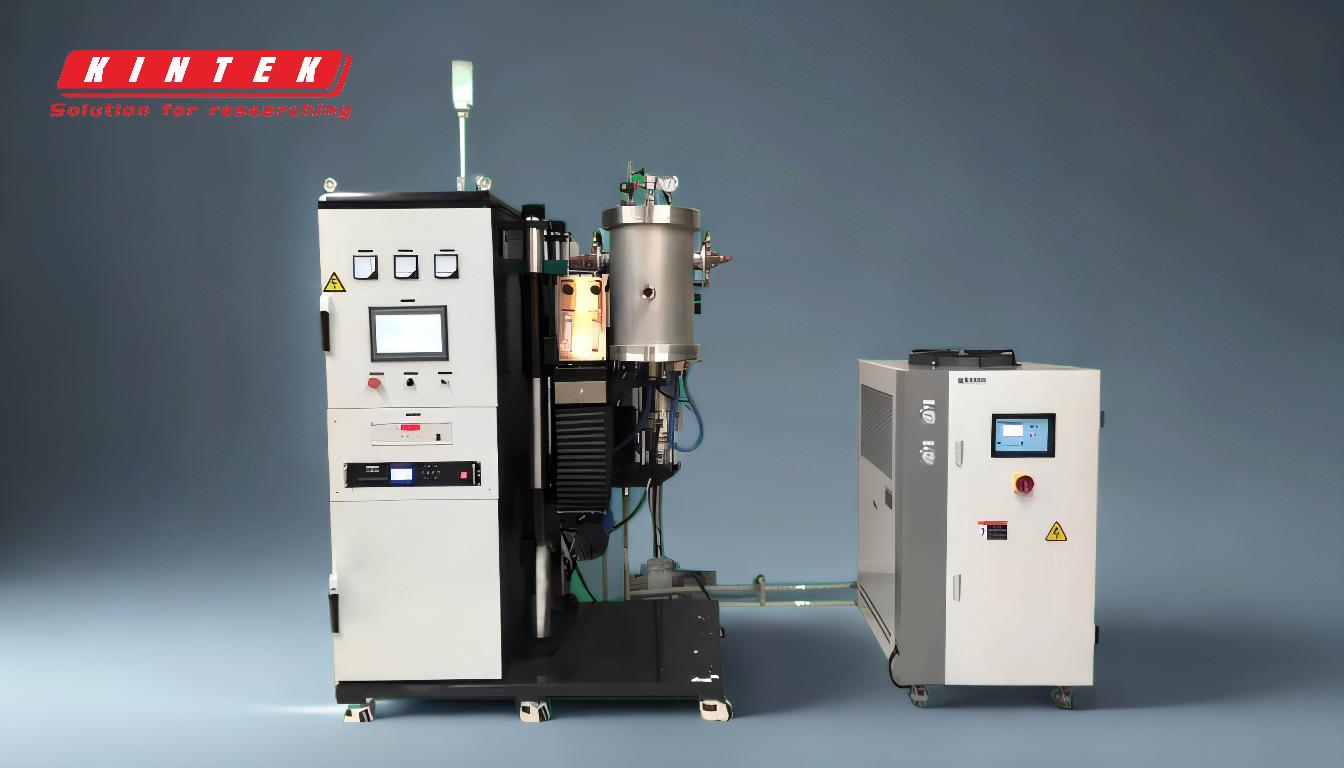
-
Process Mechanism:
- Sintering: This process involves compacting powdered materials and heating them below their melting point. The particles bond together through diffusion, forming a solid mass without complete liquefaction. This is particularly useful for creating complex shapes and structures.
- Melting: In contrast, melting involves heating materials until they reach their liquid state. This allows for the complete mixing of constituents, ensuring high purity and homogeneity in the final product.
-
Energy Efficiency:
- Sintering: Generally, sintering is more energy-efficient than melting because it requires lower temperatures. This can lead to significant energy savings, especially in large-scale production.
- Melting: Melting typically requires higher temperatures, which can be energy-intensive. However, modern techniques like induction melting can improve energy efficiency by directly heating the material.
-
Environmental Impact:
- Sintering: Sintering is often considered more environmentally friendly due to lower energy consumption and reduced emissions. The process can be conducted in a controlled atmosphere, minimizing the release of harmful gases.
- Melting: While traditional melting methods can produce emissions, advanced techniques like induction melting are designed to be cleaner, with no hot or harmful emissions released into the atmosphere.
-
Material Properties:
- Sintering: Sintered materials can have unique properties, such as controlled porosity and tailored microstructures. This makes sintering ideal for applications requiring specific material characteristics, such as filters or biomedical implants.
- Melting: Melting is preferred when high purity and homogeneity are required. The process allows for the complete mixing of alloying elements, ensuring uniform properties throughout the material.
-
Complexity and Precision:
- Sintering: Sintering is well-suited for producing complex shapes with high precision. The process allows for near-net-shape manufacturing, reducing the need for additional machining and minimizing material waste.
- Melting: Melting is typically used for simpler shapes and bulk production. The process can be more challenging for intricate designs due to the need for molds and the potential for material shrinkage upon cooling.
-
Applications:
- Sintering: Common applications include the production of ceramics, metals, and composites. Sintering is also used in powder metallurgy to create components with specific mechanical properties.
- Melting: Melting is widely used in the production of metals and alloys, particularly in industries requiring high-strength materials, such as aerospace and automotive.
In summary, the choice between sintering and melting depends on the specific requirements of the application. Sintering offers advantages in terms of energy efficiency, environmental impact, and the ability to produce complex shapes, while melting is preferred for achieving high purity and homogeneity. For more information on sintering, you can explore the topic of sintering furnace.
Summary Table:
Aspect | Sintering | Melting |
---|---|---|
Process Mechanism | Compacts and heats powdered materials below melting point. | Heats materials until they liquefy. |
Energy Efficiency | More energy-efficient due to lower temperatures. | Energy-intensive but improved with modern techniques like induction melting. |
Environmental Impact | Lower energy consumption and reduced emissions. | Cleaner with advanced methods like induction melting. |
Material Properties | Produces controlled porosity and tailored microstructures. | Ensures high purity and homogeneity. |
Complexity & Precision | Ideal for complex shapes with minimal waste. | Suitable for simpler shapes and bulk production. |
Applications | Ceramics, metals, composites, and powder metallurgy. | Metals and alloys for aerospace, automotive, and high-strength industries. |
Still unsure which process is right for your application? Contact our experts today for personalized advice!