Thermal evaporation and magnetron sputtering are both widely used thin-film deposition techniques, each with distinct advantages and limitations. Thermal evaporation is favored for its high deposition rates, simplicity, and cost-effectiveness, making it ideal for applications where speed and material utilization efficiency are prioritized, such as in optics, electronics, and solar cells. It is particularly suitable for materials with low melting points and offers excellent uniformity. On the other hand, magnetron sputtering excels in producing high-quality films with superior density, adhesion, and surface morphology, making it the preferred choice for applications requiring precise stoichiometry, low surface roughness, and enhanced film properties. The choice between the two techniques depends on the specific requirements of the application, such as film quality, deposition rate, and material compatibility.
Key Points Explained:
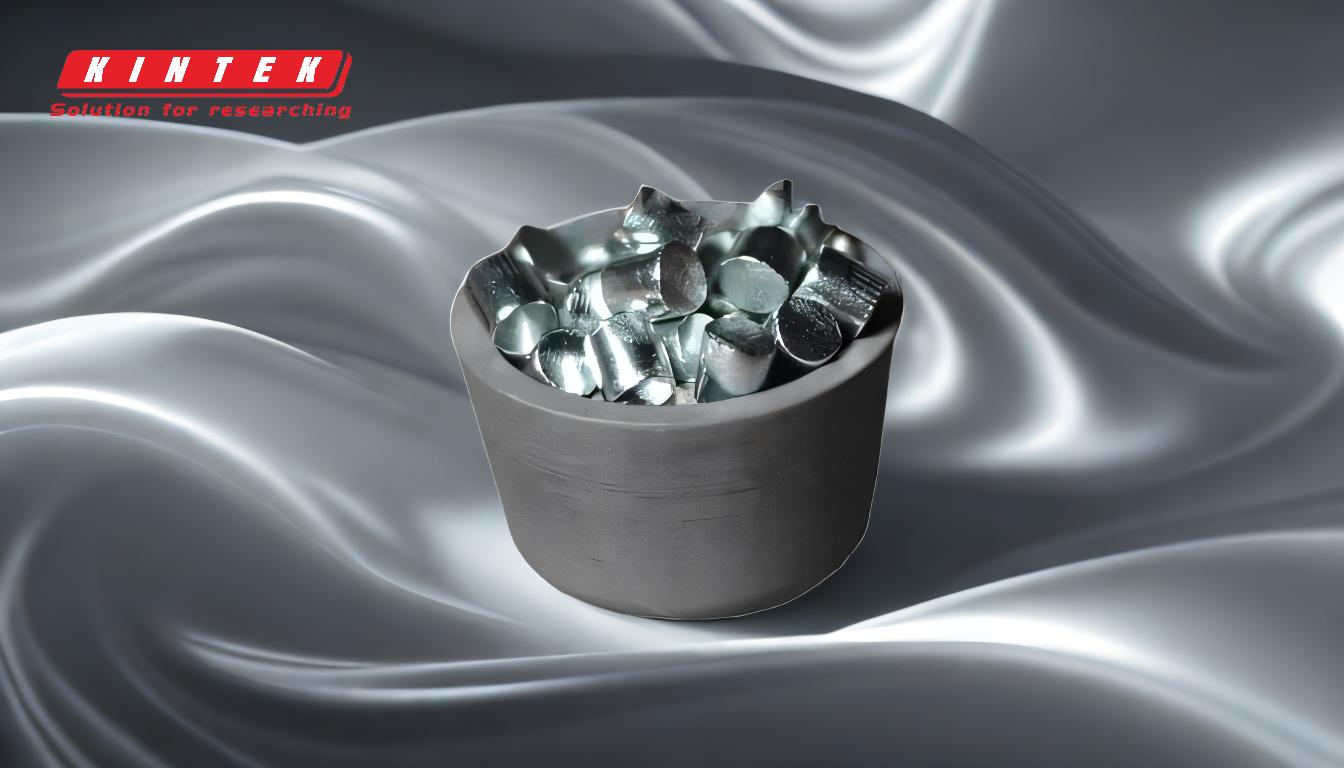
-
Deposition Rate and Efficiency:
- Thermal Evaporation: Offers significantly higher deposition rates compared to magnetron sputtering, making it faster and more efficient for applications where speed is critical. This is particularly advantageous in industries like optics and electronics, where rapid production is often required.
- Magnetron Sputtering: While slower, it provides better control over film properties, which is essential for applications requiring high precision and quality.
-
Film Quality and Properties:
- Thermal Evaporation: Produces films that are less dense and have larger grain sizes compared to sputtered films. This can result in lower adhesion and surface roughness, which may not be suitable for applications demanding high film quality.
- Magnetron Sputtering: Generates denser films with smaller grain sizes, better adhesion, and properties closer to bulk materials. This makes it ideal for applications where film quality, density, and surface morphology are critical.
-
Material Compatibility:
- Thermal Evaporation: Compatible with both metals and nonmetals, and particularly suitable for materials with low melting points. It can also create alloys and perform sequential coatings, offering flexibility in material selection.
- Magnetron Sputtering: Primarily used with metals, but offers greater versatility in terms of color options and modulation, which is beneficial for applications requiring specific aesthetic or functional properties.
-
Cost and Complexity:
- Thermal Evaporation: Relatively simple and cost-effective, with low power consumption requirements. It is a gentle technique that produces low-energy evaporated particles, making it suitable for delicate applications.
- Magnetron Sputtering: More complex and typically more expensive due to the need for specialized equipment and higher power consumption. However, the investment is justified for applications requiring high-quality films with precise properties.
-
Uniformity and Directionality:
- Thermal Evaporation: Provides excellent uniformity with the use of planetary substrate fixturing and uniformity masks. It also offers good directionality, which is advantageous for coating complex geometries.
- Magnetron Sputtering: While it can achieve high uniformity, it may require more sophisticated setup and control to achieve the same level of directionality as thermal evaporation.
-
Applications and Industry Use:
- Thermal Evaporation: Widely used in industries where high deposition rates and material efficiency are prioritized, such as in the production of optical coatings, electronic components, and solar cells.
- Magnetron Sputtering: Preferred in industries requiring high-quality films with precise properties, such as in the production of semiconductor devices, protective coatings, and decorative finishes.
In summary, the choice between thermal evaporation and magnetron sputtering depends on the specific requirements of the application. Thermal evaporation is better suited for high-speed, cost-effective production, while magnetron sputtering is the go-to method for high-quality, precise film deposition. Both techniques have their unique advantages and limitations, and the decision should be based on factors such as film quality, deposition rate, material compatibility, and cost considerations.
Summary Table:
Aspect | Thermal Evaporation | Magnetron Sputtering |
---|---|---|
Deposition Rate | High | Moderate |
Film Quality | Less dense, larger grain sizes | Denser, smaller grain sizes |
Material Compatibility | Metals, nonmetals, low melting points | Primarily metals, versatile color options |
Cost | Low cost, simple setup | Higher cost, complex setup |
Uniformity | Excellent with planetary fixturing | High but requires sophisticated control |
Applications | Optics, electronics, solar cells | Semiconductors, protective coatings |
Still unsure which thin-film deposition technique is right for your project? Contact our experts today for personalized advice!