Vacuum casting is a manufacturing process used to produce high-quality prototypes or small batches of parts. The cost of vacuum casting depends on several factors, including material selection, mold complexity, batch size, and post-processing requirements. While it is generally more cost-effective than other methods like injection molding for small-scale production, it can still be relatively expensive due to the labor-intensive nature of the process and the need for high-quality materials and molds. However, its ability to produce detailed and accurate parts with excellent surface finishes often justifies the cost for specific applications.
Key Points Explained:
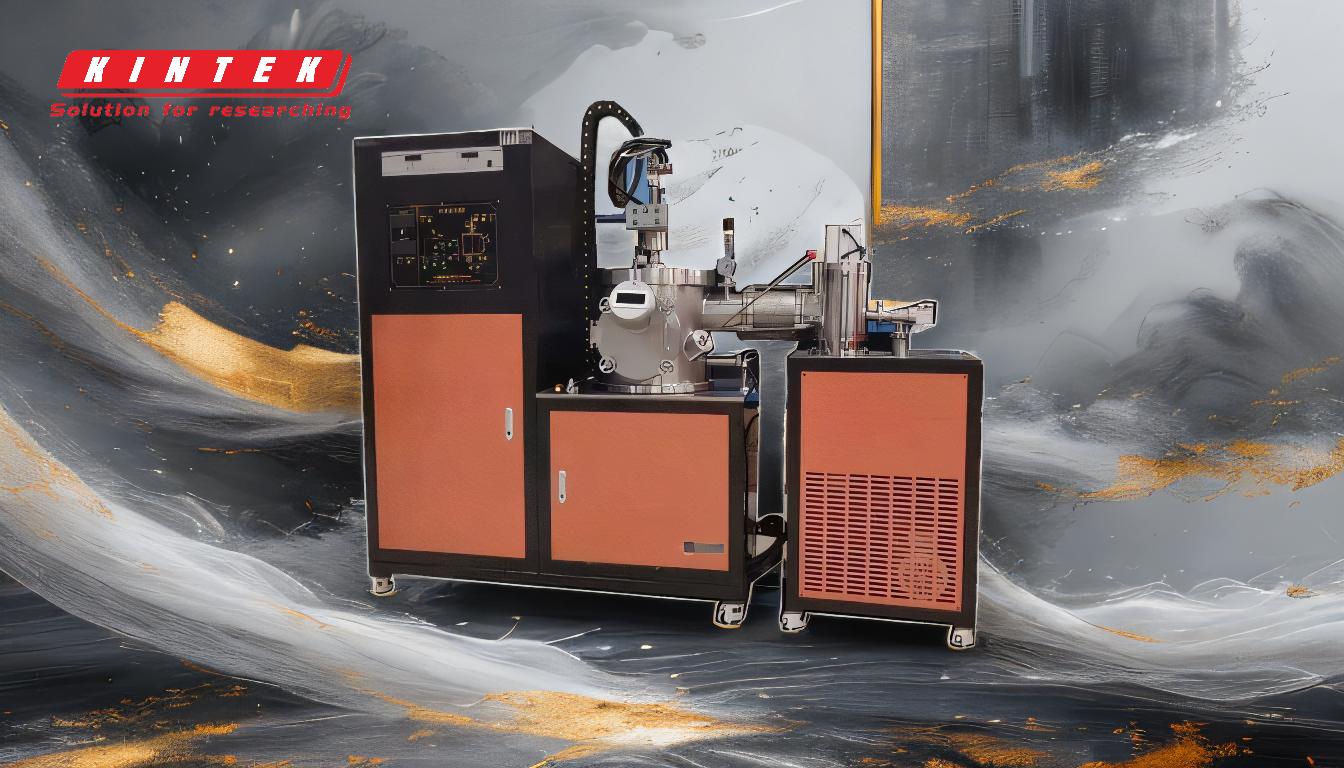
-
What is Vacuum Casting?
- Vacuum casting is a manufacturing technique used to create high-quality prototypes or small batches of parts. It involves pouring liquid resin into a silicone mold under vacuum conditions to eliminate air bubbles and ensure precise replication of the master model.
- This process is ideal for producing parts with fine details, smooth finishes, and complex geometries.
-
Factors Influencing the Cost of Vacuum Casting
- Material Costs: The type of resin used significantly impacts the overall cost. High-performance resins or specialized materials (e.g., flexible, heat-resistant, or transparent resins) are more expensive than standard options.
- Mold Complexity: Complex molds with intricate designs or undercuts require more time and skill to create, increasing costs. The number of cavities in the mold also affects pricing.
- Batch Size: While vacuum casting is cost-effective for small batches (typically 10–50 parts), the cost per unit decreases as the batch size increases. However, the silicone mold has a limited lifespan, so larger production runs may require multiple molds, adding to expenses.
- Labor and Equipment: The process is labor-intensive, requiring skilled technicians to create the master model, prepare the mold, and cast the parts. Additionally, maintaining vacuum casting equipment can contribute to higher costs.
- Post-Processing: Finishing steps like painting, polishing, or assembly add to the overall expense.
-
Comparison with Other Manufacturing Methods
- Injection Molding: Vacuum casting is generally cheaper for small-scale production because it avoids the high upfront costs of creating steel or aluminum molds. However, for large-scale production, injection molding becomes more cost-effective due to lower per-unit costs.
- 3D Printing: While 3D printing is often cheaper for single prototypes, vacuum casting offers better surface finishes and material properties, making it more suitable for functional prototypes or end-use parts.
- CNC Machining: CNC machining is more expensive for complex geometries or small batches, as it involves significant material waste and longer machining times. Vacuum casting is often a better choice for these scenarios.
-
When is Vacuum Casting Worth the Cost?
- Prototyping: Vacuum casting is ideal for creating high-quality prototypes that closely resemble the final product in terms of material properties and surface finish.
- Small Batch Production: For producing small quantities of parts (e.g., 10–50 units), vacuum casting is often the most cost-effective method.
- Complex Geometries: The ability to replicate intricate details and undercuts makes vacuum casting a preferred choice for parts with complex designs.
- Material Variety: The wide range of available resins allows for the production of parts with specific mechanical, thermal, or aesthetic properties.
-
Cost-Saving Tips for Vacuum Casting
- Optimize the design to reduce mold complexity and material usage.
- Choose standard resins unless specialized properties are required.
- Plan batch sizes carefully to maximize the lifespan of the silicone mold.
- Combine multiple parts into a single mold to reduce costs.
-
Conclusion
- While vacuum casting can be expensive due to material, labor, and mold costs, it offers significant advantages in terms of part quality, detail, and material versatility. For small-scale production or high-quality prototypes, the cost is often justified by the superior results. By understanding the factors that influence pricing and optimizing the design and production process, the expense of vacuum casting can be effectively managed.
Summary Table:
Factor | Impact on Cost |
---|---|
Material Costs | High-performance or specialized resins increase costs. |
Mold Complexity | Intricate designs or undercuts raise costs due to increased labor and skill. |
Batch Size | Cost per unit decreases with larger batches, but multiple molds may be required. |
Labor and Equipment | Skilled technicians and equipment maintenance add to expenses. |
Post-Processing | Finishing steps like painting or polishing increase overall costs. |
Need help estimating your vacuum casting costs? Contact our experts today for a tailored solution!