When brazing aluminum, the use of flux is highly recommended to ensure proper wetting, flow, and bonding of the filler metal to the base material. Flux plays a critical role in removing oxides from the aluminum surface, which is essential for achieving a strong and durable joint. The selection of the right flux, matched to the filler metal, is crucial for optimal brazing performance. Below, we explore the key considerations and reasons for using flux in aluminum brazing.
Key Points Explained:
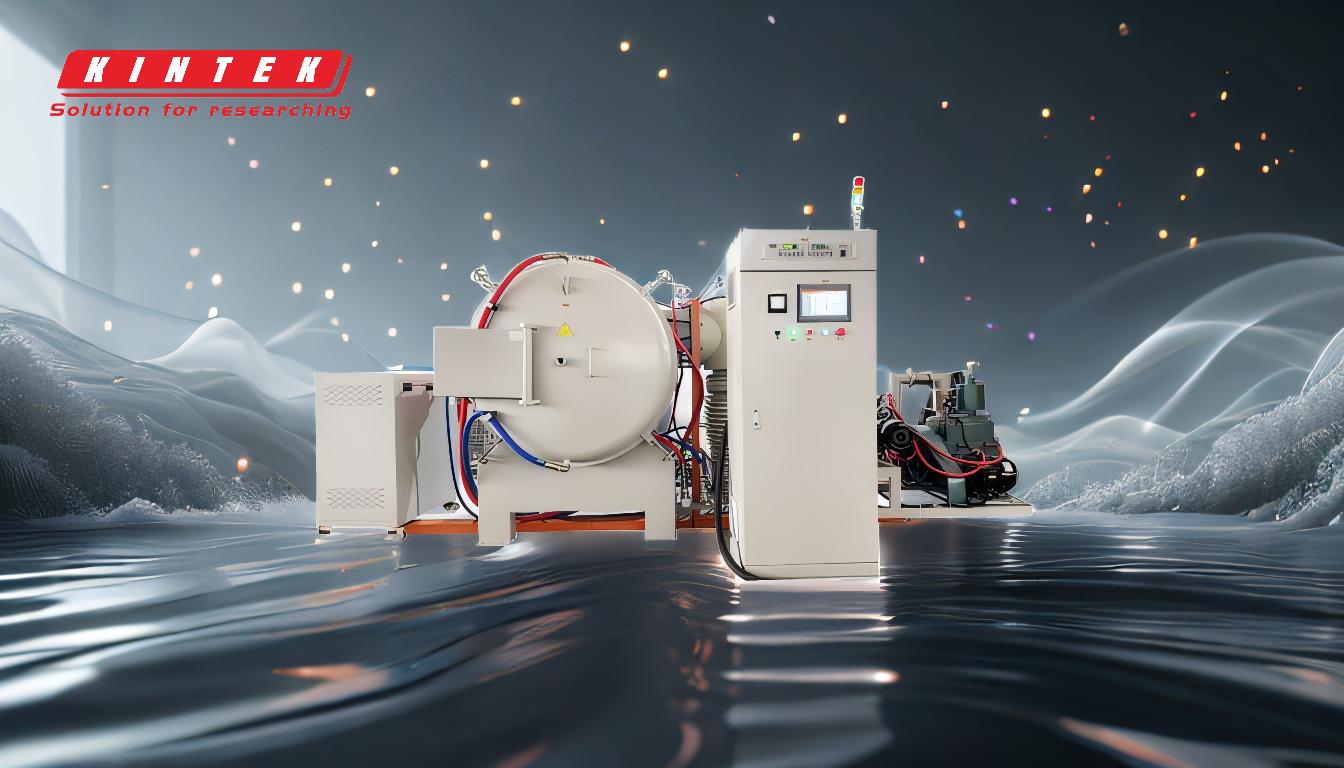
-
Role of Flux in Aluminum Brazing:
- Aluminum naturally forms a thin oxide layer on its surface, which can hinder the bonding process during brazing.
- Flux chemically reacts with the oxide layer, breaking it down and allowing the filler metal to wet and flow onto the clean aluminum surface.
- Without flux, the filler metal may not adhere properly, leading to weak or incomplete joints.
-
Matching Flux to Filler Metal:
- The flux core or composition should be specifically designed for the type of filler metal being used. For example, aluminum-silicon filler metals typically require fluoride-based fluxes.
- Using a mismatched flux can result in poor wetting, incomplete oxide removal, or even contamination of the joint.
-
Types of Flux for Aluminum Brazing:
- Corrosive Fluxes: These are commonly used for aluminum brazing and contain fluoride compounds. They are highly effective at removing oxides but require thorough post-braze cleaning to prevent corrosion.
- Non-Corrosive Fluxes: These are less common for aluminum but may be used in specific applications where post-braze cleaning is difficult.
-
Application Methods:
- Flux can be applied as a paste, powder, or pre-coated on the filler metal (flux-cored rods).
- The method of application depends on the brazing process (e.g., torch brazing, furnace brazing) and the joint design.
-
Importance of Proper Flux Removal:
- After brazing, residual flux must be removed to prevent corrosion and ensure the longevity of the joint.
- Cleaning methods include rinsing with water, using chemical cleaners, or mechanical removal, depending on the flux type.
-
Challenges of Fluxless Brazing:
- While fluxless brazing is possible in controlled environments (e.g., vacuum or inert gas atmospheres), it requires precise control of temperature and atmosphere to prevent oxide formation.
- For most applications, using flux is more practical and reliable.
-
Advantages of Using Flux:
- Ensures proper wetting and flow of the filler metal.
- Improves joint strength and durability.
- Reduces the risk of defects such as voids or incomplete bonding.
-
Considerations for Flux Selection:
- Base material composition and thickness.
- Filler metal type and melting point.
- Brazing method and equipment used.
In summary, using flux when brazing aluminum is essential for achieving high-quality, reliable joints. The flux must be carefully selected to match the filler metal and application requirements. Proper application and post-braze cleaning are critical to ensure the success of the brazing process and the longevity of the joint.
Summary Table:
Key Aspect | Details |
---|---|
Role of Flux | Removes oxides, ensures proper wetting and bonding of filler metal. |
Matching Flux to Filler | Use fluoride-based fluxes for aluminum-silicon filler metals. |
Types of Flux | Corrosive (fluoride-based) or non-corrosive (for specific applications). |
Application Methods | Paste, powder, or pre-coated on filler metal (flux-cored rods). |
Flux Removal | Clean thoroughly post-braze to prevent corrosion. |
Advantages of Flux | Improves joint strength, durability, and reduces defects. |
Flux Selection Factors | Base material, filler metal type, brazing method, and equipment. |
Need help selecting the right flux for your aluminum brazing project? Contact our experts today for personalized advice!