Brazing is a widely used metal-joining process that involves melting a filler metal into the joint between two or more base metals. Flux plays a critical role in ensuring the success of the brazing process. It helps clean the metal surfaces, prevents oxidation, and promotes the flow of the filler metal. Without flux, achieving strong, durable, and defect-free joints can be challenging. Below are three key reasons why flux is essential in brazing, along with a detailed explanation of each.
Key Points Explained:
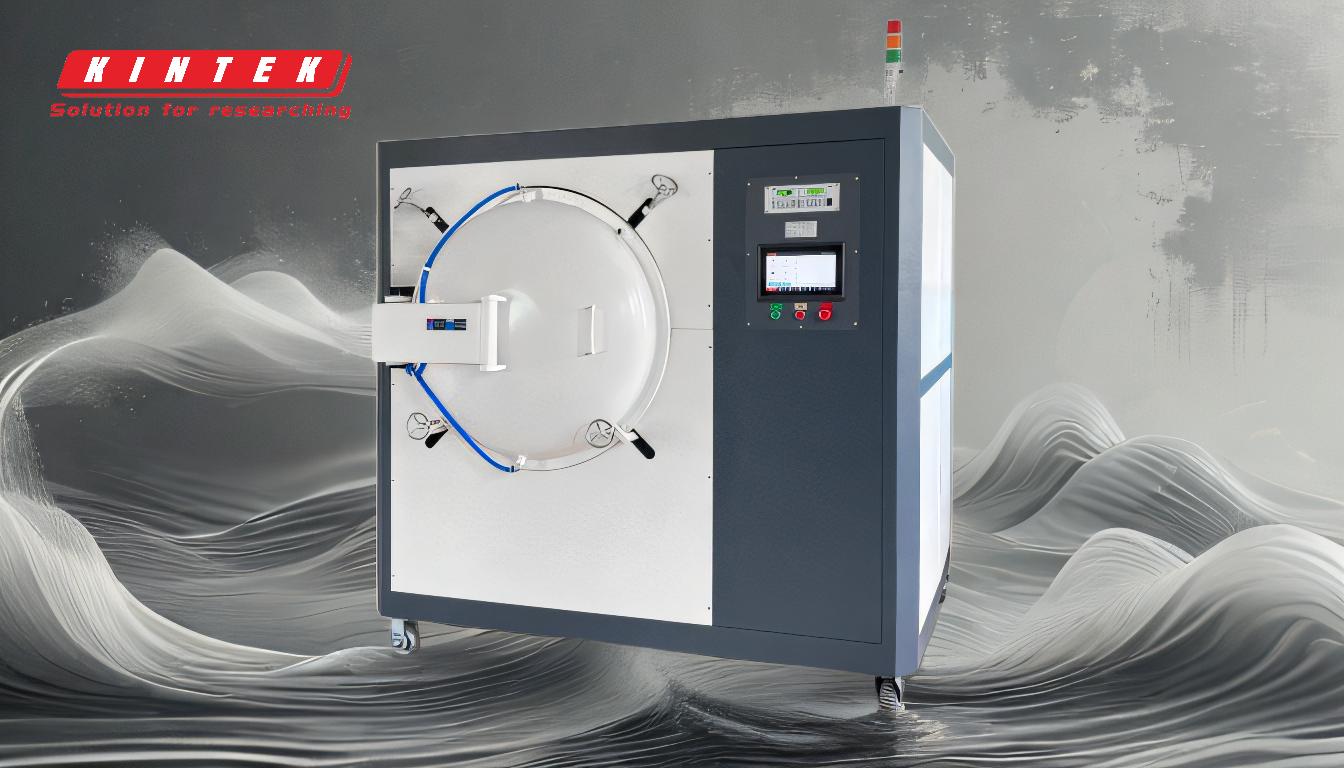
-
Cleaning Metal Surfaces for Better Adhesion
- During brazing, contaminants like oxides, oils, and dirt on the metal surfaces can hinder the filler metal from bonding properly. Flux acts as a cleaning agent, dissolving these impurities and ensuring the surfaces are ready for bonding.
- Flux removes oxides that form on the metal surfaces when exposed to heat. These oxides can create a barrier, preventing the filler metal from wetting the base metal. By eliminating oxides, flux ensures a clean surface, which is crucial for achieving a strong joint.
- This cleaning action is particularly important when working with metals like aluminum or stainless steel, which are prone to rapid oxidation. Without flux, the brazing process would likely result in weak or incomplete joints.
-
Preventing Oxidation During Heating
- When metals are heated, they react with oxygen in the air, forming oxides. These oxides can weaken the joint and interfere with the filler metal's ability to flow and bond.
- Flux creates a protective barrier over the metal surfaces, shielding them from oxygen during the heating process. This barrier prevents the formation of new oxides and ensures that the metal remains clean and reactive.
- The anti-oxidation properties of flux are especially critical in high-temperature brazing applications, where oxidation occurs more rapidly. By maintaining a clean surface, flux helps achieve consistent and high-quality joints.
-
Promoting Filler Metal Flow and Wetting
- For a successful brazed joint, the filler metal must flow evenly and wet the base metal surfaces. Wetting refers to the ability of the filler metal to spread and adhere to the base metal.
- Flux lowers the surface tension of the filler metal, allowing it to flow more easily into the joint. It also ensures that the filler metal wets the base metal uniformly, creating a strong and durable bond.
- Without flux, the filler metal might form beads or fail to spread properly, leading to weak or incomplete joints. Flux ensures that the filler metal flows smoothly and fills the joint completely, resulting in a reliable and long-lasting connection.
In summary, flux is indispensable in brazing because it cleans metal surfaces, prevents oxidation, and promotes the proper flow and wetting of the filler metal. These functions ensure that the brazed joint is strong, durable, and free from defects. Whether you're working with common metals or more challenging materials, using flux is a best practice for achieving high-quality brazed joints.
Summary Table:
Reason | Function |
---|---|
Cleans Metal Surfaces | Removes oxides, oils, and dirt for better adhesion and bonding. |
Prevents Oxidation During Heating | Forms a protective barrier to shield metals from oxygen and oxidation. |
Promotes Filler Metal Flow | Lowers surface tension, ensuring even wetting and strong, durable joints. |
Ready to achieve flawless brazed joints? Contact our experts today for guidance and solutions!