Pellet dies are critical components in pellet presses, used to compress powdered materials into pellets. They are typically made from high-strength materials to withstand the pressure and wear involved in the pelletizing process. The choice of material for pellet dies depends on the application, the type of material being pelletized, and the desired durability. Common materials include hardened steel, stainless steel, and sometimes tungsten carbide for highly abrasive materials. The design and material of the die must ensure that the pellets are formed consistently and that the die itself has a long service life.
Key Points Explained:
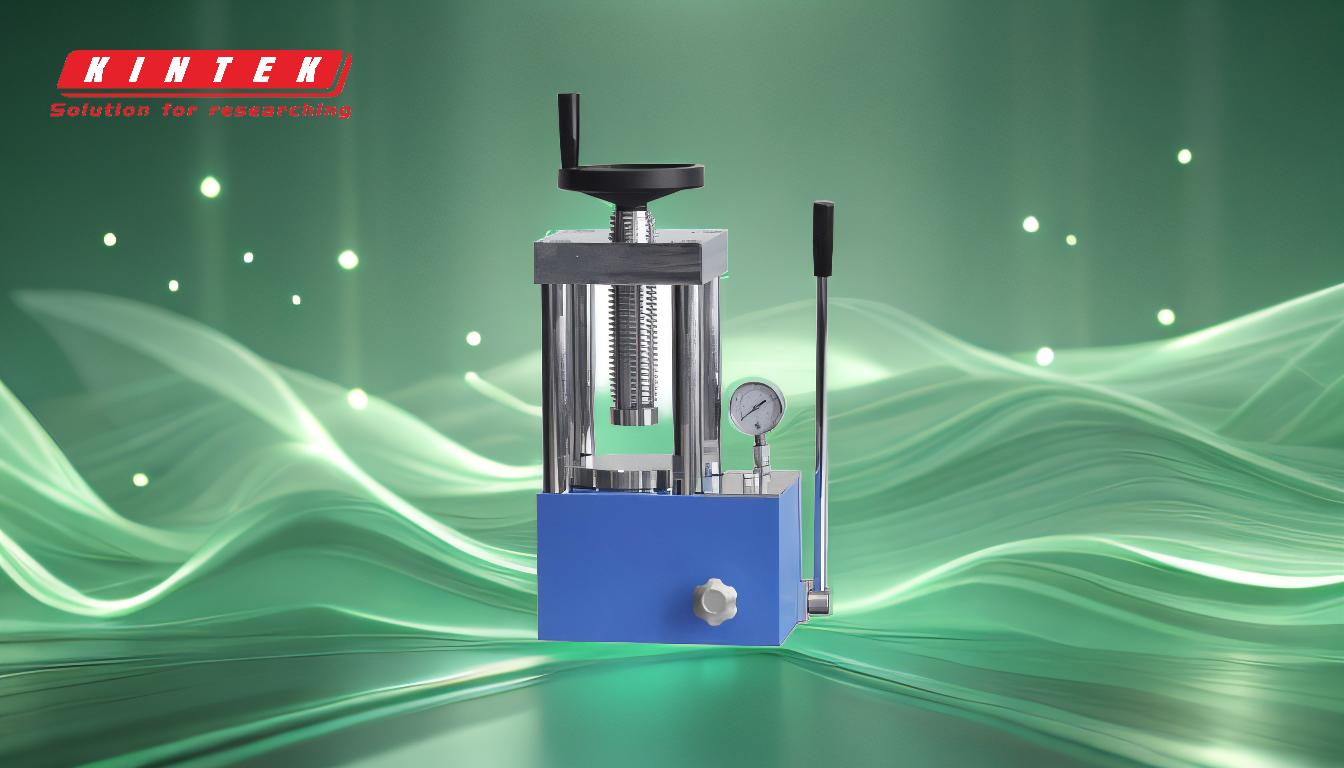
-
Materials Used in Pellet Dies:
- Hardened Steel: This is the most common material used for pellet dies due to its high strength and durability. It can withstand the high pressures required to compress powdered materials into pellets.
- Stainless Steel: Used in applications where corrosion resistance is important, such as in the food or pharmaceutical industries. Stainless steel dies are also easier to clean and maintain.
- Tungsten Carbide: For highly abrasive materials, tungsten carbide is used because of its exceptional hardness and wear resistance. This material is more expensive but offers a longer lifespan in demanding applications.
-
Design Considerations:
- Die Hole Size: The size of the die hole is crucial as it determines the diameter of the pellets. The hole size must be carefully chosen based on the expected particle diameter and the size of the raw material after crushing, which should be less than 5mm.
- Shape and Configuration: The shape of the die holes can vary (e.g., round, square, or custom shapes) depending on the desired pellet shape. The configuration of the holes (e.g., single or multiple holes) also affects the efficiency and output of the pellet press.
-
Application-Specific Requirements:
- Laboratory Applications: In settings like bomb calorimetry, where precision and consistency are critical, pellet dies must produce uniform pellets. The material and design must ensure that the pellets are free from defects and have consistent density.
- Industrial Applications: In industries where large quantities of pellets are produced, the durability and maintenance requirements of the dies are more significant. The choice of material must balance cost with the need for longevity and minimal downtime.
-
Maintenance and Longevity:
- Regular Maintenance: To ensure the longevity of pellet dies, regular maintenance is essential. This includes cleaning the dies to prevent material buildup and inspecting them for signs of wear or damage.
- Replacement and Refurbishment: Over time, even the most durable dies will wear out. Depending on the material and usage, dies may need to be refurbished or replaced to maintain the quality of the pellets.
In summary, pellet dies are made from materials like hardened steel, stainless steel, or tungsten carbide, chosen based on the application and the type of material being pelletized. The design of the die, including the size and shape of the holes, is critical to producing consistent and high-quality pellets. Regular maintenance is necessary to extend the life of the dies, and in some cases, refurbishment or replacement may be required to ensure continued performance.
Summary Table:
Material | Properties | Applications |
---|---|---|
Hardened Steel | High strength, durability, withstands high pressure | General pelletizing applications |
Stainless Steel | Corrosion-resistant, easy to clean and maintain | Food, pharmaceutical, and other industries requiring hygiene |
Tungsten Carbide | Exceptional hardness, wear resistance, longer lifespan | Highly abrasive materials and demanding applications |
Need help selecting the right pellet dies for your application? Contact our experts today for personalized advice!