Powder metallurgy is a versatile manufacturing process that offers numerous advantages, such as energy efficiency, cost-effectiveness, and the ability to produce complex, high-precision parts with minimal waste. It is particularly beneficial for industries like automotive and aerospace due to its ability to create homogenous and uniform parts with exceptional tolerances. However, it also has limitations, including size restrictions, challenges in producing highly complex shapes, and lower strength and ductility compared to traditional casting or forging methods. Despite these drawbacks, powder metallurgy remains a vital and eco-friendly technology in modern manufacturing.
Key Points Explained:
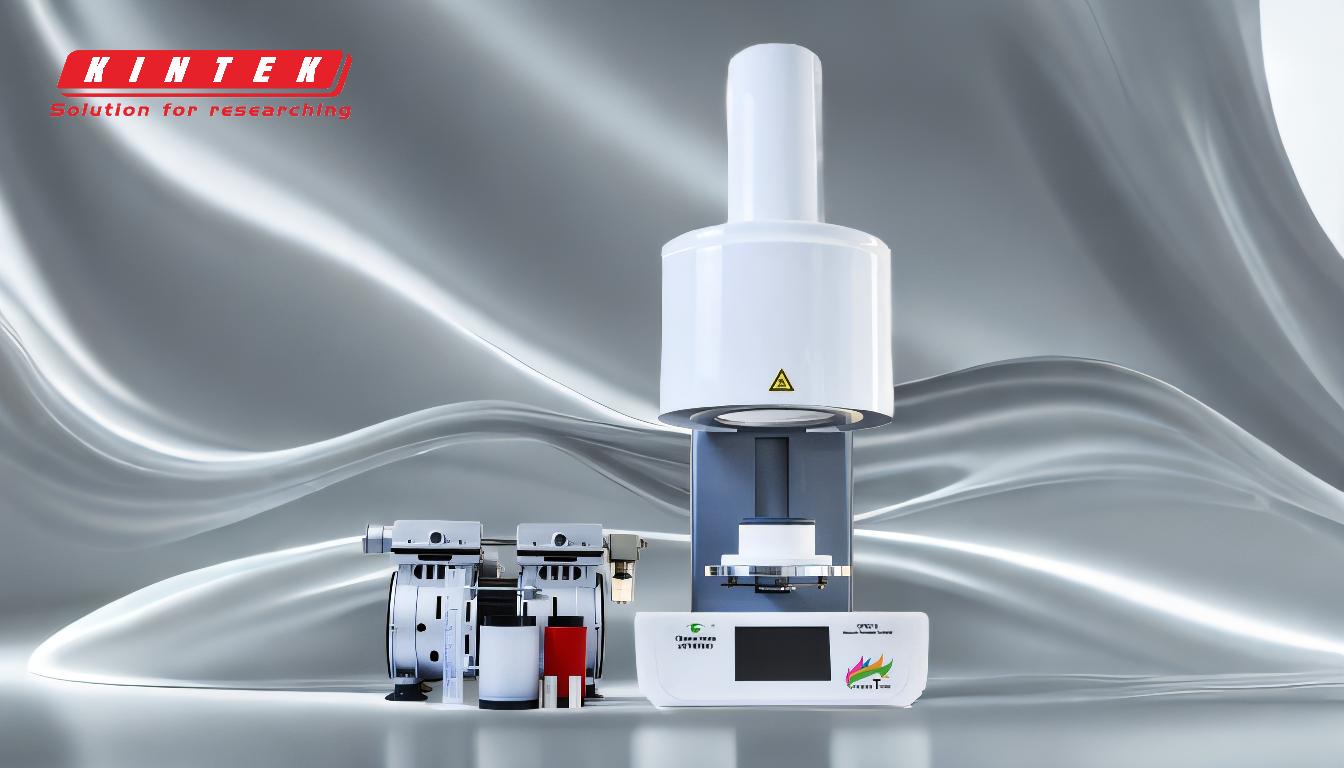
-
Advantages of Powder Metallurgy:
- Energy Efficiency and Cost-Effectiveness: Powder metallurgy is a short and efficient process that reduces energy consumption and material waste. Approximately 97% of the material used becomes part of the final product, minimizing scrap and lowering costs.
- Precision and Uniformity: The process allows for the creation of homogenous and uniform parts with exceptional tolerances, making it ideal for high-precision applications.
- Material Flexibility: Powder metallurgy enables the assembly of material structures to accurately control properties, making it suitable for producing high-value-added materials, especially alloys with high melting points or poor castability.
- Eco-Friendly Manufacturing: With minimal waste and no scrap, powder metallurgy is considered a green manufacturing technology, aligning with sustainable production practices.
-
Applications in Key Industries:
- Automotive and Aerospace: The ability to produce lightweight, durable, and high-precision components makes powder metallurgy a vital process for these industries.
- Hand Tools: Tools made using powder metallurgy exhibit superior wear resistance, toughness, and hardness retention, lasting up to five times longer than those made by other methods.
-
Disadvantages of Powder Metallurgy:
- Size Limitations: The largest presses in the industry are about 1,500 tons, which limits the practical size of parts to approximately 40-50 square inches of planar area.
- Complex Shapes: While skilled manufacturers can overcome some challenges, producing highly complex-shaped parts can still be difficult.
- Strength and Ductility: Powder metallurgy parts are generally not as strong or ductile as those produced by casting or forging, which may limit their use in applications requiring high mechanical performance.
-
Future Prospects:
- The precision and efficiency of powder metallurgy make it a promising technology for future manufacturing, particularly as industries continue to prioritize sustainability and high-performance materials. It is likely that more industries, including hand tool manufacturing, will adopt this method in the near future.
In summary, powder metallurgy offers significant advantages in terms of efficiency, precision, and sustainability, but it also has limitations in terms of part size, complexity, and mechanical properties. Understanding these trade-offs is crucial for manufacturers and purchasers when considering this technology for specific applications.
Summary Table:
Aspect | Advantages | Disadvantages |
---|---|---|
Energy Efficiency | Reduces energy consumption and material waste (97% material utilization). | Limited by press size (up to 1,500 tons). |
Precision & Uniformity | Produces homogenous, high-precision parts with exceptional tolerances. | Challenges in producing highly complex shapes. |
Material Flexibility | Enables control over material properties, ideal for high-value-added alloys. | Lower strength and ductility compared to casting or forging. |
Eco-Friendly | Minimal waste and no scrap, aligning with sustainable practices. | Part size limited to ~40-50 square inches. |
Discover how powder metallurgy can benefit your manufacturing process—contact our experts today!